Plasma Enhanced Chemical Vapor Deposition (PECVD) offers several advantages over traditional CVD methods, primarily due to the use of plasma to enhance chemical reactions. This technique allows for the deposition of high-quality thin films at lower temperatures, making it suitable for heat-sensitive substrates. PECVD is versatile, capable of depositing a wide range of materials with specific properties, such as wear resistance or insulation. It also provides excellent film uniformity, adhesion, and the ability to coat complex geometries. Additionally, PECVD systems, including MPCVD, are scalable and efficient, making them ideal for both research and industrial applications.
Key Points Explained:
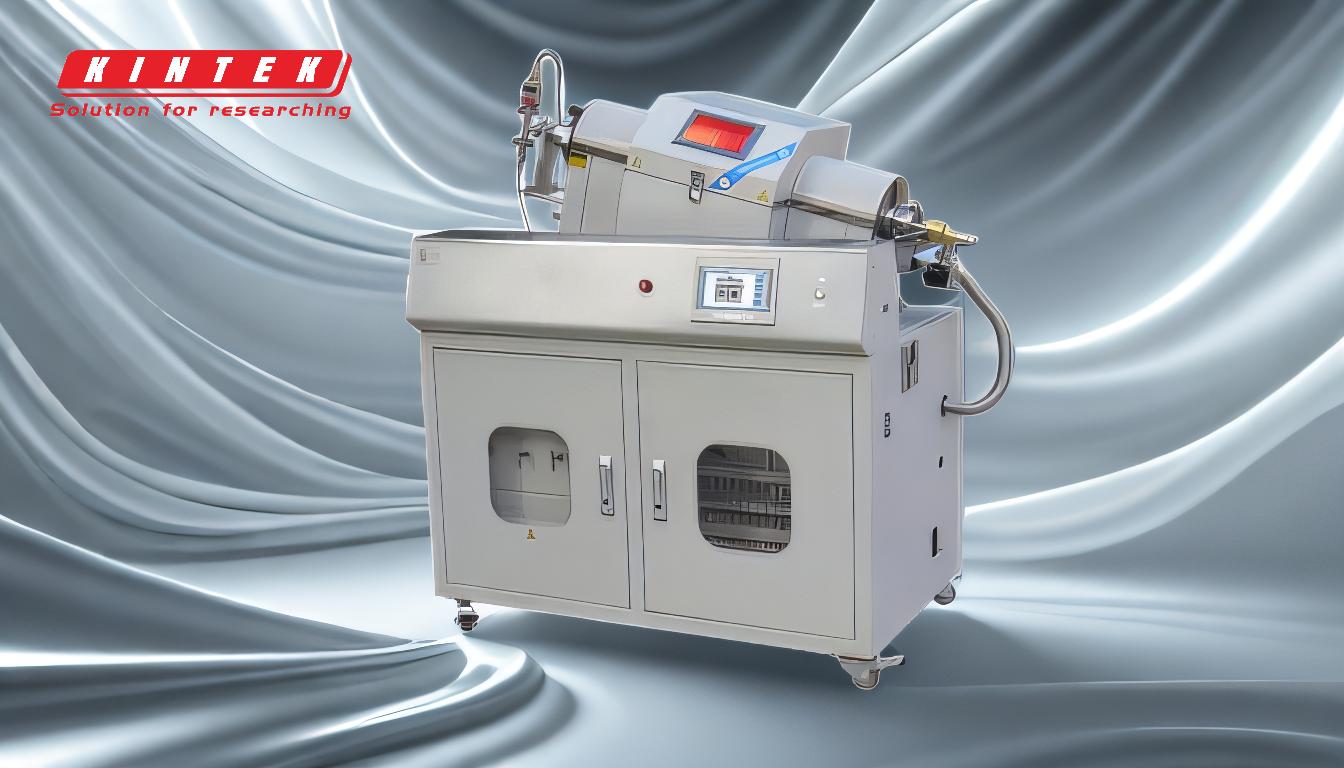
-
Lower Deposition Temperatures:
- PECVD operates at significantly lower temperatures compared to traditional CVD, often below 200°C. This is particularly advantageous for heat-sensitive substrates, such as polymers or certain metals, which might degrade or deform at higher temperatures.
-
Versatility in Material Deposition:
- PECVD can deposit a wide variety of materials, including metals, semiconductors, and ceramics. This versatility allows for the creation of thin films with specific properties, such as diamond-like carbon for wear resistance or silicon compounds for insulation.
-
High-Quality Thin Films:
- The use of plasma in PECVD results in thin films that are of high quality, with uniform thickness and excellent resistance to cracking. This uniformity is crucial for applications requiring precise control over film properties.
-
Good Adhesion:
- Films produced by PECVD exhibit strong adhesion to the substrate. This is essential for ensuring the durability and longevity of the coating, especially in harsh environments.
-
Coating Complex Geometries:
- PECVD is capable of coating parts with complex shapes and geometries. This is particularly useful in industries where components have intricate designs, such as in microelectronics or biomedical devices.
-
High Deposition Rates:
- PECVD offers high deposition rates, making it a fast and efficient process for producing large-area thin films. This efficiency is beneficial for both small-scale research and large-scale industrial production.
-
Scalability:
- PECVD systems, including MPCVD, are highly scalable. They can be used for a wide range of applications, from laboratory research to industrial manufacturing, making them a versatile choice for various industries.
-
Environmental Impact:
- Unlike some other deposition techniques, PECVD does not require chemical reagents or post-treatment cleaning, resulting in a lower environmental impact. This makes it a more sustainable option for thin film deposition.
In summary, PECVD, particularly when utilizing MPCVD, provides a powerful and flexible method for depositing high-quality thin films at lower temperatures, with excellent uniformity, adhesion, and the ability to coat complex geometries. Its scalability and efficiency make it a preferred choice for a wide range of applications, from research to industrial production.
Summary Table:
Advantage | Description |
---|---|
Lower Deposition Temperatures | Operates below 200°C, ideal for heat-sensitive substrates. |
Versatility in Material Deposition | Deposits metals, semiconductors, and ceramics with specific properties. |
High-Quality Thin Films | Uniform thickness, excellent resistance to cracking, and precise control. |
Good Adhesion | Strong adhesion to substrates, ensuring durability in harsh environments. |
Coating Complex Geometries | Capable of coating intricate designs, useful in microelectronics and biomedicine. |
High Deposition Rates | Fast and efficient for large-area thin film production. |
Scalability | Suitable for both research and industrial applications. |
Environmental Impact | No chemical reagents or post-treatment cleaning, reducing environmental impact. |
Learn how PECVD can revolutionize your thin film deposition process—contact our experts today!