Powder metallurgy is a highly efficient and versatile manufacturing process that offers numerous advantages, making it a preferred choice in various industries. It is characterized by its short process, energy efficiency, low cost, and minimal material waste. The process allows for the precise control of material properties by freely assembling material structures, making it a key player in green manufacturing. Additionally, powder metallurgy is eco-friendly, with 97% of the material used becoming part of the final product, significantly reducing waste and cost. It enables the blending of different metals and nonmetals into unique combinations, avoiding complex metallurgical procedures. The process is particularly economical for small metal parts and is the best method for preparing refractory metal sputtering targets. Furthermore, it allows for the creation of complex shapes with high precision and strength, making it ideal for automotive component production.
Key Points Explained:
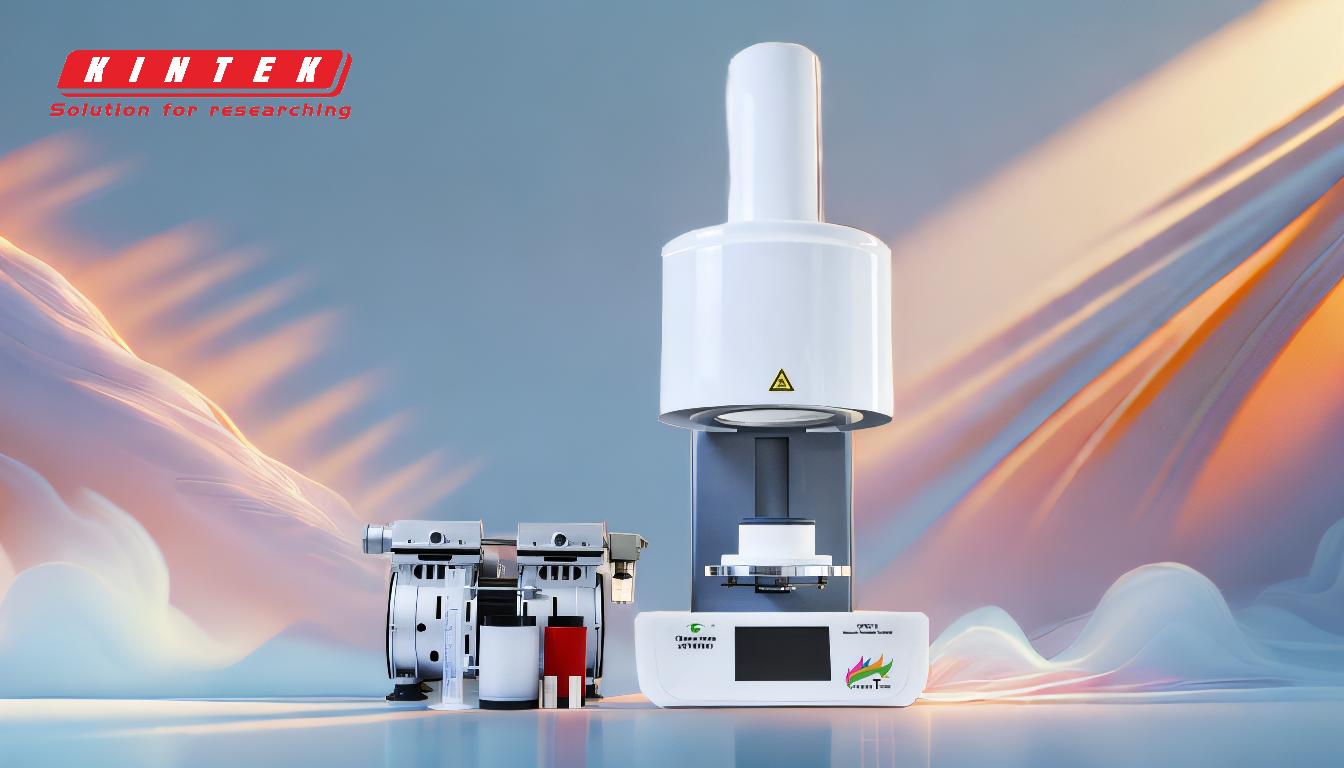
-
Short Process and Energy Efficiency:
- Powder metallurgy is known for its streamlined process, which significantly reduces the time and energy required compared to traditional manufacturing methods. This efficiency not only lowers production costs but also contributes to the sustainability of the manufacturing process.
-
Cost-Effectiveness:
- The process is cost-effective due to minimal material waste and reduced need for machining. For small metal parts, such as gears, powder metallurgy is often more economical than casting, as it avoids the considerable machining and scrap loss associated with casting.
-
Material Conservation and Eco-Friendliness:
- Powder metallurgy is highly eco-friendly, with 97% of the material used becoming part of the final product. This high material utilization rate results in very little waste and no scrap, providing significant environmental benefits and cost savings.
-
Versatility in Material Combinations:
- The process allows for the blending and mixing of different metals and nonmetals into a single product. This capability enables the creation of unique material combinations that would be difficult or impossible to achieve through traditional metallurgical methods.
-
Precision and Complex Shapes:
- Powder metallurgy excels in producing parts with complex external and internal shapes. The precision of the molds and dies used in the pressing phase, often made with centesimal tolerances using wire EDM, allows for the creation of intricate designs with high accuracy.
-
High Strength and Durability:
- The sintering process in powder metallurgy results in strong and durable parts. The uniform fine-grained structure obtained through this method enhances the mechanical properties of the final product, making it suitable for demanding applications.
-
Application in Automotive Industry:
- Powder metallurgy is particularly advantageous in the automotive industry, where it is used to produce complex configurations cost-effectively. The process allows for higher densities and strength in automotive components without the need for finishing or machining, further reducing production costs and time.
-
Preparation of Refractory Metal Sputtering Targets:
- Powder metallurgy is the best method for preparing refractory metal sputtering targets, especially for metals with large differences in melting points and densities. It is also suitable for inorganic non-metal targets and composite targets, where traditional melt casting methods are ineffective. The process offers advantages such as easily obtaining a uniform fine-grained structure, saving raw materials, and high production efficiency, making it a mainstay in the preparation of magnetron sputtering targets.
In summary, powder metallurgy offers a range of benefits that make it an attractive option for various manufacturing needs. Its efficiency, cost-effectiveness, material conservation, versatility, precision, and ability to produce strong and durable parts make it a vital part of modern manufacturing, particularly in industries such as automotive and aerospace.
Summary Table:
Advantage | Description |
---|---|
Short Process & Energy Efficiency | Streamlined process reduces time and energy, lowering production costs. |
Cost-Effectiveness | Minimal material waste and reduced machining needs make it economical. |
Material Conservation | 97% material utilization ensures eco-friendliness and cost savings. |
Versatility in Material Combinations | Blend metals and nonmetals for unique, complex material structures. |
Precision & Complex Shapes | Create intricate designs with high accuracy using precise molds and dies. |
High Strength & Durability | Sintering results in strong, durable parts with fine-grained structures. |
Automotive Industry Applications | Cost-effective production of complex automotive components with high strength. |
Refractory Metal Sputtering Targets | Best method for preparing sputtering targets with uniform fine-grained structures. |
Ready to leverage the benefits of powder metallurgy for your manufacturing needs? Contact our experts today!