Powder sintering, a fundamental process in powder metallurgy, offers numerous advantages that make it a preferred manufacturing method for a wide range of industries. This process involves compacting metal or ceramic powders and heating them to a temperature below their melting point, allowing particles to bond and form a solid structure. The benefits of powder sintering include high material purity, uniform porosity, the ability to create complex shapes, enhanced mechanical properties, cost efficiency, and environmental friendliness. These advantages make sintering a versatile and reliable technique for producing high-performance components with consistent quality.
Key Points Explained:
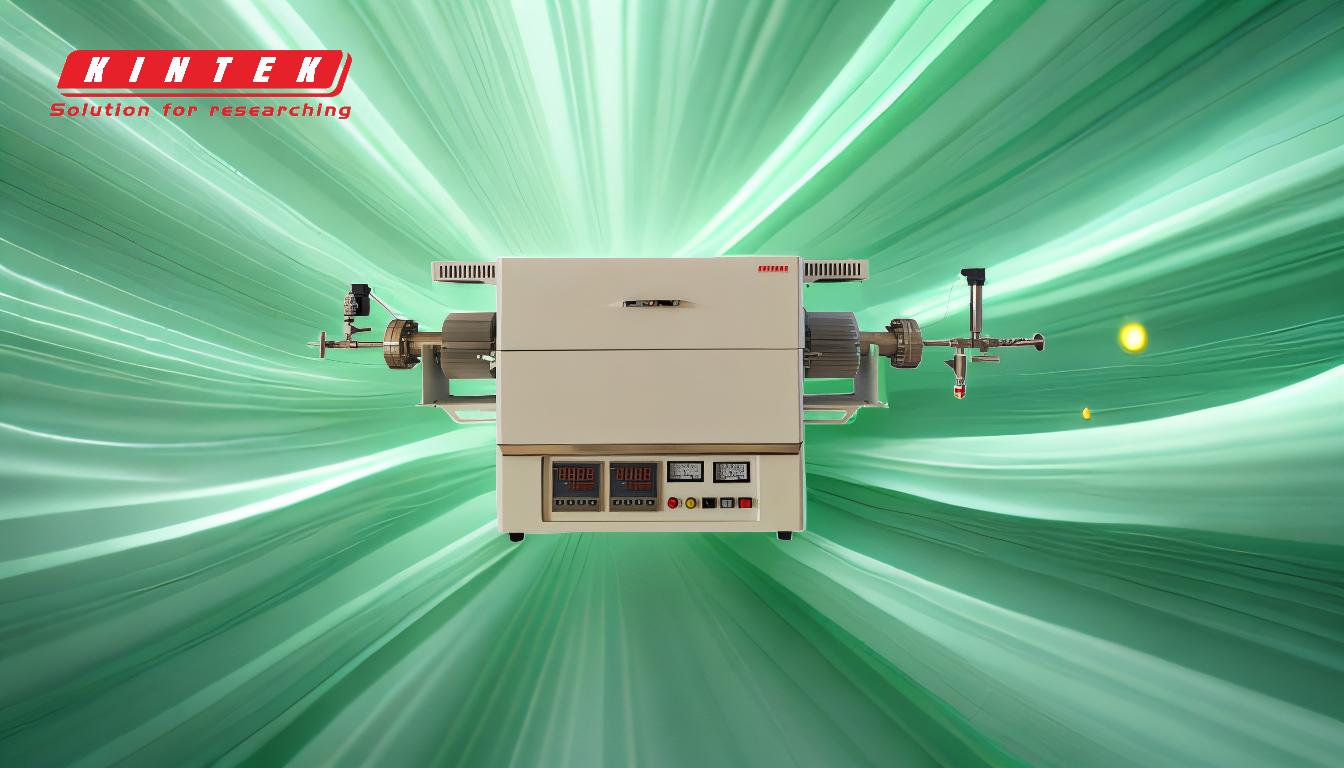
-
High Purity and Uniformity in Materials:
- Sintering ensures that the starting materials are of high purity, as the process eliminates impurities and contaminants. This results in uniform grain size and controlled porosity, which are critical for achieving consistent material properties. The absence of binding contacts or inclusions between powder particles further enhances the material's integrity.
-
Creation of Complex Shapes and Intricate Designs:
- One of the standout advantages of sintering is its ability to produce parts with highly complex geometries and intricate designs. This is particularly beneficial for industries such as aerospace, automotive, and medical devices, where components often require precise and sophisticated shapes. The process allows for the creation of nearly net-shaped objects, reducing the need for additional machining.
-
Enhanced Mechanical Properties:
- Sintering significantly improves the mechanical properties of materials, including strength, durability, and wear resistance. For example, turbine blades and other high-strength components are often manufactured using sintering due to the superior mechanical performance it imparts. The process also enhances properties like electrical conductivity, thermal conductivity, and translucency, depending on the material used.
-
Cost Efficiency and Material Savings:
- Sintering is a cost-effective manufacturing method, as it minimizes material waste. The process allows for the efficient use of raw materials, reducing overall production costs. Additionally, the ability to produce parts with high dimensional precision and good tolerance control further contributes to cost savings by reducing the need for post-processing.
-
Environmental Friendliness:
- Sintering is considered a green technology because it produces no harmful emissions and generates minimal waste. The process is energy-efficient and can be used to create environmentally friendly products, such as self-lubricating components and materials with vibration damping properties.
-
Versatility in Material Selection:
- Sintering is compatible with a wide range of materials, including metals, ceramics, and composites. This versatility allows manufacturers to tailor material compositions to meet specific performance requirements. For instance, sintering can be used to create unique isotropic materials with uniform properties in all directions.
-
Improved Surface Finish and Tolerance Control:
- Sintered parts typically exhibit excellent surface finishes and tight dimensional tolerances. This is particularly important for applications where surface quality and precision are critical, such as in medical implants or electronic components. The process also allows for the production of parts with uniform and controlled porosity, which can be advantageous in applications like filters or catalysts.
-
High Production Efficiency:
- Sintering is highly efficient for both low- and high-volume production. The process is repeatable and reliable, making it suitable for large-scale manufacturing. The ability to produce consistent, high-quality parts with minimal variation is a key advantage for industries that require mass production.
In summary, powder sintering offers a comprehensive set of advantages that make it an attractive choice for manufacturing high-performance components. From its ability to create complex shapes and enhance material properties to its cost efficiency and environmental benefits, sintering is a versatile and reliable process that meets the demands of modern industry.
Summary Table:
Advantage | Description |
---|---|
High Purity and Uniformity | Ensures high material purity, uniform grain size, and controlled porosity. |
Complex Shapes and Designs | Enables production of intricate, precise, and nearly net-shaped components. |
Enhanced Mechanical Properties | Improves strength, durability, wear resistance, and other material properties. |
Cost Efficiency | Minimizes material waste and reduces production costs. |
Environmental Friendliness | Produces no harmful emissions and is energy-efficient. |
Versatility in Material Selection | Compatible with metals, ceramics, and composites for tailored performance. |
Improved Surface Finish | Delivers excellent surface finishes and tight dimensional tolerances. |
High Production Efficiency | Suitable for both low- and high-volume manufacturing with consistent quality. |
Ready to leverage the benefits of powder sintering for your manufacturing needs? Contact us today to learn more!