RF sputtering offers several advantages over DC sputtering, particularly in terms of material versatility, process stability, and deposition quality. RF sputtering operates at lower pressures, reducing collisions and creating a more direct pathway for particles to reach the substrate. It is better suited for insulating materials due to its use of radio waves, which prevent charge buildup and arcing. Additionally, RF sputtering allows for a more uniform plasma distribution, higher plasma currents at lower pressures, and reduced target erosion, extending the target's lifetime. These features make RF sputtering ideal for applications requiring high-quality thin films on smaller substrates, especially with dielectric or insulating materials.
Key Points Explained:
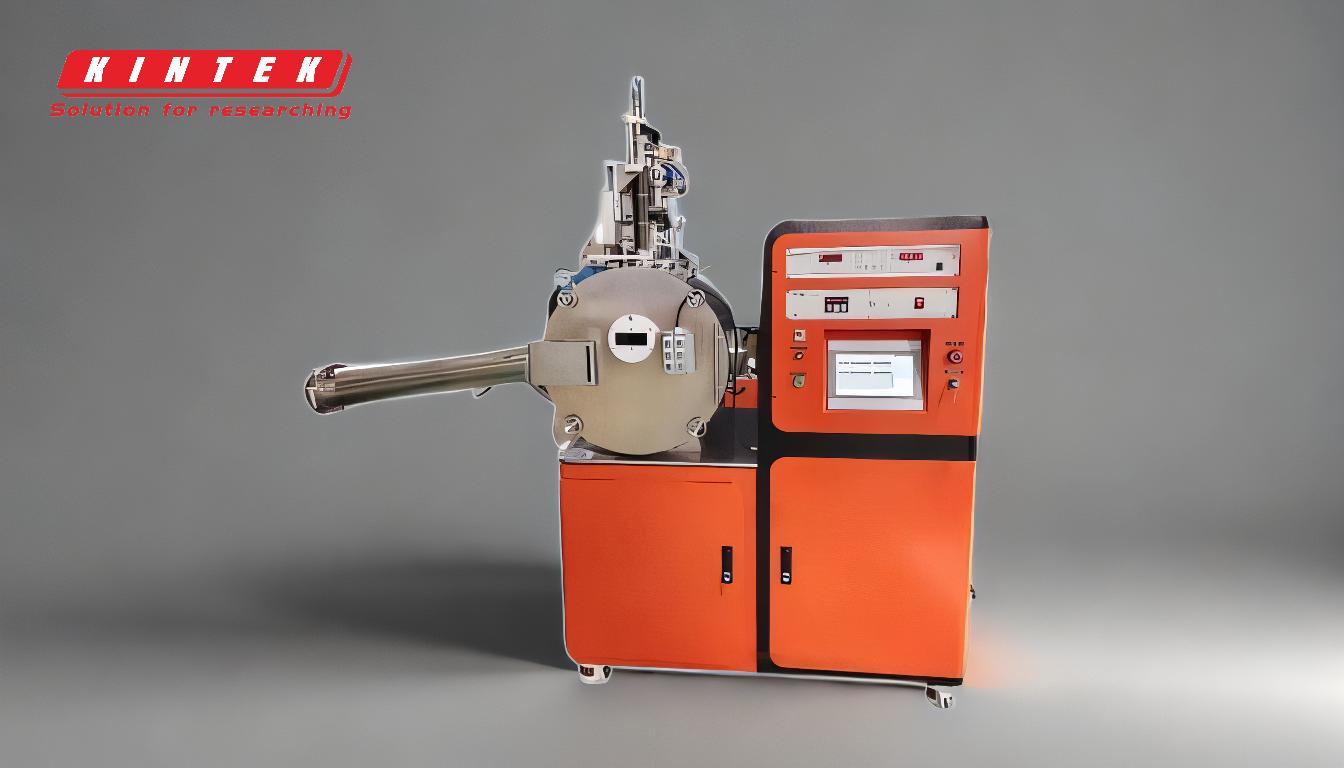
-
Lower Operating Pressure:
- RF sputtering operates at pressures less than 15 mTorr, compared to DC sputtering, which typically operates around 100 mTorr.
- Lower pressure reduces collisions between target material particles and gas ions, allowing for a more direct pathway of particles to the substrate.
- This results in higher deposition efficiency and better control over film quality.
-
Suitability for Insulating Materials:
- RF sputtering uses an alternating current (AC) power source, typically at 13.56 MHz, which prevents charge accumulation on the surface of insulating targets.
- This makes RF sputtering ideal for dielectric or non-conductive materials, which cannot be effectively sputtered using DC methods.
- The elimination of charge buildup also prevents plasma arcing, leading to smoother and more uniform thin films.
-
Extended Plasma Distribution:
- In RF sputtering, plasma formation is not limited to the cathode or target surface but can extend throughout the vacuum chamber.
- This broader plasma distribution enhances the uniformity of the deposition process and allows for more consistent film properties across the substrate.
-
Higher Plasma Currents at Lower Pressures:
- RF sputtering can maintain higher plasma currents at lower working pressures, which reduces collisions and increases the mean free path of target atoms.
- This results in higher energy particles reaching the substrate, improving film adhesion and density.
-
Reduced Target Erosion:
- RF sputtering involves a larger surface area of the target in the sputtering process, reducing localized "Race Track Erosion" commonly seen in DC sputtering.
- This extends the target's lifetime and reduces material waste, making RF sputtering more cost-effective for certain applications.
-
Elimination of Charge Buildup:
- The alternating voltage in RF sputtering prevents charge accumulation on the cathode surface, which is a common issue in DC sputtering.
- This prevents plasma arcing, leading to higher-quality thin films with fewer defects.
-
Versatility in Material Deposition:
- RF sputtering can deposit both conductive and non-conductive materials, making it a more versatile choice for a wide range of applications.
- This flexibility is particularly valuable in industries requiring precise thin-film deposition on complex or insulating substrates.
-
Improved Film Quality:
- The combination of lower pressure, reduced collisions, and elimination of charge buildup results in higher-quality thin films with better adhesion, uniformity, and density.
- This makes RF sputtering ideal for applications requiring high-performance coatings, such as in semiconductors, optics, and advanced materials research.
In summary, RF sputtering is a superior choice for applications requiring high-quality thin films on smaller substrates, especially when working with insulating or dielectric materials. Its advantages in process stability, material versatility, and deposition quality make it a preferred method in many advanced manufacturing and research settings.
Summary Table:
Advantage | Description |
---|---|
Lower Operating Pressure | Operates at <15 mTorr, reducing collisions for better film quality. |
Suitability for Insulating Materials | Prevents charge buildup, ideal for dielectric materials. |
Extended Plasma Distribution | Broader plasma ensures uniform deposition across substrates. |
Higher Plasma Currents | Maintains higher currents at lower pressures for improved film adhesion. |
Reduced Target Erosion | Minimizes localized erosion, extending target lifetime. |
Elimination of Charge Buildup | Prevents arcing, ensuring smoother, defect-free films. |
Versatility in Material Deposition | Works with conductive and non-conductive materials for diverse applications. |
Improved Film Quality | Produces high-performance coatings with better adhesion, uniformity, and density. |
Ready to elevate your thin-film deposition process? Contact us today to learn more about RF sputtering solutions!