Sintering ceramics, particularly fine ceramics, offers numerous advantages that make it a critical process in advanced material manufacturing. This process transforms ceramic powders into dense, high-performance materials with enhanced mechanical, thermal, and electrical properties. Key benefits include improved material purity, uniform microstructure, controlled porosity, and the ability to create complex shapes with high precision. Sintering also enhances properties like strength, conductivity, and durability while minimizing defects and impurities. These advantages make sintering indispensable for applications requiring high-performance ceramics, such as in aerospace, electronics, and medical devices.
Key Points Explained:
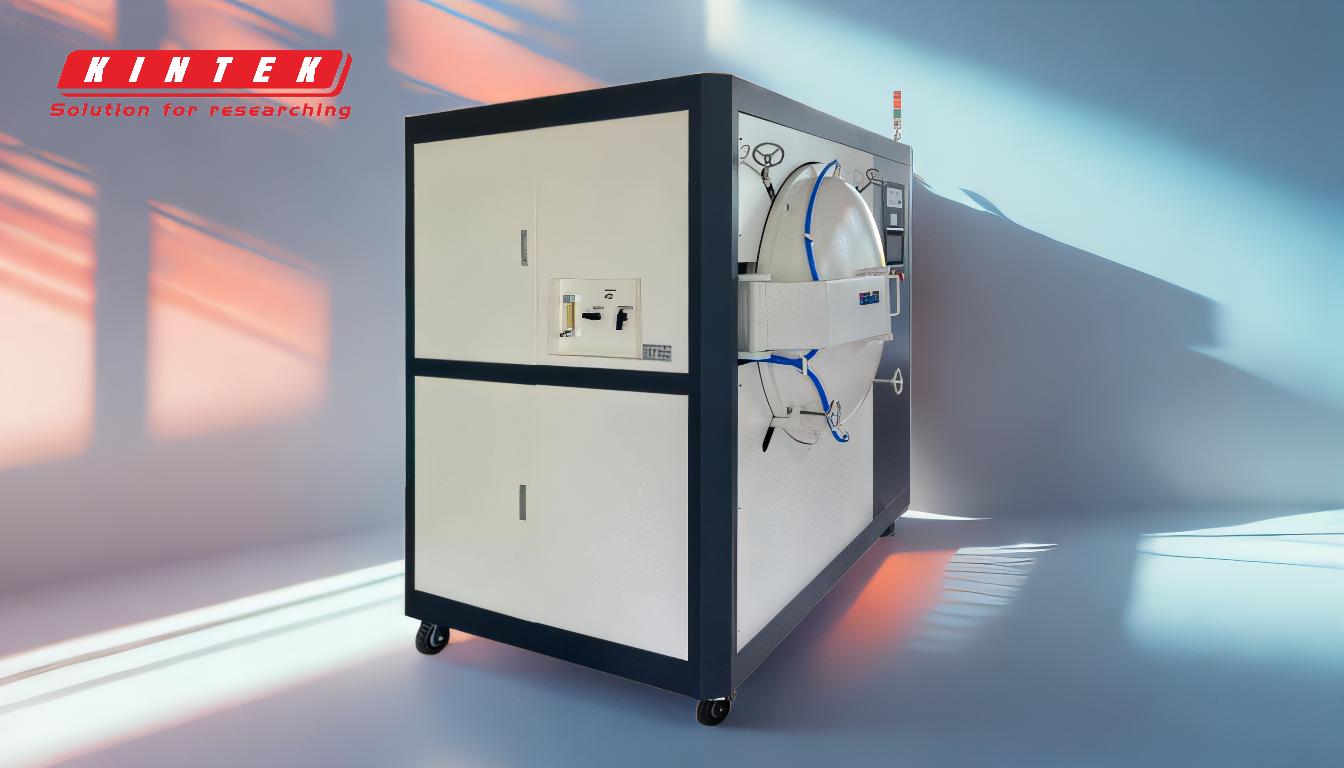
-
High Purity and Uniformity:
- Sintering ensures that the starting materials, such as ceramic powders, maintain high levels of purity and uniformity. This is crucial for achieving consistent material properties and performance in the final product.
- The process eliminates impurities and binding agents, resulting in a cleaner and more homogeneous material structure.
-
Controlled Microstructure and Grain Size:
- Sintering allows for precise control over the grain size and microstructure of the ceramics. This leads to highly repeatable operations and predictable material behavior.
- A uniform microstructure is essential for achieving desired mechanical, thermal, and electrical properties.
-
Reduced Surface Porosity:
- One of the primary advantages of sintering is its ability to minimize surface porosity. This enhances properties such as conductivity, corrosion resistance, and tensile strength.
- Low porosity also improves the material's durability and resistance to environmental factors.
-
Creation of Nearly Net-Shaped Objects:
- Sintering enables the production of complex, nearly net-shaped objects with minimal post-processing. This reduces material waste and manufacturing costs.
- The process is particularly beneficial for creating intricate components used in high-tech industries.
-
Enhanced Material Properties:
- Sintering significantly improves material properties such as thermal and electrical conductivity, mechanical strength, and translucency.
- These enhanced properties make sintered ceramics ideal for demanding applications, including turbine blades, electronic components, and medical implants.
-
Improved Mechanical Handling Strength:
- The sintering process strengthens the mechanical handling properties of ceramics, making them more resistant to cracking and deformation during manufacturing and use.
- This is particularly important for applications where the material is subjected to high stress or wear.
-
Ability to Work with Difficult Materials:
- Sintering is effective for processing materials with very high melting points, such as certain metals and ceramics, which are challenging to work with using traditional methods.
- This capability expands the range of materials that can be used in advanced manufacturing.
-
Consistency and Repeatability:
- The controlled nature of sintering ensures consistent product quality and repeatable results, which are critical for industrial applications.
- This reliability reduces the risk of defects and ensures that the final products meet stringent performance standards.
-
Environmental and Performance Benefits:
- Sintering produces less soot and oxidation compared to other metalworking techniques, resulting in cleaner, brighter, and higher-performing parts.
- This makes the process more environmentally friendly and suitable for producing high-quality components.
-
Transformation of Ceramic Powders:
- Sintering is the most critical step in preparing advanced ceramics, as it transforms ceramic powders into polycrystalline materials with specific properties.
- Through diffusion and mass transfer, sintering achieves densification, resulting in a stable shape, uniform microstructure, and excellent material properties.
In summary, sintering ceramics, especially fine ceramics, provides a wide range of advantages that are essential for producing high-performance materials. These benefits include improved purity, controlled microstructure, reduced porosity, enhanced material properties, and the ability to create complex shapes with precision. These qualities make sintered ceramics indispensable in industries requiring advanced materials with superior performance characteristics.
Summary Table:
Advantage | Description |
---|---|
High Purity and Uniformity | Ensures clean, homogeneous material structure with consistent properties. |
Controlled Microstructure | Precise grain size control for repeatable and predictable material behavior. |
Reduced Surface Porosity | Enhances conductivity, corrosion resistance, and tensile strength. |
Creation of Nearly Net-Shaped Objects | Produces complex shapes with minimal post-processing, reducing waste and costs. |
Enhanced Material Properties | Improves strength, conductivity, translucency, and durability. |
Improved Mechanical Handling Strength | Increases resistance to cracking and deformation under stress. |
Works with Difficult Materials | Processes high-melting-point materials effectively. |
Consistency and Repeatability | Ensures reliable, defect-free production for industrial applications. |
Environmental Benefits | Produces cleaner, brighter parts with less soot and oxidation. |
Transformation of Ceramic Powders | Converts powders into dense, polycrystalline materials with excellent properties. |
Ready to enhance your material performance? Contact us today to learn more about sintering ceramics!