Sintering is a critical process in metal production that offers numerous advantages, making it a preferred method for manufacturing high-performance components. It involves heating powdered materials below their melting point to bond particles, resulting in improved material properties and structural integrity. Key benefits include enhanced strength, reduced porosity, improved electrical and thermal conductivity, and the ability to produce complex shapes. Sintering also allows for tailored material compositions, cost-effectiveness, and versatility in material selection. These advantages make sintering indispensable in industries requiring precision, durability, and consistency in metal components.
Key Points Explained:
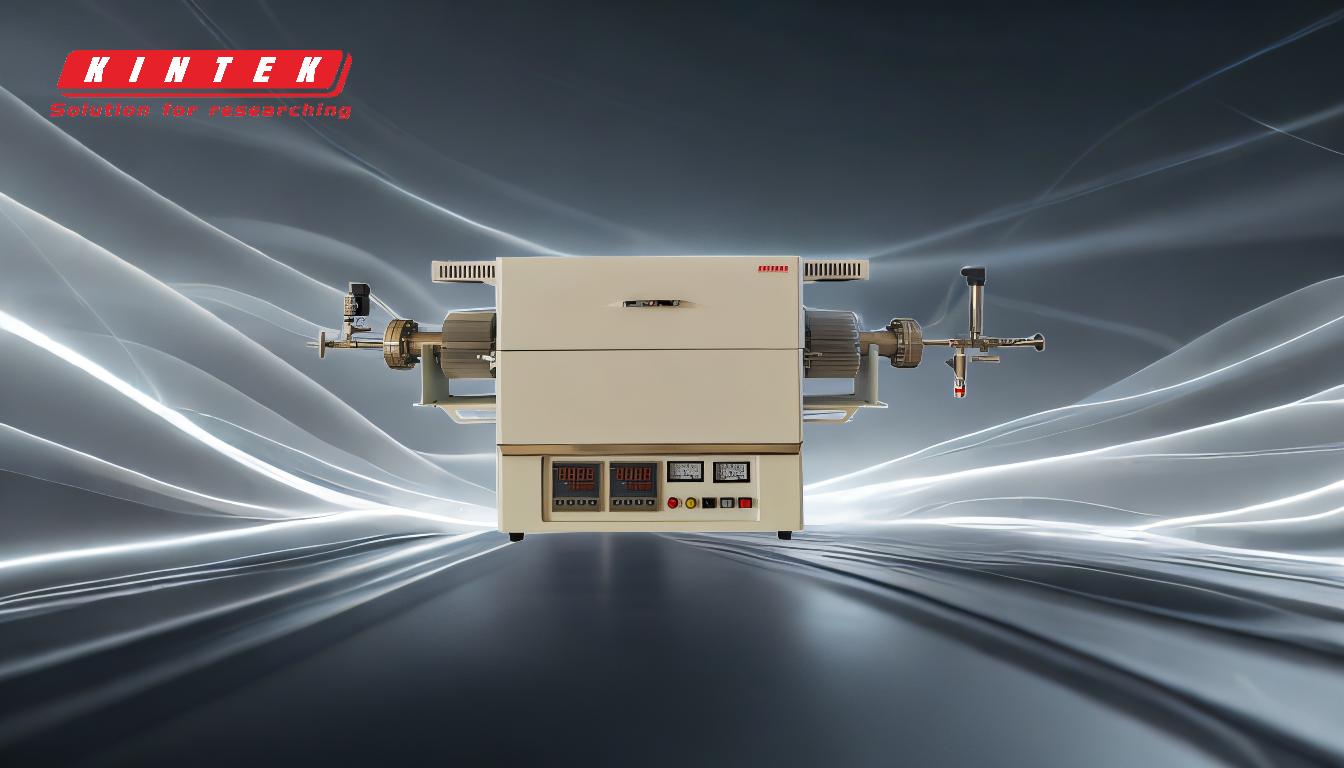
-
Enhanced Material Properties:
- Strength and Durability: Sintering develops sintered necks between particles, reducing pores and increasing the overall strength and durability of the material. This is particularly beneficial for components subjected to high stress or wear.
- Electrical and Thermal Conductivity: The process improves electrical and thermal conductivity by reducing porosity and enhancing particle bonding, making it ideal for applications requiring efficient heat or electricity transfer.
- Translucency and Transparency: In some materials, sintering can enhance translucency or transparency, which is useful in specialized applications like optical components.
-
Reduced Porosity:
- Sintering effectively reduces porosity, leading to denser and more uniform materials. This is crucial for applications where structural integrity and leak-tightness are essential, such as in filters, catalysts, or high-pressure components.
-
Complex Shape Production:
- The process allows for the creation of components with intricate designs and complex geometries that would be difficult or impossible to achieve with traditional manufacturing methods. This is particularly advantageous in industries like aerospace, automotive, and medical devices.
-
Tailored Material Compositions:
- Sintering enables the integration of different elements (e.g., nickel, copper, graphite) into the material matrix, allowing for customized properties such as improved wear resistance, thermal stability, or electrical performance.
-
Cost-Effectiveness:
- By eliminating the need for melting and reducing material waste, sintering is a cost-effective manufacturing method. It also minimizes the use of lubricants and reduces surface oxygen, further lowering production costs.
-
Versatility in Material Selection:
- Sintering can be applied to a wide range of materials, including metals with high melting points, ceramics, and composites. This versatility makes it suitable for diverse industries and applications.
-
Consistency and Control in Production:
- The sintering process offers precise control over material properties and dimensions, ensuring consistent quality and performance across batches. This is critical for industries requiring high reliability and precision.
-
Applications in Specialized Industries:
- Sintering is used to manufacture a variety of products, including bearings, jewelry, heat pipes, and shotgun shells. Its ability to enhance specific properties like gas absorbency (in filters or catalysts) makes it invaluable in niche applications.
In summary, sintering is a versatile and efficient process that significantly improves the properties of metal components while offering cost savings and design flexibility. Its ability to reduce porosity, enhance strength, and enable complex shapes makes it a cornerstone of modern metal production.
Summary Table:
Key Advantage | Description |
---|---|
Enhanced Strength & Durability | Reduces pores, increases strength, and improves wear resistance. |
Improved Conductivity | Enhances electrical and thermal conductivity for efficient heat and energy transfer. |
Reduced Porosity | Produces denser, leak-tight materials for high-pressure applications. |
Complex Shape Production | Enables intricate designs and geometries for specialized industries. |
Tailored Material Compositions | Allows customization for wear resistance, thermal stability, and electrical performance. |
Cost-Effectiveness | Reduces material waste, eliminates melting, and lowers production costs. |
Versatility in Material Selection | Suitable for metals, ceramics, and composites across diverse industries. |
Consistent Production Quality | Ensures reliable and precise material properties for high-performance applications. |
Learn how sintering can transform your metal production process—contact our experts today!