Two-plate molds are widely used in injection molding due to their cost-effectiveness and simplicity. Compared to multi-plate molds, they are less expensive to manufacture and maintain, making them a practical choice for many applications. Their straightforward design reduces complexity, which translates to lower production and operational costs. Additionally, two-plate molds are easier to operate and maintain, further enhancing their appeal for manufacturers seeking reliable and economical solutions.
Key Points Explained:
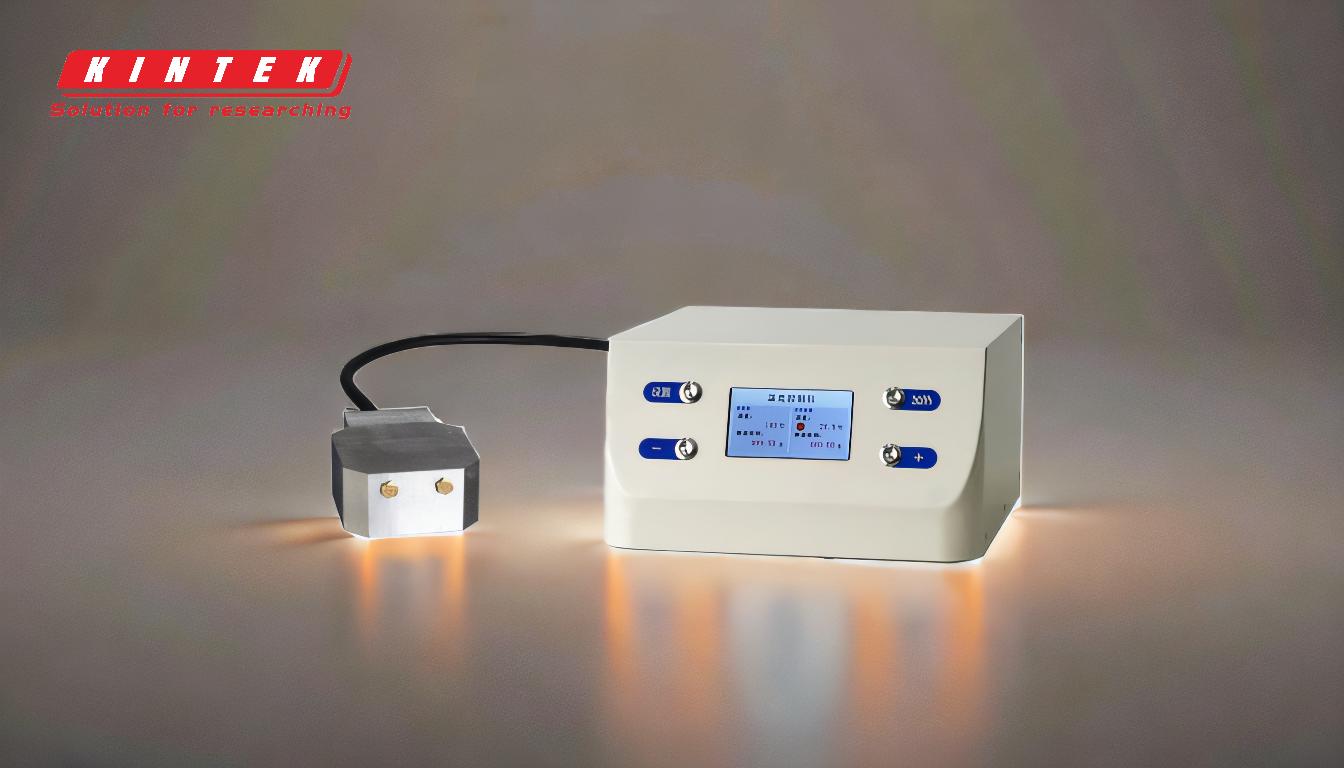
-
Lower Manufacturing Costs:
- Two-plate molds have a simpler design compared to multi-plate molds, which reduces the complexity of the manufacturing process.
- The reduced complexity means fewer parts are required, leading to lower material and labor costs.
- This makes two-plate molds a more affordable option for many manufacturers, especially for high-volume production.
-
Reduced Maintenance Costs:
- The straightforward design of two-plate molds makes them easier to maintain.
- Fewer components mean there are fewer parts that can wear out or require replacement, reducing long-term maintenance expenses.
- Maintenance procedures are simpler and less time-consuming, which minimizes downtime and keeps production lines running efficiently.
-
Ease of Operation:
- Two-plate molds are easier to operate due to their simpler design and fewer moving parts.
- Operators require less training to work with these molds, which can reduce labor costs and improve operational efficiency.
- The simplicity of the design also reduces the likelihood of operational errors, leading to fewer defects and higher-quality products.
-
Cost-Effectiveness:
- The combination of lower manufacturing and maintenance costs makes two-plate molds a cost-effective solution for many injection molding applications.
- Their affordability and reliability make them an attractive option for manufacturers looking to optimize their production processes without compromising on quality.
-
Versatility and Reliability:
- Two-plate molds are suitable for a wide range of products and materials, making them a versatile choice for various industries.
- Their reliable performance and ease of use ensure consistent production quality, which is crucial for meeting customer demands and maintaining competitive advantage.
In summary, two-plate molds offer significant advantages in terms of cost, maintenance, and ease of operation. These benefits make them a preferred choice for many manufacturers seeking efficient and economical injection molding solutions.
Summary Table:
Advantage | Description |
---|---|
Lower Manufacturing Costs | Simpler design reduces material and labor costs, ideal for high-volume production. |
Reduced Maintenance Costs | Fewer components mean less wear, lower replacement costs, and minimal downtime. |
Ease of Operation | Simpler design requires less training, reduces errors, and improves efficiency. |
Cost-Effectiveness | Combines low manufacturing and maintenance costs for economical production. |
Versatility and Reliability | Suitable for diverse materials and industries, ensuring consistent quality. |
Optimize your injection molding process with two-plate molds—contact us today for expert guidance!