Compression molding is a versatile manufacturing process used across various industries to produce high-quality, durable, and complex-shaped parts. It involves placing pre-measured material, such as rubber or thermosetting plastics, into a mold cavity. The mold is then closed, and heat and pressure are applied, causing the material to flow and fill the cavity. Excess material, known as mold flash, is expelled through grooves. This method is particularly valued for its ability to produce strong, consistent, and detailed parts with minimal waste. Below, we explore the key applications and advantages of compression molding in detail.
Key Points Explained:
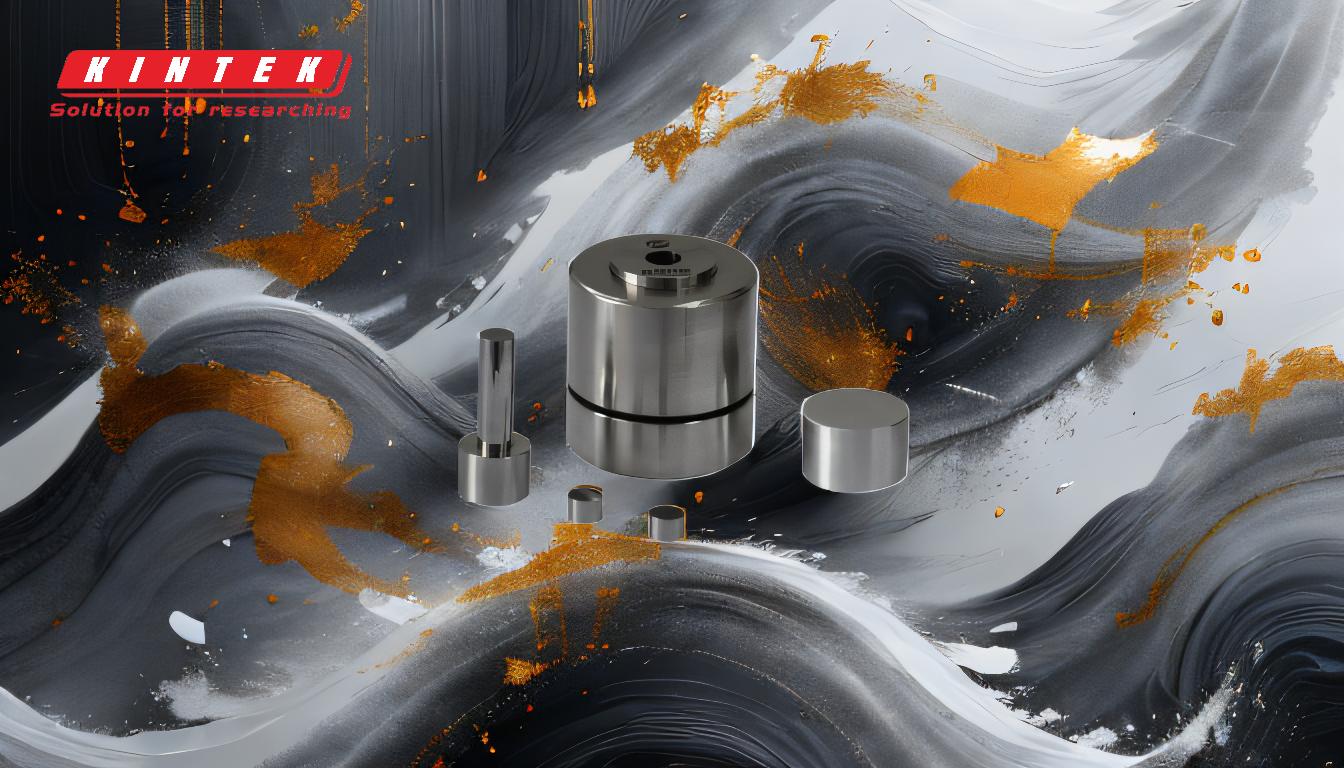
-
Automotive Industry Applications
- Compression molding is widely used in the automotive sector to manufacture components such as gaskets, seals, and rubber parts.
- These parts require high durability, resistance to heat, and precise dimensions, which compression molding can reliably achieve.
- For example, rubber seals for car doors and windows are often produced using this method due to their need for tight tolerances and long-lasting performance.
-
Electrical and Electronics Industry
- The process is ideal for creating insulating components, such as switchgear parts, circuit breakers, and connectors.
- Thermosetting plastics used in compression molding provide excellent electrical insulation and heat resistance, making them suitable for high-performance electrical applications.
- The ability to produce intricate shapes ensures that components fit perfectly into electronic devices.
-
Consumer Goods Production
- Compression molding is used to manufacture everyday items such as kitchenware, appliance handles, and plastic containers.
- The process allows for the production of aesthetically pleasing and durable products with consistent quality.
- For instance, heat-resistant handles for cookware are often made using this technique.
-
Aerospace and Defense Applications
- In aerospace, compression molding is used to create lightweight, high-strength components such as composite panels and structural parts.
- The process ensures that parts meet stringent safety and performance standards required in these industries.
- Materials like advanced composites can be molded to produce parts that withstand extreme conditions.
-
Medical Device Manufacturing
- Compression molding is employed to produce medical-grade components such as syringe plungers, seals, and housings for medical devices.
- The process ensures that these parts are biocompatible, precise, and free from contaminants.
- The ability to use sterilizable materials makes it a preferred method for medical applications.
-
Advantages of Compression Molding
- Cost-Effectiveness: The process minimizes material waste, making it economical for large-scale production.
- High Strength and Durability: The molded parts exhibit excellent mechanical properties due to the uniform distribution of material under pressure.
- Design Flexibility: Complex shapes and intricate details can be achieved with high precision.
- Material Versatility: A wide range of materials, including rubber, thermosetting plastics, and composites, can be used.
-
Limitations and Considerations
- While compression molding offers numerous benefits, it has some limitations, such as longer cycle times compared to injection molding.
- The process may not be suitable for very high-volume production where speed is critical.
- Tooling costs can be high for complex molds, making it less economical for small production runs.
In summary, compression molding is a highly adaptable and efficient manufacturing process with applications spanning automotive, electronics, consumer goods, aerospace, and medical industries. Its ability to produce strong, precise, and durable parts makes it a preferred choice for many manufacturers. However, it is essential to consider the specific requirements of the application, such as production volume and material properties, to determine if compression molding is the most suitable method.
Summary Table:
Industry | Applications |
---|---|
Automotive | Gaskets, seals, rubber parts (e.g., car door seals) |
Electrical & Electronics | Insulating components (e.g., switchgear parts, circuit breakers) |
Consumer Goods | Kitchenware, appliance handles, plastic containers |
Aerospace & Defense | Lightweight composite panels, structural parts |
Medical Devices | Syringe plungers, seals, housings for medical devices |
Want to leverage compression molding for your industry? Contact our experts today to learn more!