Industrial furnaces are versatile tools used across a wide range of industries for various thermal processes. Their ability to maintain high temperatures for extended periods makes them indispensable in applications such as metal processing, material synthesis, and laboratory testing. From annealing and tempering to curing and sintering, industrial furnaces play a critical role in achieving desired material properties, joining metals, and removing impurities. They are particularly valuable in large-scale steel projects, where precision and consistency in heat treatment are essential. Below, we explore the key applications of industrial furnaces in detail.
Key Points Explained:
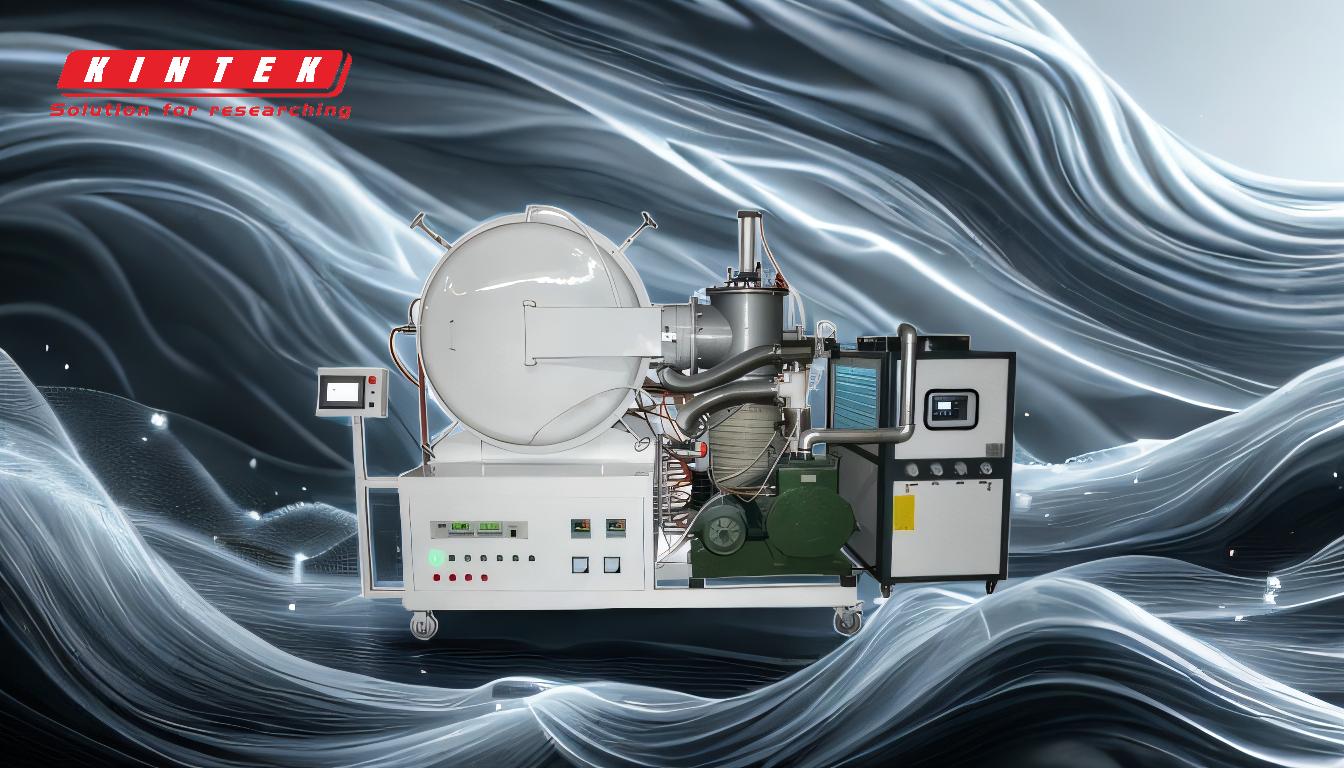
-
Annealing
- Purpose: Softening work-hardened materials to make them more ductile and suitable for further cold working.
- Process: The material is heated to a specific temperature, held for a set time, and then cooled slowly.
- Applications: Used in metalworking industries to improve machinability and reduce internal stresses in materials like steel, copper, and aluminum.
-
Smelting
- Purpose: Extracting metal from its ore by heating it to high temperatures.
- Process: The furnace melts the ore, separating the metal from impurities.
- Applications: Essential in the production of metals like iron, copper, and aluminum for construction, manufacturing, and electronics.
-
Tempering
- Purpose: Increasing the toughness of metals by reducing brittleness.
- Process: The metal is heated to a temperature below its critical point and then cooled.
- Applications: Commonly used in the production of tools, gears, and structural components.
-
Aging
- Purpose: Altering the properties of certain alloys over time and temperature.
- Process: The material is held at an elevated temperature to achieve desired mechanical properties.
- Applications: Used in aerospace and automotive industries for aluminum and titanium alloys.
-
Baking
- Purpose: Removing entrained gases from materials.
- Process: The material is heated to release trapped gases.
- Applications: Critical in the production of ceramics, glass, and certain metals.
-
Brazing and Soldering
- Purpose: Joining metal parts using a filler material.
- Process: The filler material (e.g., brass) is melted to bond the parts.
- Applications: Widely used in electronics, plumbing, and automotive manufacturing.
-
Burning Off
- Purpose: Removing cured coatings or contaminants from surfaces.
- Process: High temperatures are used to oxidize and remove unwanted materials.
- Applications: Used in surface preparation for painting or coating.
-
Curing
- Purpose: Changing the properties of materials through chemical or physical processes.
- Process: The material is heated to initiate curing reactions.
- Applications: Common in the production of composites, adhesives, and coatings.
-
Drying
- Purpose: Removing moisture from materials.
- Process: The material is heated to evaporate water or solvents.
- Applications: Used in the production of ceramics, pharmaceuticals, and food products.
-
Firing and Sintering
- Purpose: Bonding particle surfaces in powders to form solid materials.
- Process: The powder is heated to just below its melting point.
- Applications: Essential in the production of ceramics, metals, and advanced materials.
-
Casting and Melting
- Purpose: Melting metals for casting into shapes.
- Process: The metal is heated until molten and then poured into molds.
- Applications: Used in foundries for manufacturing engine parts, tools, and machinery.
-
Heat Treatment
- Purpose: Altering the physical and mechanical properties of metals through controlled heating and cooling.
- Process: Includes processes like hardening, tempering, and annealing.
- Applications: Critical in the production of automotive components, aerospace parts, and industrial machinery.
-
Hot Pressing
- Purpose: Densifying materials using heat and pressure.
- Process: The material is compressed while being heated.
- Applications: Used in the production of advanced ceramics and composites.
-
Laboratory Work
- Purpose: Conducting thermal processing and testing.
- Process: Precise temperature control is used for experiments and material characterization.
- Applications: Essential in research and development for new materials and processes.
-
Preheating
- Purpose: Heating materials prior to austenitizing or other processes.
- Process: The material is heated to a specific temperature to prepare it for further treatment.
- Applications: Used in welding and heat treatment to prevent cracking and improve results.
-
Quenching
- Purpose: Rapidly cooling materials to achieve desired properties.
- Process: The material is heated and then quickly cooled in water, oil, or air.
- Applications: Used in the production of hardened steel components.
-
Specialized Applications
- Purpose: Addressing unique industrial needs.
- Examples: Includes processes like carburizing (adding carbon to steel surfaces) and nitriding (introducing nitrogen into metal surfaces).
- Applications: Used in industries requiring high wear resistance and surface hardness.
Industrial furnaces are indispensable in modern manufacturing and material processing. Their ability to perform a wide range of thermal processes with precision and consistency makes them a cornerstone of industries such as automotive, aerospace, electronics, and construction. Whether it's for large-scale steel production or specialized laboratory testing, industrial furnaces provide the thermal control needed to achieve desired material properties and product performance.
Summary Table:
Application | Purpose | Process | Industries |
---|---|---|---|
Annealing | Soften materials for better ductility and cold working | Heat to a specific temperature, hold, and cool slowly | Metalworking (steel, copper, aluminum) |
Smelting | Extract metal from ore | Melt ore to separate metal from impurities | Construction, manufacturing, electronics |
Tempering | Increase metal toughness by reducing brittleness | Heat below critical point and cool | Tools, gears, structural components |
Aging | Alter alloy properties over time and temperature | Hold at elevated temperature | Aerospace, automotive (aluminum, titanium) |
Baking | Remove entrained gases from materials | Heat to release trapped gases | Ceramics, glass, metals |
Brazing & Soldering | Join metal parts using filler material | Melt filler (e.g., brass) to bond parts | Electronics, plumbing, automotive |
Burning Off | Remove coatings or contaminants | Use high temperatures to oxidize and remove materials | Surface preparation for painting/coating |
Curing | Change material properties through chemical/physical processes | Heat to initiate curing reactions | Composites, adhesives, coatings |
Drying | Remove moisture from materials | Heat to evaporate water/solvents | Ceramics, pharmaceuticals, food |
Firing & Sintering | Bond particle surfaces in powders | Heat just below melting point | Ceramics, metals, advanced materials |
Casting & Melting | Melt metals for casting | Heat until molten and pour into molds | Foundries (engine parts, tools, machinery) |
Heat Treatment | Alter metal properties through controlled heating/cooling | Includes hardening, tempering, annealing | Automotive, aerospace, industrial machinery |
Hot Pressing | Densify materials using heat and pressure | Compress while heating | Advanced ceramics, composites |
Laboratory Work | Conduct thermal processing and testing | Precise temperature control for experiments | Research and development |
Preheating | Heat materials prior to further treatment | Heat to specific temperature | Welding, heat treatment |
Quenching | Rapidly cool materials to achieve desired properties | Heat and cool quickly in water, oil, or air | Hardened steel components |
Specialized Apps | Address unique industrial needs (e.g., carburizing, nitriding) | Add carbon/nitrogen to metal surfaces | High wear resistance and surface hardness industries |
Discover how industrial furnaces can transform your processes—contact our experts today for tailored solutions!