Physical Vapor Deposition (PVD) is a vacuum-based coating process that involves converting a solid material into a vapor phase and then depositing it onto a substrate to form a thin film. This process is widely used in industries for creating durable, high-performance coatings on various materials. The basic principles of PVD include the conversion of a solid target material into vapor, its transportation through a vacuum or low-pressure environment, and its subsequent condensation onto a substrate. The process is highly controllable, allowing for precise deposition rates and thicknesses, and is performed under high vacuum and relatively low temperatures. Common PVD methods include sputtering, e-beam evaporation, and pulsed laser deposition.
Key Points Explained:
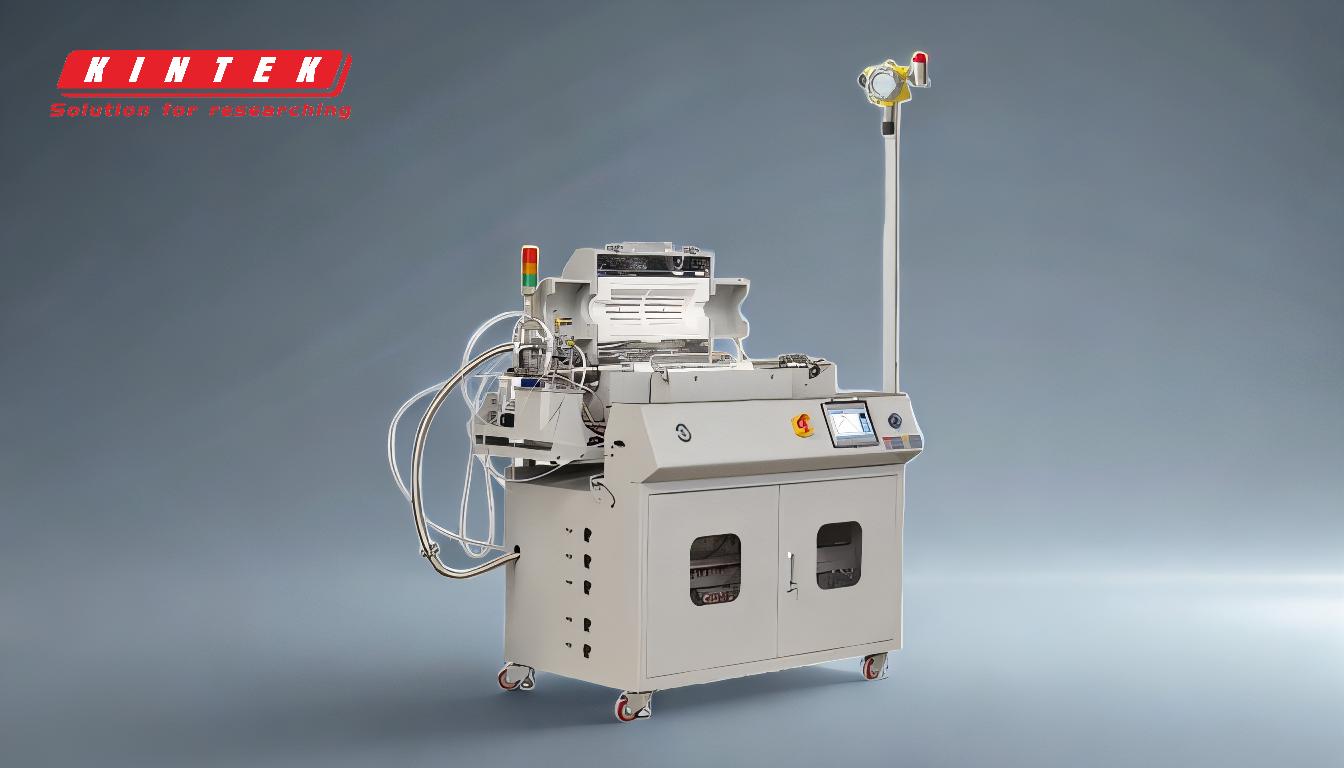
-
Conversion of Solid to Vapor Phase:
- The PVD process begins with a solid target material, which is converted into a vapor phase. This is achieved through various energy sources such as high-power electricity, laser beams, or electron beams.
- The method of vaporization depends on the specific PVD technique used. For example, in sputtering, atoms are ejected from the target material due to bombardment by high-energy particles, while in e-beam evaporation, an electron beam heats the target material until it vaporizes.
-
Transportation of Vaporized Material:
- Once the target material is vaporized, the resulting atoms or molecules are transported through a vacuum or low-pressure environment. This step is crucial to prevent contamination from background gases and to ensure that the vaporized material reaches the substrate without reacting with other substances.
- The vacuum environment also helps in controlling the direction and energy of the vaporized particles, allowing for precise deposition.
-
Deposition onto Substrate:
- The vaporized material is then directed toward the substrate, where it condenses and forms a thin film. The substrate can be made of various materials, including metals, ceramics, or polymers, depending on the application.
- The deposition process is influenced by factors such as the energy of the vaporized particles, the temperature of the substrate, and the vacuum conditions. These factors determine the adhesion, uniformity, and properties of the resulting film.
-
Control of Deposition Rate and Thickness:
- One of the key advantages of PVD is the ability to precisely control the deposition rate and the thickness of the film. This is typically achieved using a quartz crystal rate monitor, which measures the rate at which material is being deposited.
- By adjusting parameters such as the power applied to the target, the pressure in the vacuum chamber, and the distance between the target and the substrate, manufacturers can achieve the desired film properties.
-
Variants of PVD:
- PVD encompasses several different techniques, each with its own unique method of vaporizing the target material. Common variants include:
- Sputtering: Uses high-energy particles to eject atoms from the target material.
- E-beam Evaporation: Utilizes an electron beam to heat and vaporize the target material.
- Pulsed Laser Deposition (PLD): Employs a high-power laser to ablate material from the target.
- Cathodic Arc Deposition: Involves creating an arc discharge to vaporize the target material.
- Each method has its own advantages and is chosen based on the specific requirements of the application, such as the type of material being deposited, the desired film properties, and the scale of production.
- PVD encompasses several different techniques, each with its own unique method of vaporizing the target material. Common variants include:
-
Advantages of PVD:
- High Purity: The vacuum environment ensures that the deposited films are free from contaminants, resulting in high-purity coatings.
- Durability: PVD coatings are known for their hardness, wear resistance, and corrosion resistance, making them ideal for applications in harsh environments.
- Versatility: PVD can be used to deposit a wide range of materials, including metals, alloys, and ceramics, onto various substrates.
- Precision: The ability to control the deposition process with high precision allows for the creation of thin films with specific properties, such as optical, electrical, or mechanical characteristics.
-
Applications of PVD:
- PVD is used in a variety of industries, including:
- Electronics: For depositing thin films in semiconductor devices, solar cells, and displays.
- Automotive: For coating engine components, cutting tools, and decorative finishes.
- Aerospace: For creating wear-resistant coatings on turbine blades and other critical components.
- Medical: For coating surgical instruments and implants to improve biocompatibility and reduce wear.
- PVD is used in a variety of industries, including:
In summary, the basic principles of PVD involve the conversion of a solid material into a vapor phase, its transportation through a vacuum environment, and its deposition onto a substrate to form a thin film. The process is highly controllable, allowing for precise deposition rates and thicknesses, and is performed under high vacuum and relatively low temperatures. PVD is a versatile and durable coating technology with applications across various industries.
Summary Table:
Aspect | Details |
---|---|
Process Overview | Converts solid material into vapor, transports it in a vacuum, and deposits it onto a substrate. |
Key Steps | 1. Solid to vapor conversion. 2. Vapor transportation. 3. Deposition onto substrate. |
Common PVD Methods | Sputtering, E-beam Evaporation, Pulsed Laser Deposition, Cathodic Arc Deposition. |
Advantages | High purity, durability, versatility, and precision in film properties. |
Applications | Electronics, automotive, aerospace, and medical industries. |
Discover how PVD can enhance your products—contact our experts today for more information!