Isostatic pressing, particularly hot isostatic pressing (HIP), offers numerous benefits that make it a preferred method for manufacturing high-performance components. This process ensures uniform density and strength in all directions, enabling the production of complex shapes that are difficult to achieve with traditional uniaxial pressing. HIP enhances material properties by eliminating internal defects, improving mechanical performance, and enabling the creation of lightweight, durable, and high-density products. It also reduces material waste, increases productivity, and extends the service life of components. Below, the key advantages of isostatic pressing are explained in detail.
Key Points Explained:
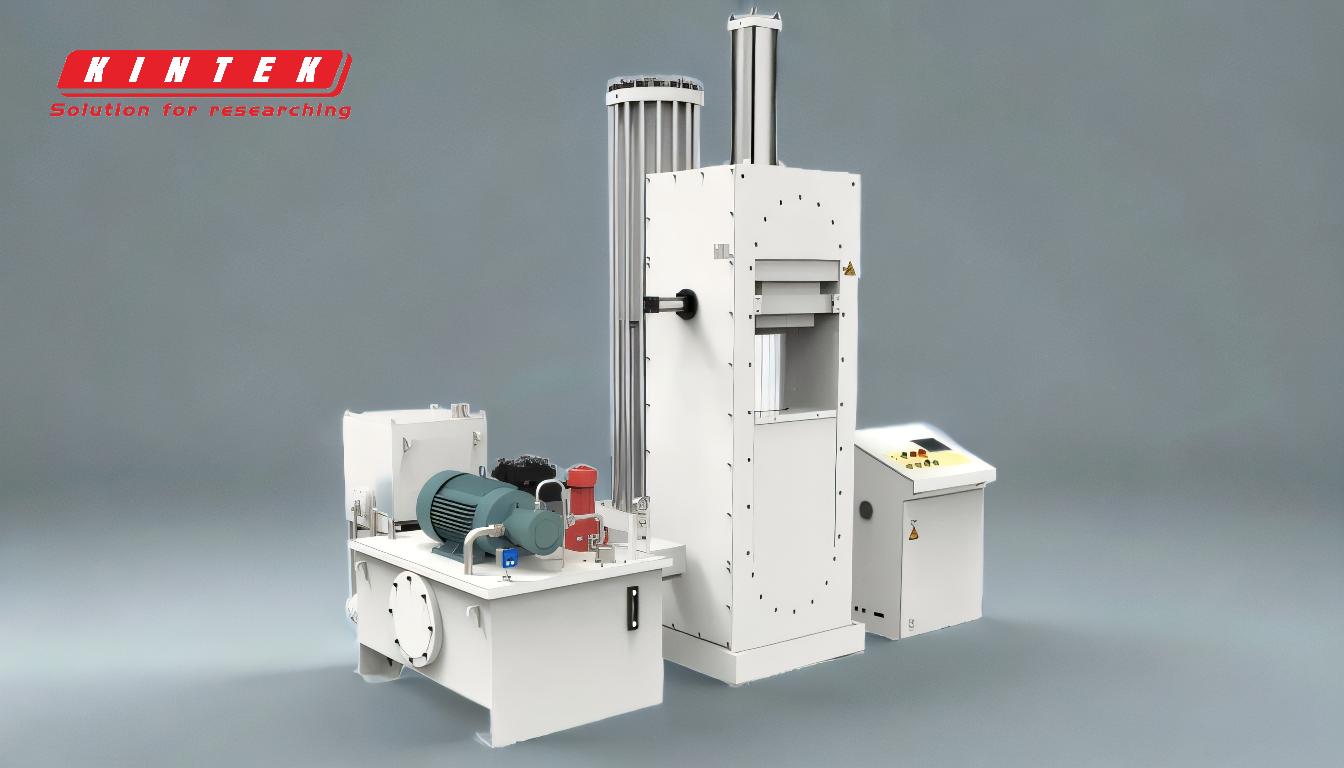
-
Uniform Density and Strength in All Directions
- Isostatic pressing applies uniform pressure from all directions, ensuring consistent density and mechanical properties throughout the component.
- This uniformity eliminates weak spots, making the material isotropic (having the same properties in all directions).
- Traditional uniaxial pressing often results in uneven density and strength due to directional pressure application.
-
Ability to Create Complex Shapes
- Isostatic pressing allows for the production of intricate and complex shapes that are difficult or impossible to achieve with uniaxial pressing.
- Elastomeric molds are used to shape the material, providing flexibility in design and enabling the engineering of components with unique geometries.
- This capability is particularly valuable for industries like aerospace, automotive, and medical devices, where complex parts are often required.
-
Improved Mechanical Properties
- HIP enhances material properties by eliminating internal microporosity and defects, resulting in a high-density, uniform microstructure.
- The process improves fatigue life, ductility, impact strength, toughness, and overall consistency of the material.
- Components produced through HIP exhibit superior mechanical performance compared to those made using conventional methods.
-
Increased Product Density
- HIP achieves near-full density in materials, reducing porosity and improving structural integrity.
- High-density materials are essential for applications requiring high strength, durability, and resistance to wear and corrosion.
- This benefit is particularly significant for advanced materials like superalloys, titanium, and stainless steel.
-
Reduction of Internal Defects
- HIP repairs internal porosity and voids, which are common defects in cast or sintered materials.
- By eliminating these defects, the process enhances the reliability and performance of components, making them suitable for critical applications in industries like energy and defense.
-
Efficient Material Utilization
- Isostatic pressing minimizes material waste, making it cost-effective for expensive and difficult-to-compact materials.
- The process ensures efficient use of raw materials, reducing scrap and losses during production.
- This efficiency is particularly beneficial for high-value materials like superalloys and titanium.
-
Lightweight Designs
- HIP enables the production of lightweight components without compromising strength or durability.
- This is crucial for industries like aerospace and automotive, where reducing weight is a priority to improve fuel efficiency and performance.
-
Formation of Metallurgical Bonds
- HIP can create strong metallurgical bonds between different materials, enabling the production of hybrid components with tailored properties.
- This capability is useful for manufacturing parts that require a combination of materials, such as those used in advanced engineering applications.
-
Extended Service Life
- Components produced through HIP exhibit longer service life due to their improved mechanical properties and reduced internal defects.
- This durability reduces maintenance costs and downtime, making HIP an economically viable option for high-performance applications.
-
Higher Productivity and Reduced Costs
- The combination of cold isostatic pressing (CIP) and HIP streamlines the manufacturing process, increasing productivity.
- Reduced scrap rates and efficient material utilization contribute to lower production costs.
- These advantages make HIP a cost-effective solution for producing high-quality components.
In summary, isostatic pressing, particularly HIP, offers a wide range of benefits, including uniform density and strength, the ability to create complex shapes, improved mechanical properties, and efficient material utilization. These advantages make it an ideal choice for industries requiring high-performance, durable, and lightweight components.
Summary Table:
Key Benefits of Isostatic Pressing | Details |
---|---|
Uniform Density & Strength | Ensures consistent properties in all directions, eliminating weak spots. |
Complex Shapes | Produces intricate designs with elastomeric molds, ideal for aerospace and medical industries. |
Improved Mechanical Properties | Eliminates defects, enhancing fatigue life, ductility, and toughness. |
Increased Product Density | Achieves near-full density, improving strength and durability. |
Reduction of Internal Defects | Repairs porosity and voids, enhancing reliability for critical applications. |
Efficient Material Utilization | Minimizes waste, ideal for high-value materials like superalloys and titanium. |
Lightweight Designs | Produces strong, lightweight components for aerospace and automotive industries. |
Metallurgical Bonds | Creates hybrid components with tailored material properties. |
Extended Service Life | Improves durability, reducing maintenance costs and downtime. |
Higher Productivity & Reduced Costs | Streamlines manufacturing with CIP and HIP, lowering production costs. |
Ready to enhance your manufacturing process with isostatic pressing? Contact our experts today to learn more!