Physical Vapor Deposition (PVD) is a highly effective technique for creating durable, high-quality, and corrosion-resistant coatings on various substrates. It is an environmentally friendly process, as it does not produce hazardous waste, making it a sustainable choice for many industries. However, PVD can be costly, has a slower rate of yield, and requires regular maintenance of cooling systems, which may limit its feasibility in some applications. Despite these challenges, PVD offers significant advantages, such as the ability to deposit materials with high precision and uniformity, making it ideal for applications requiring high-performance coatings.
Key Points Explained:
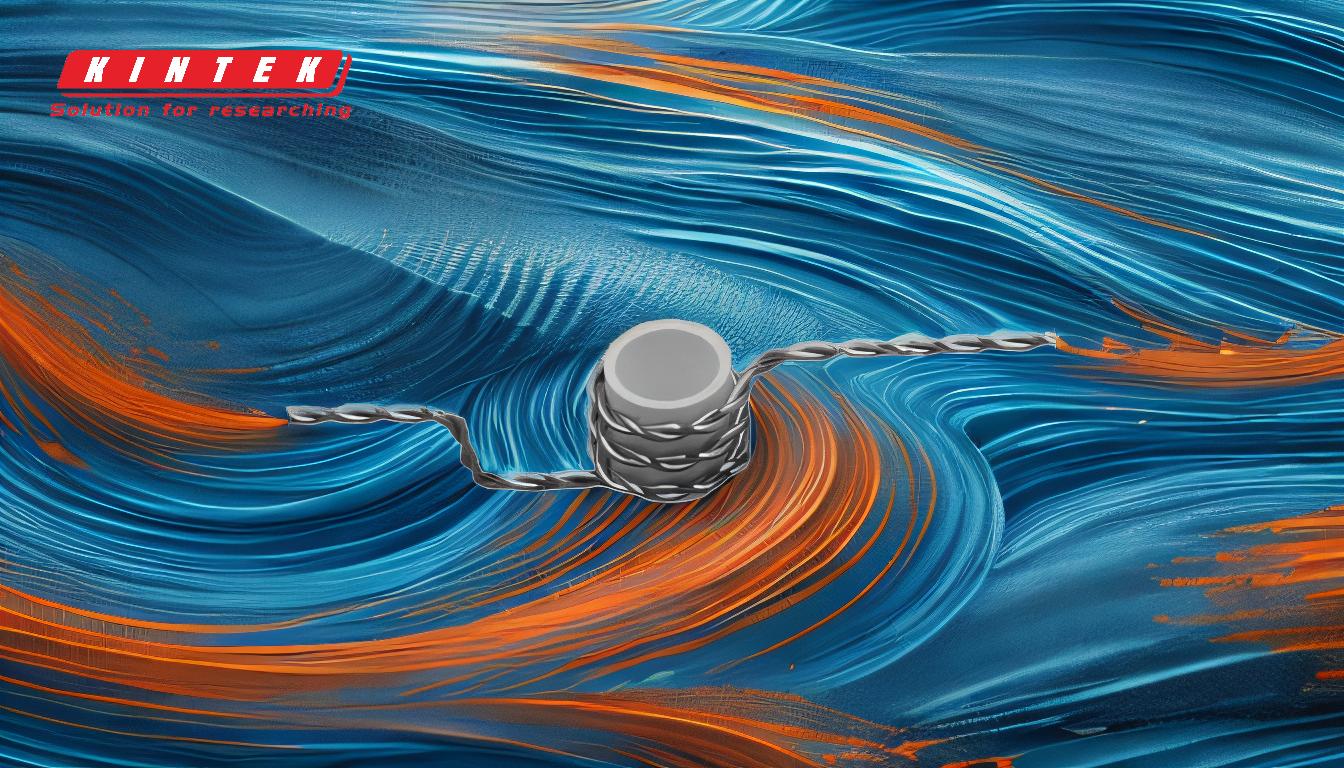
-
High-Quality and Durable Coatings:
- PVD allows for the deposition of high-quality, durable, and corrosion-resistant atoms on a substrate. This makes it suitable for applications where longevity and resistance to environmental factors are critical. For example, PVD coatings are often used in the aerospace and automotive industries to protect components from wear and corrosion.
-
Environmentally Friendly:
- One of the significant benefits of PVD is its environmental friendliness. Unlike some other deposition methods, PVD does not produce hazardous waste, making it a more sustainable option. This is particularly important in industries where environmental regulations are stringent.
-
Precision and Uniformity:
- PVD offers high precision and uniformity in coating deposition. This is crucial for applications that require consistent thickness and coverage, such as in the manufacturing of electronic components. The ability to achieve uniform coatings even on complex shapes is a notable advantage of PVD.
-
Resistance to High Temperatures:
- Films deposited by PVD can tolerate exposure to high temperatures, making them suitable for use in high-stress environments. This is particularly beneficial in industries like aerospace and automotive, where components are often subjected to extreme conditions.
-
Versatility in Material Deposition:
- PVD can be used to deposit a wide range of materials, including metals, ceramics, and glass. This versatility allows for the creation of coatings with specific properties, such as enhanced corrosion resistance or abrasion resistance, tailored to the needs of the application.
-
Challenges and Limitations:
- Despite its many advantages, PVD does have some limitations. The process can be expensive, and the rate of yield is relatively slow compared to other methods. Additionally, PVD requires routine maintenance of a reliable cooling system, which can add to the overall cost and complexity of the process. These factors may limit the feasibility of PVD in some applications, particularly those requiring high throughput or low-cost solutions.
-
Comparison with Chemical Vapor Deposition (CVD):
- While PVD offers several advantages, it is important to compare it with other deposition methods like Chemical Vapor Deposition (CVD). CVD has its own set of advantages, such as better selectivity in depositing material, greater conformality, and the ability to process substrates in larger batches. However, CVD typically requires higher temperatures and more complex chemical reactions, which can be a drawback in some applications.
In summary, PVD is a versatile and environmentally friendly method for depositing high-quality, durable coatings on various substrates. While it has some limitations, its advantages make it a valuable technique in many industries, particularly those requiring high-performance coatings with precise and uniform properties.
Summary Table:
Advantages of PVD | Details |
---|---|
High-Quality & Durable Coatings | Resistant to wear, corrosion, and environmental factors. |
Environmentally Friendly | No hazardous waste, making it a sustainable choice. |
Precision & Uniformity | Ensures consistent thickness and coverage, even on complex shapes. |
High-Temperature Resistance | Suitable for extreme conditions in aerospace and automotive industries. |
Versatile Material Deposition | Deposits metals, ceramics, and glass for tailored properties. |
Limitations | Details |
High Cost | Expensive process and equipment. |
Slower Yield Rate | Lower throughput compared to other methods. |
Cooling System Maintenance | Requires regular upkeep, adding to operational complexity. |
Learn how PVD can elevate your coating applications—contact our experts today!