PVD (Physical Vapor Deposition) coating is a versatile and advanced surface finishing technique that offers numerous benefits across various industries. It enhances the durability, corrosion resistance, and aesthetic appeal of products, making it a preferred choice for applications ranging from decorative finishes to high-performance industrial components. The process is environmentally friendly, cost-effective, and capable of producing high-quality, long-lasting coatings. Below, we explore the key benefits and applications of PVD coating in detail.
Key Points Explained:
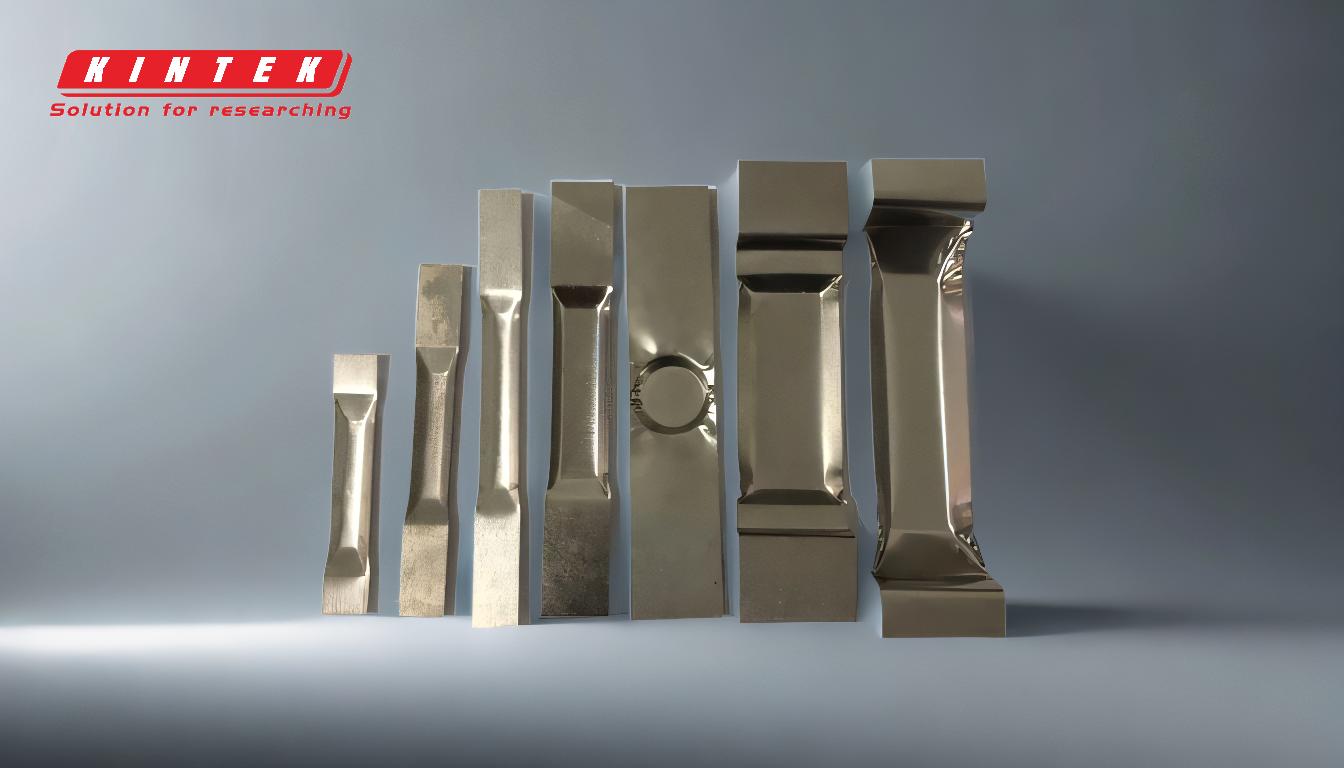
-
High Hardness and Durability
- PVD coatings significantly increase the hardness of surfaces, making them more resistant to wear, scratches, and abrasion.
- This property is particularly beneficial for tools, automotive components, and industrial machinery, where durability is critical.
- The enhanced hardness also extends the lifespan of products, reducing the need for frequent replacements.
-
Corrosion Resistance
- PVD coatings provide excellent protection against corrosion, even in harsh environments.
- This makes them ideal for marine hardware, medical equipment, and outdoor applications where exposure to moisture and chemicals is common.
- The corrosion-resistant properties ensure that products maintain their functionality and appearance over time.
-
High-Temperature Resistance
- PVD coatings can withstand high temperatures, making them suitable for applications involving high-temperature cutting, evaporation, and other extreme conditions.
- This property is particularly valuable in industries like aerospace and automotive, where components are often exposed to high heat.
-
Environmentally Friendly
- Compared to traditional coating methods like chrome plating, PVD coating is more environmentally friendly.
- It does not produce toxic byproducts or hazardous waste, making it a sustainable choice for manufacturers.
- The process also reduces the need for harmful chemicals, contributing to a greener production cycle.
-
Decorative Applications
- PVD coating is widely used for decorative purposes, offering a wide range of colors and finishes.
- By adjusting factors like coating material, time, and workpiece, manufacturers can achieve various aesthetic effects, such as gold, rose gold, black, or matte finishes.
- This versatility makes PVD coating popular in industries like jewelry, eyewear, and home fixtures.
-
Extended Product Lifespan
- PVD coatings can enhance the lifespan of products by up to ten times, making them last more than 25 years in some cases.
- This is particularly beneficial for high-wear components like car parts, surgical tools, and industrial machinery.
- The extended lifespan reduces maintenance costs and improves overall efficiency.
-
Versatility Across Industries
- PVD coating is used in a wide range of industries, including automotive, medical, marine, firearms, and consumer goods.
- Common applications include kitchen and bath fixtures, writing instruments, door hardware, musical instruments, and sporting goods.
- The ability to customize coatings for specific applications makes PVD a highly versatile solution.
-
Improved Electrical Conductivity
- PVD coatings can enhance electrical conductivity by depositing conductive materials like metals.
- This property is useful for electronic devices, where conductive films are required for efficient performance.
- It also supports the development of advanced technologies like solar panels and electronic displays.
-
Cost-Effective Production
- PVD coating machines are computer-controlled, allowing for efficient and precise production.
- The process reduces production costs and turnaround time, making it suitable for both high-volume manufacturing and small batch production.
- The ability to multitask and automate the process further enhances its cost-effectiveness.
-
Enhanced Optical Properties
- PVD coatings offer excellent optical properties, making them ideal for lenses, mirrors, and other optical components.
- They improve reflectivity and transmission, which is crucial for applications in electronics, solar panels, and precision instruments.
- The ability to achieve high-quality optical finishes adds value to products in the optics industry.
In conclusion, PVD coating is a highly beneficial surface finishing technique that offers a combination of durability, aesthetic appeal, and environmental sustainability. Its wide range of applications and cost-effective production make it a valuable solution for industries seeking to enhance the performance and longevity of their products.
Summary Table:
Benefit | Key Details |
---|---|
High Hardness & Durability | Resists wear, scratches, and abrasion; extends product lifespan. |
Corrosion Resistance | Protects against moisture and chemicals; ideal for harsh environments. |
High-Temperature Resistance | Withstands extreme heat; suitable for aerospace and automotive applications. |
Environmentally Friendly | No toxic byproducts; reduces harmful chemicals; sustainable production. |
Decorative Applications | Offers customizable colors and finishes like gold, black, and matte. |
Extended Product Lifespan | Enhances lifespan by up to 10x; reduces maintenance costs. |
Versatility Across Industries | Used in automotive, medical, marine, and consumer goods industries. |
Improved Electrical Conductivity | Enhances conductivity for electronics and advanced technologies. |
Cost-Effective Production | Computer-controlled process; reduces costs and turnaround time. |
Enhanced Optical Properties | Improves reflectivity and transmission for lenses, mirrors, and solar panels. |
Unlock the full potential of PVD coating for your products—contact us today to learn more!