Sintering is a manufacturing process that offers numerous benefits, making it a preferred method for producing high-performance materials and components. It involves heating powdered materials below their melting point to bond particles, resulting in improved material properties and structural integrity. The advantages of sintering include enhanced strength, durability, and conductivity, as well as the ability to create complex shapes and work with high-melting-point materials. Additionally, sintering ensures high purity, uniformity, and repeatability in production, while also allowing for controlled porosity and cost-effective manufacturing. These benefits make sintering a versatile and efficient process for a wide range of applications, from industrial components to specialized products like filters and jewelry.
Key Points Explained:
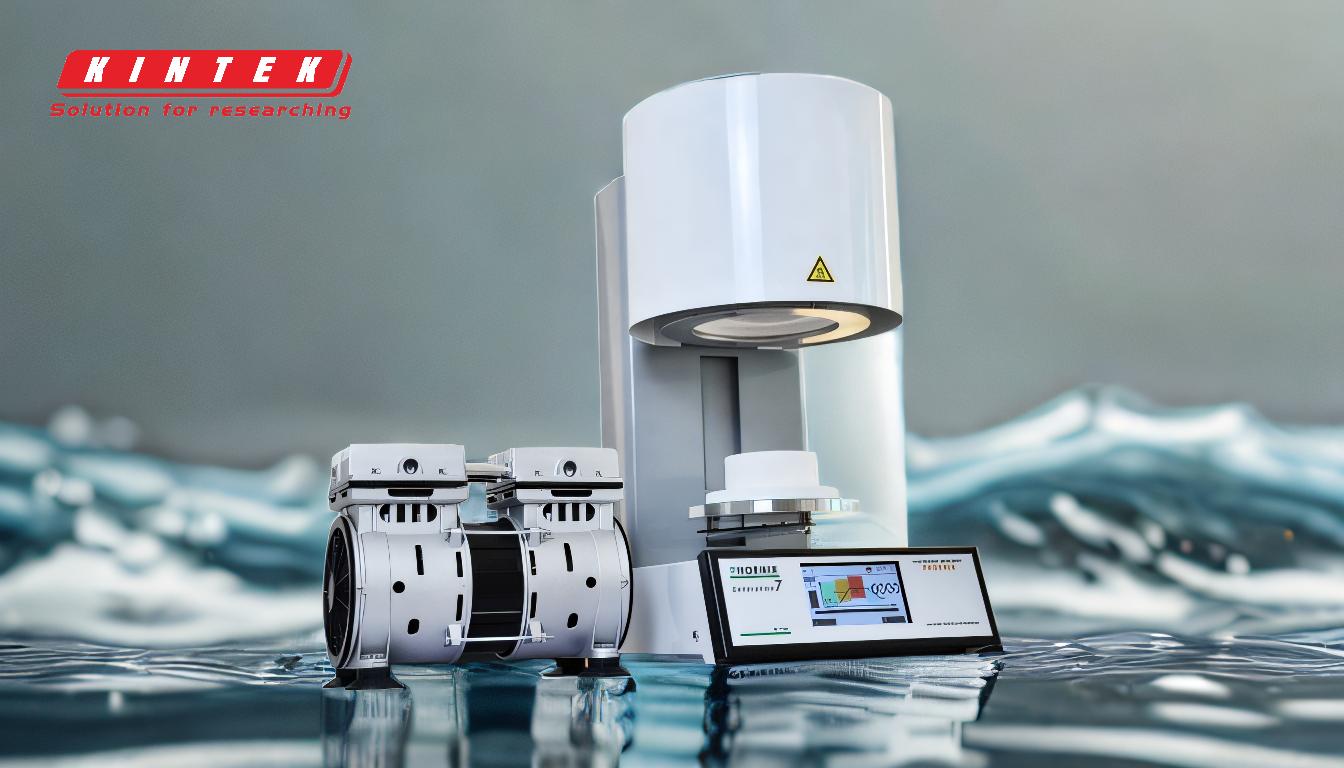
-
Enhanced Material Properties:
- Strength and Durability: Sintering develops sintered necks between particles, reducing pores and increasing the overall strength of the material. This makes the final product more durable and capable of withstanding mechanical stress.
- Thermal and Electrical Conductivity: The process improves thermal and electrical conductivity by creating a more uniform and dense material structure, which is essential for applications like heat pipes and electrical components.
- Transparency and Translucency: In certain materials, sintering can enhance optical properties, making them more transparent or translucent, which is useful in applications like ceramics and specialized glass.
-
Controlled Porosity:
- Sintering allows for the creation of materials with uniform and controlled porosity. This is particularly useful in applications like filters and catalysts, where gas absorbency is required without compromising strength.
- The ability to tailor porosity also enables the production of lightweight yet strong materials, which are ideal for aerospace and automotive industries.
-
High Purity and Uniformity:
- Sintering ensures high levels of purity in the starting materials, as it eliminates impurities and contaminants during the heating process.
- The process also provides uniformity in grain size and material composition, leading to consistent and repeatable results in production.
-
Complex Shapes and Net-Shaped Objects:
- One of the standout benefits of sintering is its ability to produce components with complex shapes and intricate designs. This is particularly advantageous in industries like jewelry and precision engineering.
- The process creates nearly net-shaped objects, reducing the need for additional machining and minimizing material waste.
-
Cost-Effectiveness:
- Sintering is a cost-effective manufacturing method because it reduces the need for secondary processing steps like machining. The ability to produce near-net shapes directly from the sintering process saves both time and resources.
- The process also allows for the use of less expensive raw materials, such as powdered metals, without compromising the quality of the final product.
-
Versatility in Material Selection:
- Sintering can be used with a wide range of materials, including those with very high melting points, such as tungsten and molybdenum. This makes it possible to manufacture components that would be difficult or impossible to produce using traditional melting and casting methods.
- The process also supports the diffusion of alloying elements like nickel, copper, and graphite, enabling the creation of tailored material compositions with specific properties.
-
Improved Mechanical Handling Strength:
- Sintered materials exhibit improved mechanical handling strength, making them easier to work with during subsequent manufacturing processes. This is particularly important for components that require precise assembly or further processing.
-
Environmental and Operational Benefits:
- Sintering eliminates the need for lubricants in the compacted powder, reducing the environmental impact and simplifying the production process.
- The reduction of surface oxygen during sintering also improves the material's resistance to oxidation and corrosion, extending the lifespan of the final product.
In summary, sintering is a highly advantageous process that enhances material properties, enables the production of complex shapes, and offers cost-effective and versatile manufacturing solutions. Its ability to control porosity, ensure high purity, and work with difficult materials makes it indispensable in various industries, from aerospace to consumer goods.
Summary Table:
Key Benefits of Sintering | Description |
---|---|
Enhanced Material Properties | Improves strength, durability, conductivity, and optical properties. |
Controlled Porosity | Enables uniform porosity for filters, catalysts, and lightweight materials. |
High Purity and Uniformity | Ensures consistent grain size and eliminates impurities. |
Complex Shapes and Net-Shapes | Produces intricate designs with minimal machining and waste. |
Cost-Effectiveness | Reduces secondary processing and material costs. |
Versatility in Material Use | Works with high-melting-point materials like tungsten and molybdenum. |
Improved Mechanical Strength | Enhances handling strength for precise assembly and processing. |
Environmental Benefits | Eliminates lubricants and reduces oxidation, improving corrosion resistance. |
Ready to leverage the benefits of sintering for your materials? Contact us today to learn more!