Vacuum annealing, performed in a vacuum annealing furnace, offers numerous benefits, particularly in industries requiring high precision and quality in material processing. This process involves heating materials in a vacuum environment, which eliminates exposure to reactive gases and impurities, ensuring ultra-clean and high-quality components. The controlled environment enhances mechanical properties such as hardness, strength, and wear resistance while maintaining dimensional stability. Additionally, vacuum annealing provides precise temperature control, energy efficiency, and versatility for various heat treatment processes. These advantages make it a preferred method for industries like aerospace, automotive, and electronics, where material integrity and performance are critical.
Key Points Explained:
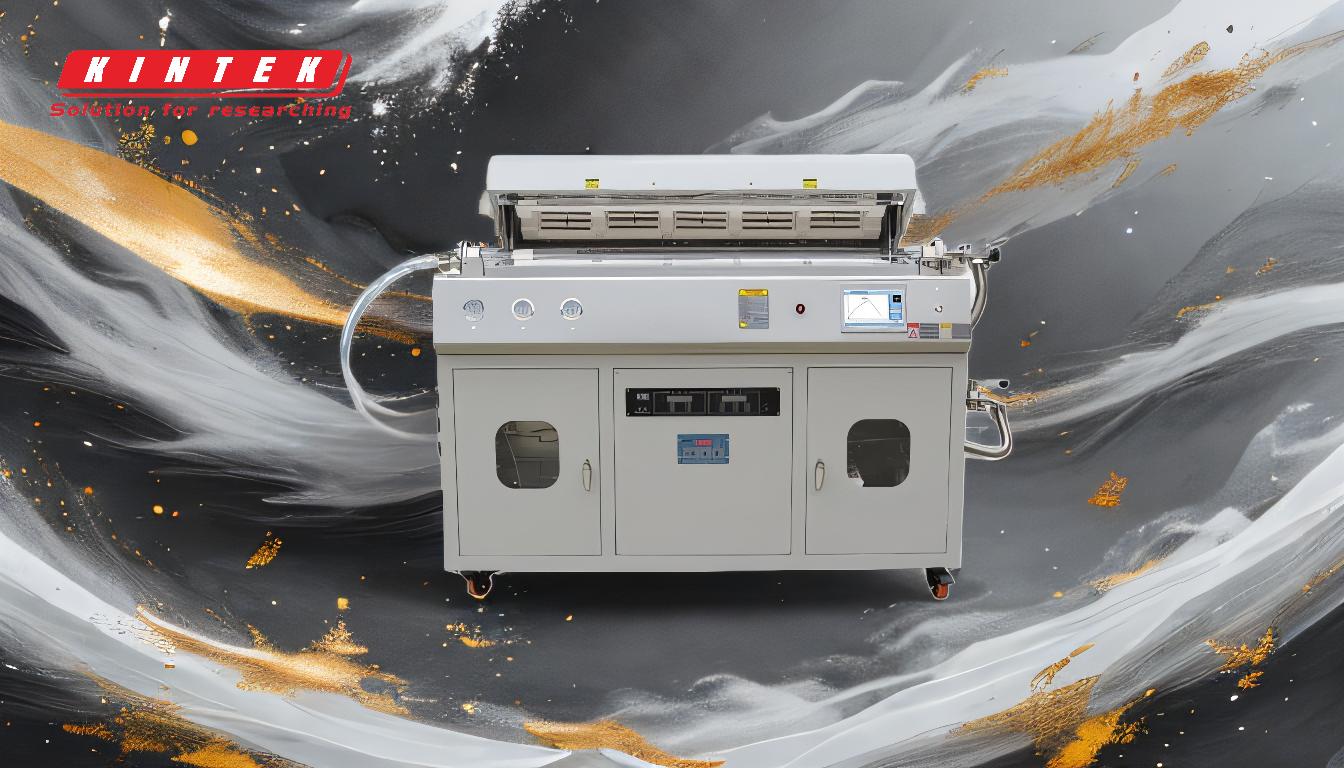
-
Clean and Controlled Environment:
- Vacuum annealing eliminates exposure to reactive gases like oxygen, moisture, and carbon dioxide, which can cause surface oxidation, decarburization, or contamination. This ensures the production of ultra-clean components with no impurities, making it ideal for applications requiring high purity, such as semiconductors and medical devices.
-
Improved Mechanical Properties:
- The process enhances material properties such as hardness, strength, and wear resistance while preserving dimensional stability. This is particularly beneficial for metals and alloys, as it prevents surface defects like softening or hardening, ensuring consistent performance.
-
Precise Temperature Control:
- Vacuum furnaces offer excellent temperature uniformity and stability, enabling consistent and repeatable results. This precision is crucial for industries with stringent quality standards, as it ensures that components meet specified performance criteria in every treatment cycle.
-
Versatility in Heat Treatment:
- Vacuum annealing supports a wide range of heat treatment processes, including brazing, sintering, tempering, and hardening. This versatility makes it suitable for various materials and applications, from aerospace alloys to tool steels.
-
Energy Efficiency:
- Advanced insulation materials and control systems in vacuum furnaces minimize heat loss and optimize energy consumption. This reduces operational costs and environmental impact, aligning with sustainability goals.
-
Reduced Oxidation and Decarburization:
- The vacuum environment prevents oxidation and decarburization of the workpiece surface, resulting in less deformation and better mechanical properties. This is especially important for high-temperature applications where surface integrity is critical.
-
Consistency and Repeatability:
- The controlled environment and precise parameters of vacuum annealing ensure repeatable results, which are essential for industries requiring strict quality assurance. This predictability guarantees that components meet performance standards in every treatment cycle.
-
Enhanced Material Purity:
- Vacuum annealing removes impurities and gases from materials, producing finished products with fewer defects such as pinholes and segregation. This is particularly advantageous for melting and processing special alloys, including nickel-based superalloys and corrosion-resistant materials.
-
Rapid Cooling (Quenching):
- Vacuum furnaces are equipped with rapid-cooling devices that use inert gases like nitrogen or argon to achieve fast and controlled cooling rates. This enhances the material's microstructure and mechanical properties, making it suitable for high-performance applications.
-
No Pollution:
- The process is environmentally friendly, as it produces no harmful emissions or waste. This aligns with modern industrial trends toward sustainable and eco-friendly manufacturing practices.
In summary, vacuum annealing in a vacuum annealing furnace provides a clean, precise, and efficient method for enhancing material properties and ensuring high-quality results. Its versatility, energy efficiency, and ability to produce consistent, repeatable outcomes make it an indispensable tool in advanced manufacturing and material processing industries.
Summary Table:
Benefit | Description |
---|---|
Clean and Controlled Environment | Eliminates reactive gases, ensuring ultra-clean, high-purity components. |
Improved Mechanical Properties | Enhances hardness, strength, and wear resistance while maintaining stability. |
Precise Temperature Control | Ensures uniform heating and repeatable results for stringent quality standards. |
Versatility in Heat Treatment | Supports brazing, sintering, tempering, and hardening for various materials. |
Energy Efficiency | Minimizes heat loss and reduces operational costs with advanced insulation. |
Reduced Oxidation and Decarburization | Prevents surface defects, ensuring better mechanical properties. |
Consistency and Repeatability | Guarantees predictable, high-quality outcomes for every treatment cycle. |
Enhanced Material Purity | Removes impurities, producing defect-free components for critical applications. |
Rapid Cooling (Quenching) | Achieves fast, controlled cooling rates for improved microstructure. |
No Pollution | Eco-friendly process with no harmful emissions or waste. |
Unlock the full potential of vacuum annealing for your materials—contact our experts today to learn more!