Graphene, a single layer of carbon atoms arranged in a hexagonal lattice, is produced through various methods, each with unique advantages and limitations. The primary methods include mechanical exfoliation, liquid-phase exfoliation, reduction of graphene oxide (GO), and chemical vapor deposition (CVD). Among these, CVD is the most promising for producing large-area, high-quality graphene, making it the best source for industrial applications. Mechanical exfoliation is ideal for research purposes, while liquid-phase exfoliation is suitable for mass production but often results in lower electrical quality. Reduction of GO is another method, but it typically yields graphene with defects. The choice of method depends on the intended application, with CVD standing out as the best source for high-quality, scalable graphene production.
Key Points Explained:
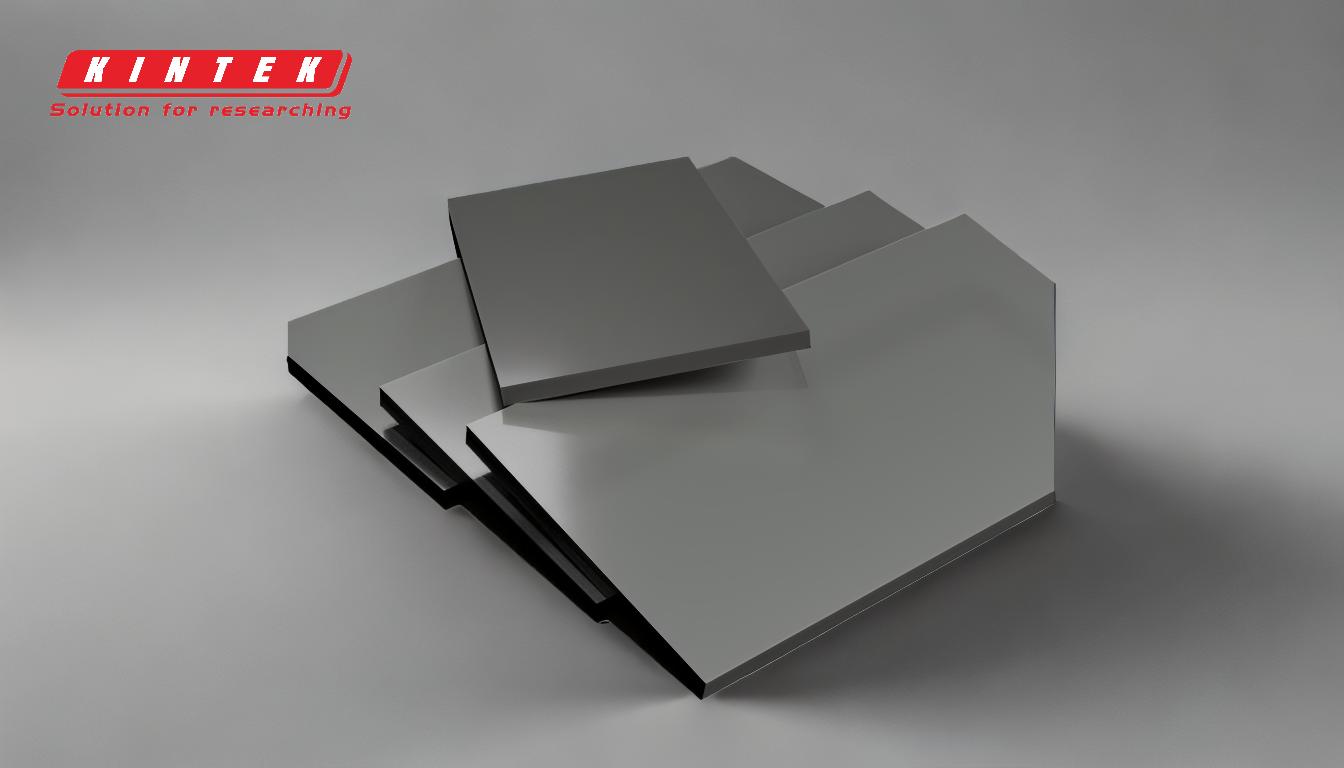
-
Mechanical Exfoliation:
- Process: This method involves peeling layers of graphene from graphite using adhesive tape or similar techniques.
- Advantages: Produces high-quality graphene with minimal defects, making it ideal for fundamental research and studies.
- Disadvantages: Not scalable for industrial applications; yields small quantities of graphene.
- Best Use Case: Research laboratories and fundamental studies where high-quality graphene is required in small amounts.
-
Liquid-Phase Exfoliation:
- Process: Graphite is dispersed in a liquid medium and subjected to ultrasonic waves to separate the layers into graphene.
- Advantages: Suitable for mass production; relatively simple and cost-effective.
- Disadvantages: Graphene produced often has lower electrical quality due to defects and impurities.
- Best Use Case: Applications where large quantities of graphene are needed, but high electrical quality is not critical, such as in composites or coatings.
-
Reduction of Graphene Oxide (GO):
- Process: Graphene oxide is chemically reduced to produce graphene, often using reducing agents like hydrazine or thermal reduction.
- Advantages: Can produce graphene in large quantities; relatively low cost.
- Disadvantages: The resulting graphene often contains defects and residual oxygen groups, which can affect its electrical properties.
- Best Use Case: Applications where cost is a significant factor, and high electrical quality is not essential, such as in sensors or energy storage devices.
-
Chemical Vapor Deposition (CVD):
- Process: Graphene is grown on a substrate, typically a transition metal like nickel or copper, by decomposing carbon-containing gases at high temperatures.
- Advantages: Produces large-area, high-quality graphene with excellent electrical properties; scalable for industrial applications.
- Disadvantages: Requires high temperatures and specialized equipment; can be expensive.
- Best Use Case: Industrial applications requiring high-quality, large-area graphene, such as in electronics, transparent conductive films, and advanced materials.
-
Sublimation of Silicon Carbide (SiC):
- Process: Silicon is sublimated from a silicon carbide crystal at high temperatures, leaving behind a layer of graphene.
- Advantages: Produces high-quality graphene with good electrical properties.
- Disadvantages: High cost; limited scalability.
- Best Use Case: Specialized applications where high-quality graphene is required, but cost and scalability are less of a concern.
-
Comparison of Methods:
- Quality: CVD and mechanical exfoliation produce the highest quality graphene, with minimal defects and excellent electrical properties.
- Scalability: CVD and liquid-phase exfoliation are the most scalable methods, suitable for industrial production.
- Cost: Liquid-phase exfoliation and reduction of GO are generally more cost-effective, while CVD and SiC sublimation are more expensive.
- Applications: The choice of method depends on the specific application, with CVD being the best source for high-quality, large-area graphene needed in advanced technologies.
In conclusion, the best source of graphene depends on the intended application. For high-quality, large-area graphene, CVD is the most promising method, making it the best source for industrial applications. Mechanical exfoliation is ideal for research, while liquid-phase exfoliation and reduction of GO are suitable for cost-sensitive applications where high electrical quality is not critical.
Summary Table:
Method | Advantages | Disadvantages | Best Use Case |
---|---|---|---|
Mechanical Exfoliation | High-quality, minimal defects | Not scalable, small quantities | Research labs, fundamental studies |
Liquid-Phase Exfoliation | Mass production, cost-effective | Lower electrical quality | Composites, coatings |
Reduction of GO | Large quantities, low cost | Defects, residual oxygen groups | Sensors, energy storage |
CVD | Large-area, high-quality, scalable | Expensive, specialized equipment | Electronics, advanced materials |
SiC Sublimation | High-quality, good electrical properties | High cost, limited scalability | Specialized applications |
Need high-quality graphene for your application? Contact our experts today to find the best solution!