Thin film technology, while highly promising for applications in electronics, optics, and coatings, faces several significant challenges. These challenges stem from the intricate processes involved in deposition, cooling, and scaling. Key issues include temperature limitations during deposition, undesirable stresses generated during cooling, and the need to optimize deposition rates while improving mechanical and tribological properties. Additionally, achieving uniformity, ensuring proper adhesion, minimizing contamination, and balancing cost and scalability are critical hurdles. Addressing these challenges requires a multidisciplinary approach, combining materials science, engineering, and process optimization to ensure the successful application of thin film technology in various industries.
Key Points Explained:
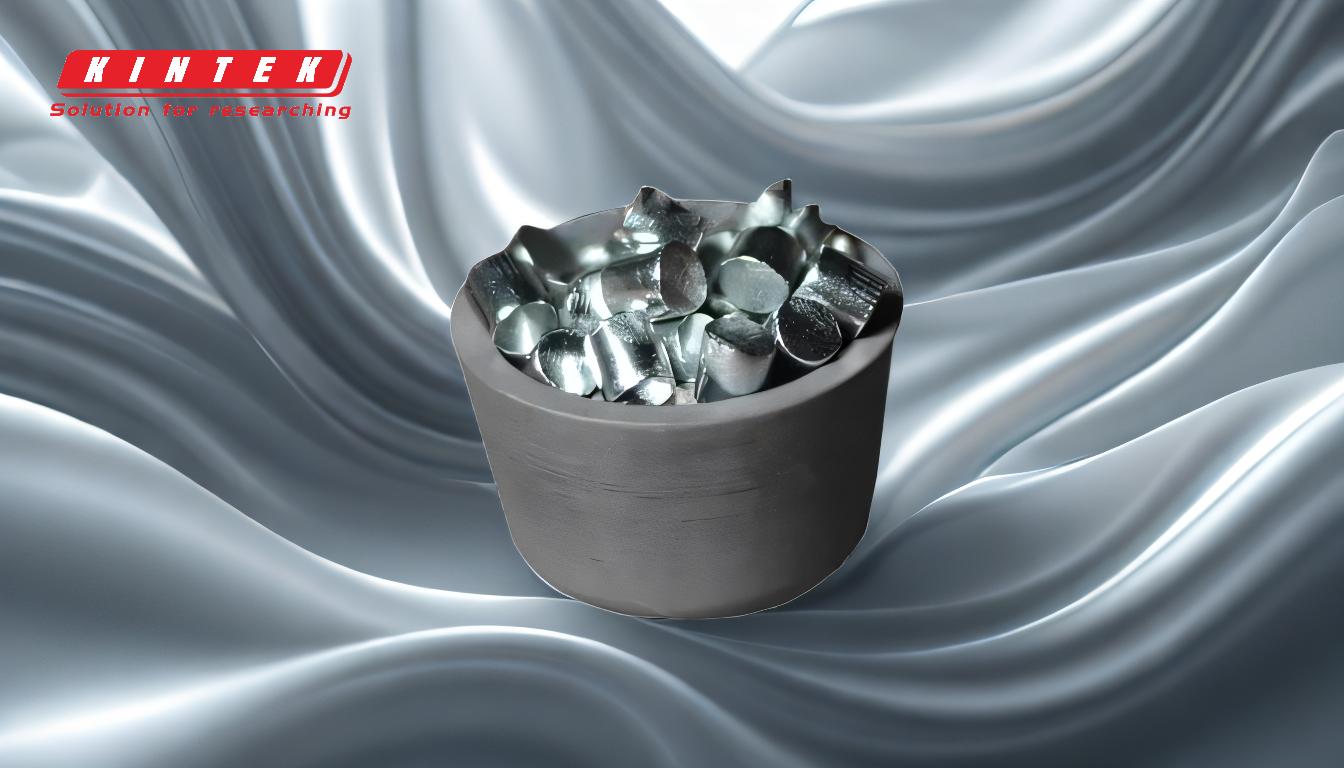
-
Temperature Limitations During Deposition:
- Thin film deposition processes, such as chemical vapor deposition (CVD) and physical vapor deposition (PVD), often require high temperatures to achieve the desired film properties.
- High temperatures can lead to substrate damage, especially for temperature-sensitive materials like polymers or certain semiconductors.
- Managing temperature gradients is crucial to prevent thermal stress and ensure uniform film growth.
-
Undesirable Stresses Generated During Cooling:
- After deposition, cooling can induce thermal stresses due to differences in thermal expansion coefficients between the film and the substrate.
- These stresses can lead to film cracking, delamination, or other mechanical failures.
- Techniques such as stress-relief annealing or using intermediate layers with matched thermal properties are often employed to mitigate these issues.
-
Optimizing Deposition Rates and Improving Mechanical and Tribological Properties:
- Achieving high deposition rates is essential for industrial scalability but often compromises film quality, such as uniformity and mechanical properties.
- Balancing deposition rate with the need for high-quality films requires precise control over process parameters like pressure, temperature, and gas flow rates.
- Enhancing mechanical properties (e.g., hardness, wear resistance) and tribological performance (e.g., friction, lubrication) is critical for applications in coatings and protective layers.
-
Ensuring Uniformity and Thickness Control:
- Uniformity in film thickness is vital for consistent performance, especially in optical and electronic applications.
- Variations in thickness can lead to defects, such as pinholes or uneven electrical conductivity.
- Advanced deposition techniques, such as atomic layer deposition (ALD), offer better control but may be slower and more expensive.
-
Achieving Proper Adhesion and Preventing Delamination:
- Strong adhesion between the film and substrate is essential to prevent delamination, which can compromise the functionality and durability of the film.
- Surface preparation, such as cleaning and roughening, and the use of adhesion-promoting layers are common strategies to enhance bonding.
- Delamination can also occur due to mechanical stresses, thermal cycling, or environmental factors like humidity.
-
Minimizing Contamination:
- Contaminants, such as dust, gases, or impurities, can degrade film quality and performance.
- Maintaining a clean deposition environment, using high-purity materials, and implementing rigorous cleaning protocols are necessary to minimize contamination.
- Contamination can lead to defects, reduced electrical conductivity, or compromised optical properties.
-
Ensuring Substrate Compatibility:
- The choice of substrate material is critical, as it must be compatible with the deposition process and the intended application.
- Mismatches in thermal expansion coefficients, chemical reactivity, or mechanical properties can lead to film failure.
- Surface treatments or intermediate layers may be required to improve compatibility.
-
Maintaining Film Purity and Composition:
- High purity and precise control over film composition are essential for applications in semiconductors, optics, and coatings.
- Impurities or deviations in composition can alter electrical, optical, or mechanical properties.
- Techniques like sputtering or molecular beam epitaxy (MBE) are used to achieve high-purity films with precise composition control.
-
Balancing Cost and Scalability:
- Thin film deposition processes must be cost-effective and scalable for industrial applications.
- High-cost techniques, such as ALD or MBE, may not be feasible for large-scale production.
- Developing cost-effective deposition methods, optimizing process parameters, and reducing material waste are key to achieving scalability.
-
Achieving Standardization:
- Standardization of deposition processes, materials, and characterization methods is essential for consistent quality and performance.
- Lack of standardization can lead to variability in film properties and hinder the adoption of thin film technology in industry.
- Collaborative efforts between researchers, manufacturers, and standardization bodies are needed to establish best practices and guidelines.
By addressing these challenges through innovative materials, advanced deposition techniques, and rigorous process control, the potential of thin film technology can be fully realized across a wide range of applications.
Summary Table:
Challenge | Key Issues | Solutions |
---|---|---|
Temperature Limitations | High temperatures can damage substrates; thermal stress affects uniformity. | Manage temperature gradients; use compatible materials. |
Undesirable Stresses During Cooling | Thermal stresses cause cracking or delamination. | Stress-relief annealing; use intermediate layers. |
Deposition Rate Optimization | High rates may compromise film quality. | Balance process parameters (pressure, temperature, gas flow). |
Uniformity and Thickness Control | Variations lead to defects like pinholes. | Use advanced techniques like ALD for better control. |
Adhesion and Delamination | Poor adhesion compromises durability. | Surface preparation; adhesion-promoting layers. |
Contamination | Impurities degrade film quality. | Maintain clean environments; use high-purity materials. |
Substrate Compatibility | Mismatched properties cause film failure. | Surface treatments; intermediate layers. |
Film Purity and Composition | Impurities alter electrical or optical properties. | Use sputtering or MBE for high-purity films. |
Cost and Scalability | High-cost techniques hinder large-scale production. | Optimize processes; reduce material waste. |
Standardization | Lack of standardization leads to variability. | Collaborate with researchers and manufacturers for best practices. |
Ready to tackle thin film challenges? Contact our experts today for tailored solutions!