Induction furnaces, particularly the IGBT induction furnace, are widely used in metallurgical and manufacturing industries due to their efficiency and precision. However, they come with several disadvantages that can impact their suitability for certain applications. These include limitations in refining capacity, higher operating costs, lower power efficiency in some designs, and challenges related to maintenance and alloy changes. Below, we explore these cons in detail to provide a comprehensive understanding of the drawbacks associated with induction furnaces.
Key Points Explained:
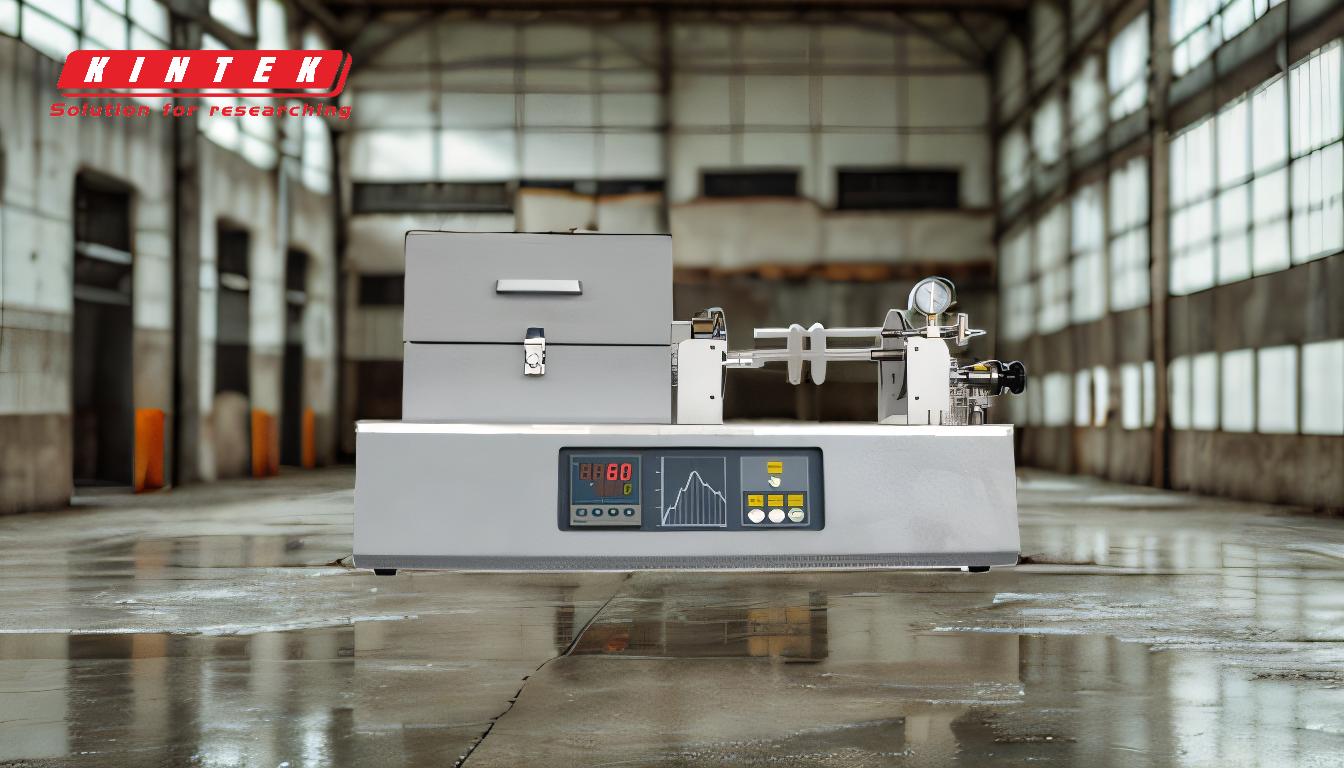
-
Lack of Refining Capacity
- Induction furnaces, including the IGBT induction furnace, are not designed for refining processes.
- Charge materials must be free of oxides and have a known composition to avoid issues during melting.
- Alloying elements can be lost due to oxidation, requiring re-addition, which increases material costs and operational complexity.
-
Lower Power Efficiency in Coreless-Type Induction Furnaces
- Coreless-type induction furnaces, which operate across a wide frequency range (50 Hz to 10 kHz), have a power efficiency of approximately 75%.
- This is significantly lower than core-type induction furnaces, which can achieve up to 98% power efficiency.
- Frequent alloy changes in coreless-type furnaces can also reduce the lifespan of the refractory lining, adding to maintenance costs.
-
High Operating Costs
- Induction furnaces rely on electricity, which can be more expensive than gas or oil, leading to higher operating costs.
- The cost of electricity can vary significantly depending on location, making it a less economical option in regions with high energy prices.
-
Maintenance and Operational Challenges
- Core-type induction furnaces require continuous maintenance of the metal loop and are rarely allowed to cool, which can increase operational complexity.
- While electric furnaces are generally sturdy, any issues that arise may require professional repairs, which can be costly and time-consuming.
-
Limitations in Alloy Changes
- Core-type induction furnaces are less flexible when it comes to alloy changes, as they are optimized for high-throughput operations with few alloy changes.
- Coreless-type furnaces, while more flexible, still face challenges with refractory lining wear due to frequent alloy changes.
-
Temperature Control and Material Loss
- Although induction furnaces offer precise temperature control, the lack of refining capacity can lead to material loss, particularly for oxidation-prone elements.
- This can result in additional costs for re-adding lost elements and ensuring the final product meets quality standards.
In summary, while induction furnaces, including the IGBT induction furnace, offer numerous advantages such as fast heating, high efficiency, and precise temperature control, they also come with significant drawbacks. These include limitations in refining capacity, higher operating costs, lower power efficiency in certain designs, and challenges related to maintenance and alloy changes. Understanding these cons is crucial for making informed decisions when selecting a furnace for specific industrial applications.
Summary Table:
Disadvantage | Details |
---|---|
Lack of Refining Capacity | Not designed for refining; requires pre-cleaned materials. |
Lower Power Efficiency | Coreless-type furnaces have ~75% efficiency vs. 98% in core-type designs. |
High Operating Costs | Electricity reliance leads to higher costs, especially in high-energy areas. |
Maintenance Challenges | Requires continuous upkeep; repairs can be costly and time-consuming. |
Limitations in Alloy Changes | Core-type furnaces are less flexible; refractory wear in coreless designs. |
Material Loss | Oxidation-prone elements may be lost, increasing material costs. |
Need help choosing the right furnace for your needs? Contact our experts today!