Chemical Vapor Deposition (CVD) reactors are categorized based on their design, operating conditions, and applications. The two primary reactor types are hot wall reactors and cold wall reactors, each with distinct advantages and disadvantages. Additionally, CVD processes can be classified into closed reactors and open reactors, depending on the gas flow system. Furthermore, CVD reactors are often tailored to specific processes such as Atmospheric Pressure CVD (APCVD), Low-Pressure CVD (LPCVD), Ultrahigh Vacuum CVD (UHV/CVD), and Plasma-Enhanced CVD (PECVD), each optimized for different materials and film deposition requirements. Understanding these reactor types is crucial for selecting the appropriate system for specific applications, such as semiconductor manufacturing, coatings, or nanotechnology.
Key Points Explained:
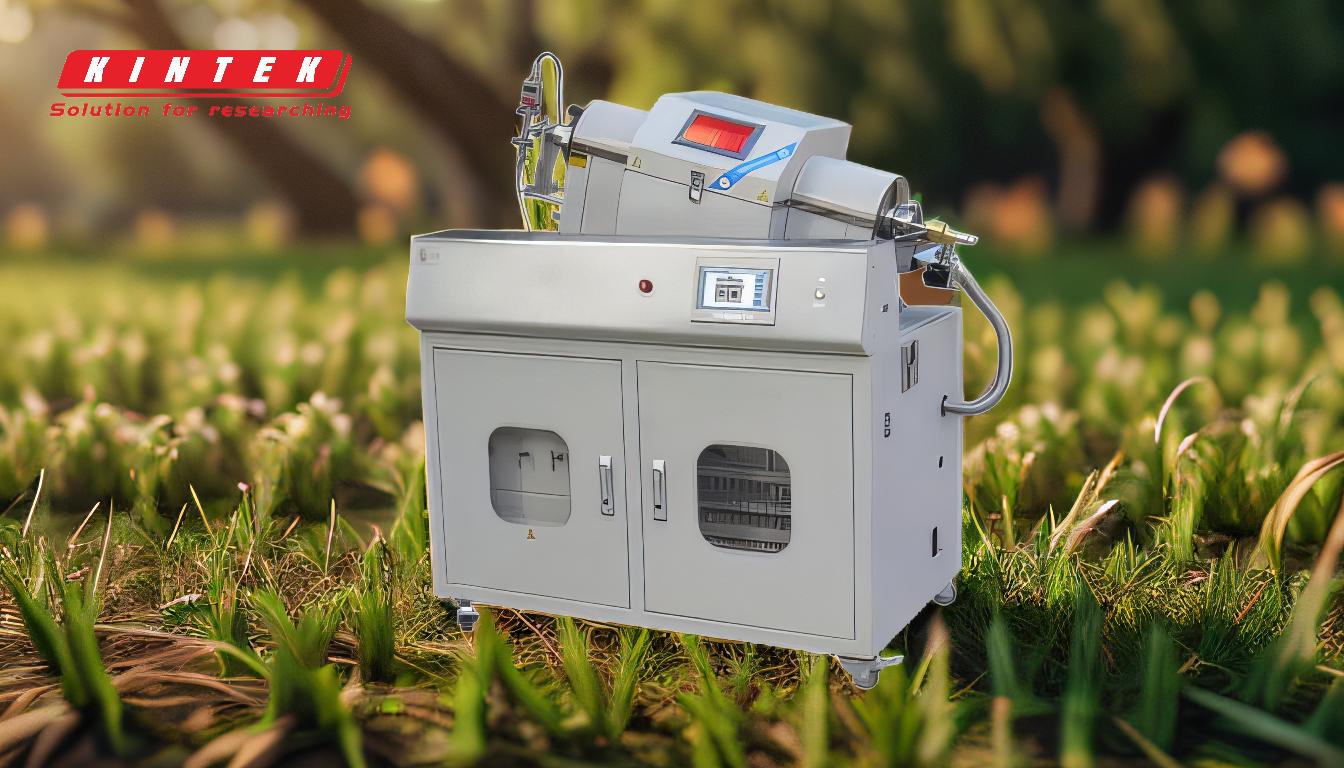
-
Hot Wall Reactors vs. Cold Wall Reactors
-
Hot Wall Reactors:
- The entire reactor chamber, including the walls, is heated uniformly.
- Commonly used in batch processing, where multiple wafers (100–200) are processed simultaneously.
-
Advantages:
- Uniform temperature distribution ensures consistent film deposition.
- Suitable for high-temperature processes like LPCVD.
-
Disadvantages:
- Higher energy consumption due to heating the entire chamber.
- Potential for unwanted deposition on chamber walls.
-
Cold Wall Reactors:
- Only the substrate is heated, while the chamber walls remain cool.
- Often used in single-wafer processing and integrated into cluster tools for advanced applications like gate stack processing.
-
Advantages:
- Energy-efficient since only the substrate is heated.
- Reduces unwanted deposition on chamber walls.
-
Disadvantages:
- Temperature gradients can lead to non-uniform film deposition.
- Requires precise control of heating systems.
-
Hot Wall Reactors:
-
Closed Reactors vs. Open Reactors
-
Closed Reactors:
- Reactants are placed in a sealed container, and the reaction occurs within this closed system.
- Suitable for small-scale or specialized applications.
-
Advantages:
- Minimal reactant loss.
- Controlled environment reduces contamination risks.
-
Disadvantages:
- Limited scalability for large-scale production.
- Difficult to replenish reactants during the process.
-
Open Reactors (Flowing-Gas CVD):
- Reactants are continuously introduced into the system, and byproducts are removed in a flowing gas stream.
- Commonly used in industrial applications.
-
Advantages:
- Scalable for high-volume production.
- Allows for continuous replenishment of reactants.
-
Disadvantages:
- Higher reactant consumption.
- Requires precise control of gas flow rates.
-
Closed Reactors:
-
Types of CVD Processes and Their Reactors
-
Atmospheric Pressure CVD (APCVD):
- Operates at ambient pressure.
- Used for depositing materials like silicon dioxide and silicon nitride.
- Reactor Type: Typically cold wall reactors to minimize energy consumption.
-
Low-Pressure CVD (LPCVD):
- Operates at reduced pressures (0.1–10 Torr).
- Used for depositing materials like polysilicon and silicon nitride.
- Reactor Type: Hot wall reactors for uniform temperature distribution.
-
Ultrahigh Vacuum CVD (UHV/CVD):
- Operates at extremely low pressures (below 10^-6 Torr).
- Used for high-purity films in advanced semiconductor applications.
- Reactor Type: Cold wall reactors to minimize contamination.
-
Plasma-Enhanced CVD (PECVD):
- Uses plasma to activate chemical reactions at lower temperatures.
- Used for depositing materials like silicon dioxide and silicon nitride at low temperatures.
- Reactor Type: Cold wall reactors to avoid plasma damage to chamber walls.
-
Atomic Layer Deposition (ALD):
- A variant of CVD that deposits films one atomic layer at a time.
- Used for ultra-thin, conformal films in nanotechnology.
- Reactor Type: Cold wall reactors for precise control.
-
Atmospheric Pressure CVD (APCVD):
-
Applications and Material Considerations
-
High-Temperature CVD:
- Used for depositing materials like silicon and titanium nitride at temperatures up to 1500°C.
- Reactor Type: Hot wall reactors for high-temperature stability.
-
Low-Temperature CVD:
- Used for depositing insulating layers like silicon dioxide at low temperatures.
- Reactor Type: Cold wall reactors to avoid substrate damage.
-
Plasma-Assisted CVD:
- Used for depositing materials like diamond-like carbon (DLC) and silicon carbide.
- Reactor Type: Cold wall reactors to prevent plasma damage.
-
Photo-Assisted CVD:
- Uses laser photons to activate chemical reactions.
- Used for precise, localized deposition.
- Reactor Type: Cold wall reactors for controlled laser interaction.
-
High-Temperature CVD:
-
Selection Criteria for CVD Reactors
-
Material Requirements:
- High-temperature materials like silicon carbide may require hot wall reactors, while low-temperature materials like silicon dioxide may use cold wall reactors.
-
Process Scale:
- Batch processing (hot wall reactors) for high-volume production.
- Single-wafer processing (cold wall reactors) for advanced, low-volume applications.
-
Energy Efficiency:
- Cold wall reactors are more energy-efficient for processes requiring localized heating.
-
Film Uniformity:
- Hot wall reactors provide better uniformity for large-scale batch processing.
-
Material Requirements:
By understanding these reactor types and their applications, equipment purchasers can make informed decisions based on their specific material, process, and production requirements.
Summary Table:
Reactor Type | Key Features | Applications |
---|---|---|
Hot Wall Reactors | Uniform heating, high energy consumption, batch processing | LPCVD, high-temperature processes |
Cold Wall Reactors | Energy-efficient, single-wafer processing, precise control | PECVD, UHV/CVD, ALD |
Closed Reactors | Minimal reactant loss, controlled environment, limited scalability | Small-scale or specialized applications |
Open Reactors | Scalable, continuous replenishment, higher reactant consumption | Industrial applications, high-volume production |
APCVD | Ambient pressure, cold wall reactors | Silicon dioxide, silicon nitride deposition |
LPCVD | Reduced pressure, hot wall reactors | Polysilicon, silicon nitride deposition |
UHV/CVD | Ultrahigh vacuum, cold wall reactors | High-purity films in advanced semiconductor applications |
PECVD | Plasma activation, cold wall reactors | Low-temperature deposition of silicon dioxide, silicon nitride |
ALD | Atomic layer deposition, cold wall reactors | Ultra-thin, conformal films in nanotechnology |
Looking for the right CVD reactor for your application? Contact our experts today to find the perfect solution!