Aluminum brazing is a complex process that requires precise control over various parameters to achieve high-quality joints. Defects in aluminum brazing can arise from several factors, including improper vacuum levels, inadequate temperature control, and poor part fixturing. Understanding these defects and their root causes is crucial for ensuring the reliability and performance of brazed components.
Key Points Explained:
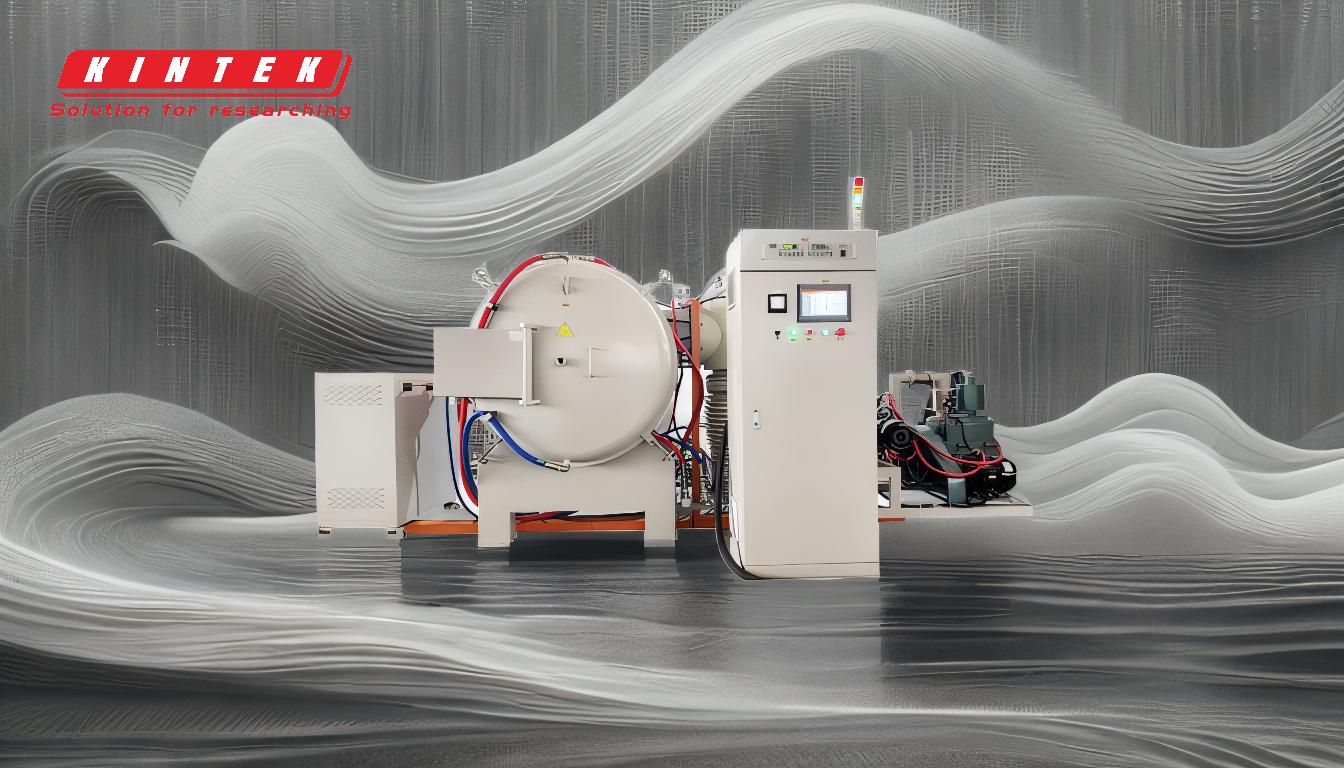
-
Vacuum Level Maintenance:
- Defect: Inadequate vacuum levels can lead to oxidation and contamination of the brazing surfaces, resulting in poor joint quality.
- Explanation: Maintaining vacuum levels in the 10^-5 mbar range or better is critical. This ensures that the brazing environment is free from contaminants that could interfere with the bonding process. Any deviation from this range can lead to incomplete wetting of the filler metal, causing voids and weak joints.
-
Heating Temperature:
- Defect: Incorrect heating temperatures can cause either insufficient melting of the filler metal or excessive melting, leading to joint failure.
- Explanation: The optimal heating temperature for aluminum brazing typically ranges between 575-590°C, depending on the alloy used. Ensuring that the parts reach the correct temperature is essential for the filler metal to flow properly and form a strong bond. Deviations from this range can result in incomplete bonding or excessive intermetallic formation, both of which compromise joint integrity.
-
Temperature Uniformity:
- Defect: Non-uniform heating can cause localized overheating or underheating, leading to inconsistent joint quality.
- Explanation: Temperature uniformity within ±5.5°C is crucial for achieving consistent brazing results. Non-uniform heating can cause some areas to reach the optimal temperature while others do not, leading to defects such as incomplete bonding, voids, and weak spots in the joint. Using multiple-zone temperature-controlled furnaces helps maintain uniform heating across the entire part.
-
Cycle Time:
- Defect: Improper cycle times can result in either insufficient or excessive heating, both of which can lead to joint defects.
- Explanation: Cycle times depend on the furnace type, part configuration, and part fixturing. If the cycle time is too short, the filler metal may not have enough time to flow and bond properly. Conversely, if the cycle time is too long, excessive intermetallic compounds may form, weakening the joint. Properly calibrated cycle times are essential for achieving optimal brazing results.
-
Part Fixturing:
- Defect: Poor fixturing can lead to misalignment, gaps, and inconsistent joint quality.
- Explanation: Proper part fixturing ensures that the components to be brazed are held in the correct position and alignment during the heating process. Misalignment or gaps between parts can prevent the filler metal from flowing evenly, leading to defects such as voids, incomplete bonding, and weak joints. High-quality fixturing is essential for maintaining consistent joint quality.
In summary, defects in aluminum brazing can be mitigated by maintaining precise control over vacuum levels, heating temperatures, temperature uniformity, cycle times, and part fixturing. Understanding and addressing these critical factors is essential for producing high-quality brazed joints that meet the required performance standards.
Summary Table:
Defect | Cause | Prevention |
---|---|---|
Oxidation/Contamination | Inadequate vacuum levels (below 10^-5 mbar) | Maintain vacuum levels in the 10^-5 mbar range or better. |
Insufficient/Excessive Melting | Incorrect heating temperatures (outside 575-590°C range) | Ensure precise temperature control within the optimal range. |
Non-Uniform Heating | Temperature variations exceeding ±5.5°C | Use multi-zone temperature-controlled furnaces for uniform heating. |
Improper Cycle Times | Cycle times too short or too long | Calibrate cycle times based on furnace type, part configuration, and fixturing. |
Misalignment/Gaps | Poor part fixturing | Use high-quality fixturing to ensure proper alignment and contact between parts. |
Ensure flawless aluminum brazing results—contact our experts today for tailored solutions!