Brazing is a versatile joining process that uses a filler metal to bond two or more materials together. The choice of brazing gas or atmosphere depends on the specific brazing method and the materials being joined. Common brazing gases include exothermic gas, hydrogen, argon, and vacuum atmospheres, each tailored to optimize the brazing process by preventing oxidation, ensuring proper filler metal flow, and achieving strong, clean joints. Understanding the types of brazing gases and their applications is essential for selecting the right method for a given project.
Key Points Explained:
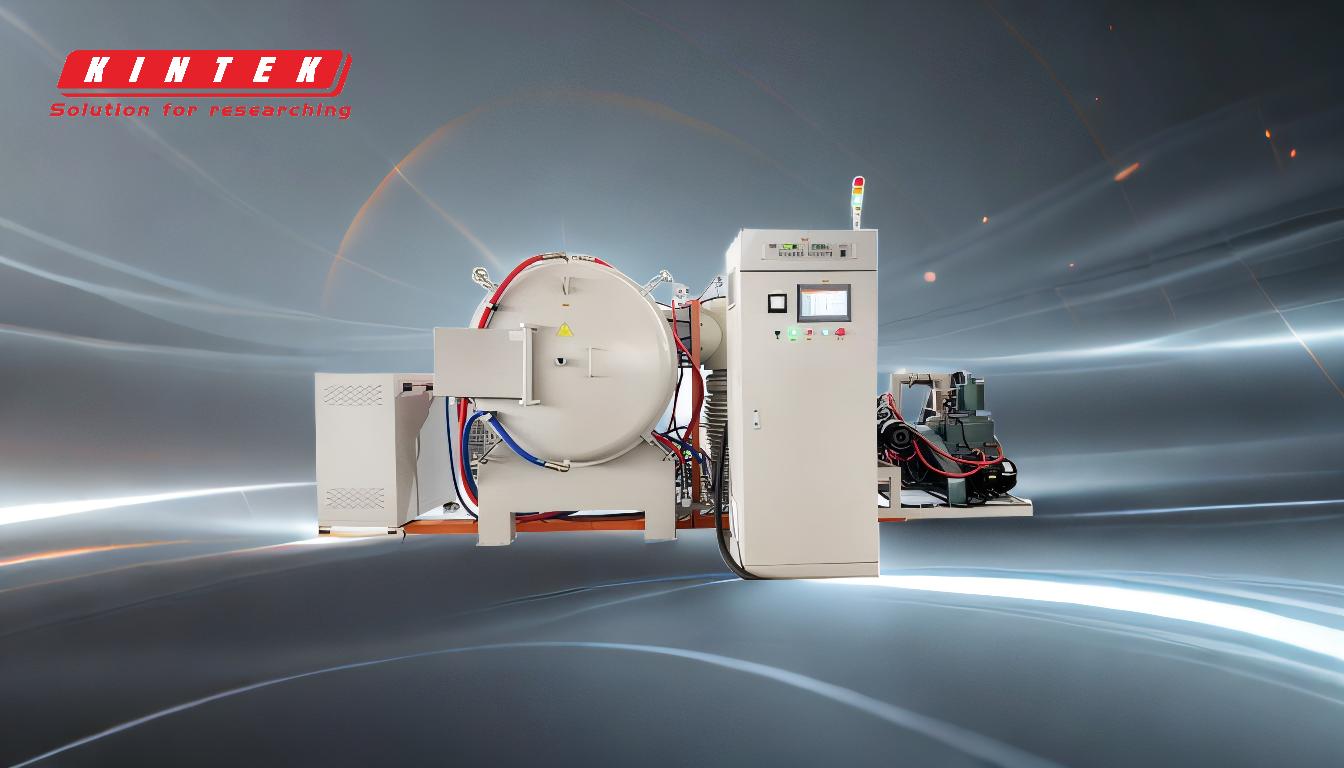
-
Torch Brazing:
- Torch brazing typically uses a fuel gas combined with oxygen or air to generate a flame. Common fuel gases include acetylene, propane, and natural gas.
- The flame heats the base metals and the filler metal, allowing the filler to melt and flow into the joint.
- This method is versatile and widely used for small-scale or manual brazing operations.
-
Furnace Brazing:
- Furnace brazing involves heating the assembly in a controlled atmosphere to prevent oxidation and ensure a clean joint.
- Exothermic Gas: A mixture of nitrogen, hydrogen, and carbon monoxide, often used for brazing carbon steels and other materials that require a reducing atmosphere.
- Hydrogen: Pure hydrogen is used for brazing materials like stainless steel and other alloys that are sensitive to oxidation. It provides a highly reducing environment.
- Argon: An inert gas that prevents oxidation and is suitable for brazing reactive metals like titanium and zirconium.
- Vacuum Atmosphere: Vacuum brazing eliminates the need for a protective gas by removing all air, making it ideal for high-temperature applications and materials that are highly reactive with oxygen.
-
Induction Brazing:
- Induction brazing uses electromagnetic induction to heat the joint area. The process often employs an inert gas like argon or nitrogen to shield the joint from oxidation.
- This method is precise and efficient, making it suitable for high-volume production and applications requiring localized heating.
-
Dip Brazing:
- Dip brazing involves immersing the assembly in a molten salt bath or a bath of molten filler metal. The salt bath acts as both a heat source and a protective atmosphere.
- This method is commonly used for aluminum and other non-ferrous metals.
-
Resistance Brazing:
- Resistance brazing uses electrical resistance to generate heat at the joint. An inert gas or flux is often used to protect the joint from oxidation.
- This method is ideal for small, precise joints and is commonly used in electrical and electronic applications.
-
Infrared Brazing:
- Infrared brazing uses focused infrared radiation to heat the joint. A protective gas like argon or nitrogen is often used to prevent oxidation.
- This method is suitable for delicate or complex assemblies.
-
Blanket Brazing:
- Blanket brazing involves using a flexible heating element wrapped around the assembly. A protective gas or vacuum is used to ensure a clean joint.
- This method is versatile and can be used for large or irregularly shaped components.
-
Electron Beam and Laser Brazing:
- Electron beam and laser brazing use highly focused energy beams to heat the joint. These methods often operate in a vacuum or use an inert gas shield.
- They are ideal for high-precision applications and materials that require minimal heat-affected zones.
-
Braze Welding:
- Braze welding uses a filler metal with a lower melting point than the base metals. A fuel gas like acetylene or propane is typically used to heat the joint.
- This method is suitable for repairing or joining dissimilar metals.
By understanding the different types of brazing gases and their applications, you can select the most appropriate method for your specific brazing needs, ensuring high-quality, durable joints.
Summary Table:
Brazing Method | Common Gases/Atmospheres | Key Applications |
---|---|---|
Torch Brazing | Acetylene, Propane, Natural Gas | Small-scale or manual brazing operations |
Furnace Brazing | Exothermic Gas, Hydrogen, Argon, Vacuum | Carbon steels, stainless steel, reactive metals, high-temperature applications |
Induction Brazing | Argon, Nitrogen | High-volume production, localized heating |
Dip Brazing | Molten Salt Bath | Aluminum and non-ferrous metals |
Resistance Brazing | Inert Gas, Flux | Electrical and electronic applications |
Infrared Brazing | Argon, Nitrogen | Delicate or complex assemblies |
Blanket Brazing | Protective Gas, Vacuum | Large or irregularly shaped components |
Electron Beam/Laser | Vacuum, Inert Gas | High-precision applications, minimal heat-affected zones |
Braze Welding | Acetylene, Propane | Repairing or joining dissimilar metals |
Need help selecting the right brazing gas for your project? Contact our experts today for personalized guidance!