Calcination is a thermal treatment process used to bring about a thermal decomposition, phase transition, or removal of a volatile fraction in materials. The equipment used for calcination, known as calciners, comes in various configurations, each designed to meet specific industrial needs. The primary types of calciners include muffle furnaces, reverberatory furnaces, and shaft furnaces or kilns. These types differ in design, operation, and application, making them suitable for different materials and processes. Below, we explore these types in detail, focusing on their unique features, advantages, and typical applications.
Key Points Explained:
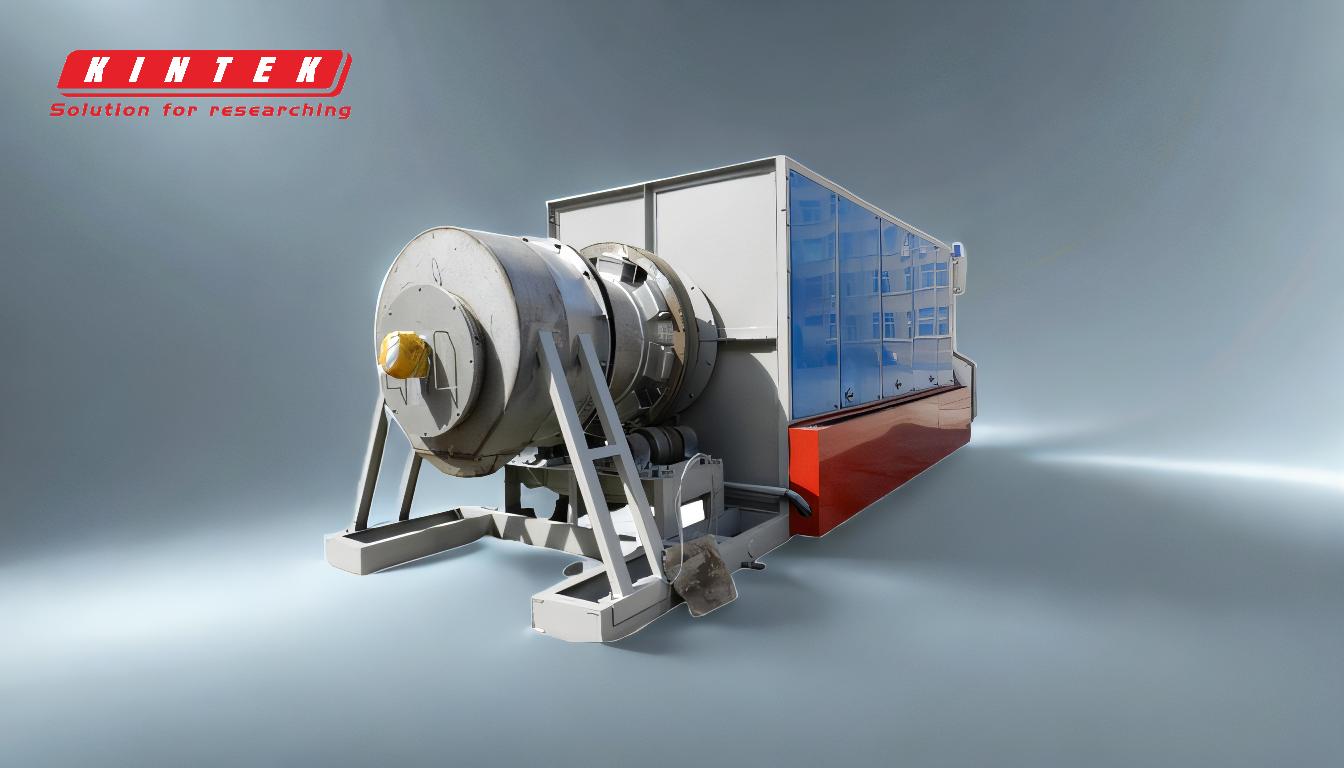
-
Muffle Furnaces
- Design and Operation: Muffle furnaces are designed with a separate chamber (the muffle) that isolates the material being processed from the combustion gases. This ensures that the material is heated indirectly, maintaining a clean and controlled environment.
-
Advantages:
- Precise temperature control.
- Protection of materials from contamination by combustion gases.
- Suitable for small-scale or laboratory applications.
-
Applications:
- Calcination of sensitive materials like ceramics, glass, and certain metals.
- Laboratory research and development.
-
Reverberatory Furnaces
- Design and Operation: Reverberatory furnaces feature a large, open chamber where heat is reflected (reverberated) from the roof and walls onto the material. The material is heated directly by the flames and indirectly by the reflected heat.
-
Advantages:
- High throughput for large-scale industrial processes.
- Ability to handle bulk materials.
- Uniform heating due to the reverberation of heat.
-
Applications:
- Calcination of ores, such as bauxite in the production of alumina.
- Processing of cement clinker and other industrial minerals.
-
Shaft Furnaces or Kilns
- Design and Operation: Shaft furnaces or kilns are vertical structures where material is fed from the top and moves downward through a heated zone. The heat is typically generated by burning fuel at the base, and the material is calcined as it descends.
-
Advantages:
- Efficient use of heat due to countercurrent flow of material and gases.
- Continuous operation, making it suitable for large-scale production.
- Compact design compared to horizontal furnaces.
-
Applications:
- Calcination of limestone to produce lime.
- Processing of iron ore pellets and other metallurgical applications.
-
Comparison of Calciner Types
- Scale of Operation: Muffle furnaces are ideal for small-scale or precise applications, while reverberatory and shaft furnaces are better suited for large-scale industrial processes.
- Material Compatibility: Muffle furnaces are preferred for sensitive materials, whereas reverberatory and shaft furnaces are used for bulk materials like ores and minerals.
- Energy Efficiency: Shaft furnaces are generally more energy-efficient due to their design, while muffle furnaces require more energy for indirect heating.
-
Selection Criteria for Calciners
- Material Properties: The type of material being processed (e.g., sensitivity to contamination, particle size) influences the choice of calciner.
- Production Scale: The required throughput determines whether a small-scale muffle furnace or a large-scale reverberatory or shaft furnace is needed.
- Temperature Requirements: Different calciners have varying temperature capabilities, which must align with the material's calcination temperature.
- Energy Efficiency: For cost-effective operations, energy efficiency is a critical factor, especially in large-scale industrial settings.
In summary, the choice of calciner depends on the specific requirements of the material and process. Muffle furnaces are ideal for precise, small-scale applications, reverberatory furnaces excel in large-scale industrial processes, and shaft furnaces offer energy-efficient continuous operation for bulk materials. Understanding these differences is crucial for selecting the right equipment for calcination needs.
Summary Table:
Calciner Type | Design & Operation | Advantages | Applications |
---|---|---|---|
Muffle Furnace | Separate chamber isolates material from combustion gases; indirect heating. | Precise temperature control, contamination-free, ideal for small-scale use. | Calcination of ceramics, glass, metals; lab R&D. |
Reverberatory Furnace | Open chamber with heat reflected from walls; direct and indirect heating. | High throughput, handles bulk materials, uniform heating. | Calcination of ores (e.g., bauxite), cement clinker, industrial minerals. |
Shaft Furnace/Kiln | Vertical structure; material descends through heated zone; countercurrent heat flow. | Energy-efficient, continuous operation, compact design. | Calcination of limestone, iron ore pellets, metallurgical applications. |
Need help choosing the right calciner for your process? Contact our experts today!