Chemical vapor deposition (CVD) coatings are versatile materials applied to surfaces through a high-temperature process that involves the reaction of volatile precursors. These coatings are known for their durability, high purity, and fine-grained structure, making them suitable for a wide range of applications, including wear resistance, corrosion protection, and high-temperature performance. CVD coatings are deposited at slow rates but offer exceptional hardness and environmental friendliness. Common types of CVD coatings include polysilicon, silicon dioxide, silicon nitride, metals, graphene, graphene nanoribbon, and diamond. Each type serves specific industrial needs, from enhancing tool longevity to enabling advanced electronics.
Key Points Explained:
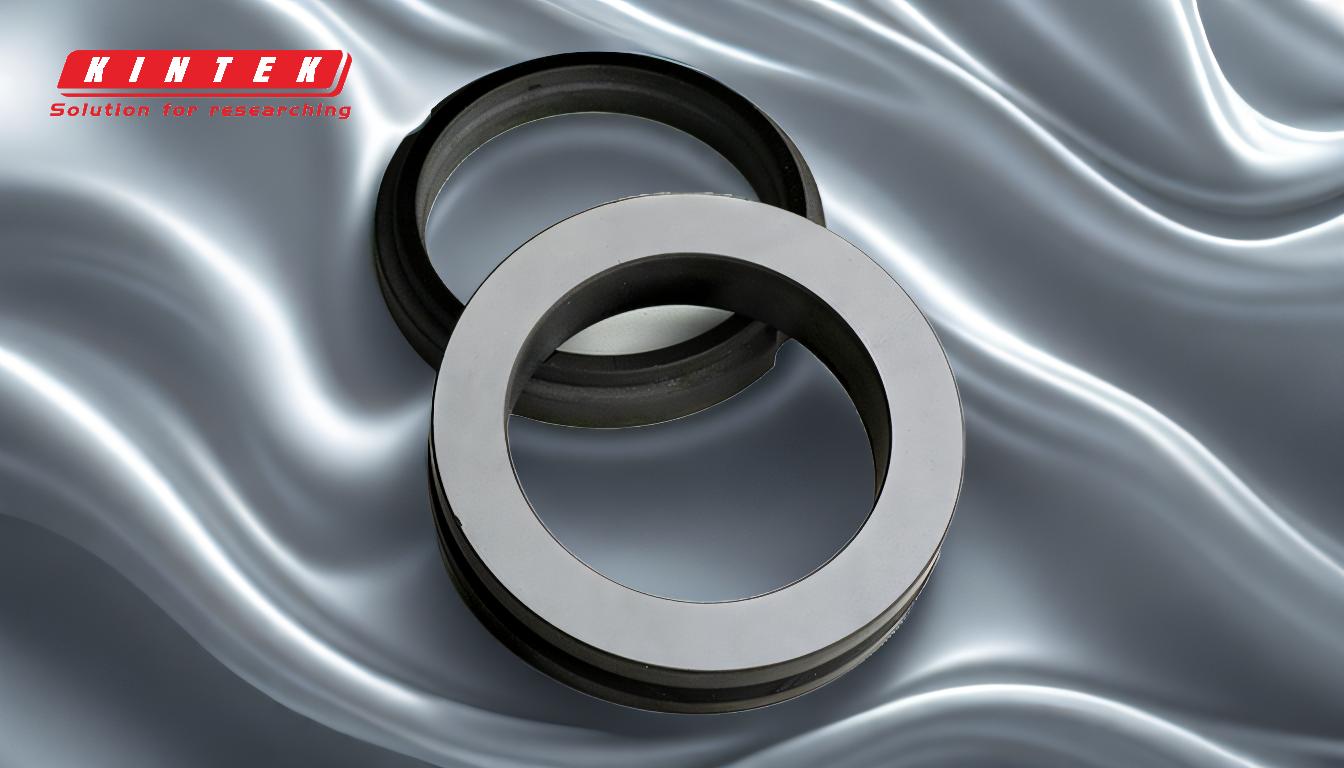
-
Overview of CVD Coatings:
- CVD coatings are created through a chemical vapor deposition process, where volatile precursors react or decompose at high temperatures to form a durable coating on a substrate.
- The process occurs under vacuum conditions, ensuring high purity and fine-grained coatings.
- These coatings are known for their hardness, impermeability, and environmental friendliness.
-
Types of CVD Coatings:
- Polysilicon: Used in semiconductor manufacturing and solar cell production due to its excellent electrical properties.
- Silicon Dioxide (SiO₂): Commonly applied as an insulating layer in microelectronics and optical applications.
- Silicon Nitride (Si₃N₄): Known for its high thermal stability and mechanical strength, used in cutting tools and high-temperature applications.
- Metals: CVD-deposited metals like tungsten and titanium are used in electronics and as protective coatings.
- Graphene: A single layer of carbon atoms with exceptional electrical and mechanical properties, used in advanced electronics and sensors.
- Graphene Nanoribbon: A derivative of graphene with tailored electronic properties for nanoscale devices.
- Diamond: Extremely hard and thermally conductive, used in cutting tools, wear-resistant coatings, and high-performance electronics.
-
Applications of CVD Coatings:
- Wear Resistance: CVD coatings like diamond and silicon nitride are applied to cutting tools and wear components to extend their lifespan.
- Corrosion Resistance: Coatings such as silicon dioxide and metals protect surfaces from chemical degradation.
- High-Temperature Protection: Silicon nitride and other refractory materials are used in environments with extreme heat.
- Erosion Protection: Coatings like diamond are used in applications where surfaces are exposed to abrasive conditions.
-
Properties of CVD Coatings:
- Fine-Grained Structure: Ensures uniformity and high performance.
- High Purity: Achieved through vacuum processing, making them suitable for sensitive applications like semiconductors.
- Hardness: CVD coatings are harder than conventionally produced ceramics, enhancing their durability.
- Impervious Nature: Provides excellent barrier properties against environmental factors.
-
Deposition Process:
- CVD coatings are deposited at slow rates, typically a few microns per minute.
- The process involves high temperatures, often exceeding the tempering temperature of materials like high-speed steel.
- Post-coating heat treatment is required to restore the hardness of the substrate.
-
Surface Characteristics:
- CVD coatings have a slightly rougher surface compared to the substrate, which can be beneficial for certain applications like adhesion enhancement.
- The film thickness is typically around 7.5 μm, providing a balance between performance and material usage.
-
Advantages of CVD Coatings:
- Durability: Suitable for high-performance applications in harsh environments.
- Environmental Friendliness: The process minimizes waste and harmful byproducts.
- Versatility: Can be tailored for a wide range of materials and applications.
By understanding the types, properties, and applications of CVD coatings, purchasers can make informed decisions based on the specific needs of their equipment or consumables.
Summary Table:
Aspect | Details |
---|---|
Types | Polysilicon, Silicon Dioxide, Silicon Nitride, Metals, Graphene, Diamond |
Properties | High purity, fine-grained structure, hardness, impervious nature |
Applications | Wear resistance, corrosion protection, high-temperature performance |
Deposition Process | High-temperature, vacuum conditions, slow deposition rates |
Advantages | Durability, environmental friendliness, versatility |
Ready to enhance your equipment with CVD coatings? Contact us today for expert guidance!