Physical vapor deposition (PVD) is a versatile and environmentally friendly technique used to create thin, high-purity coatings on substrates. The process involves vaporizing materials in a vacuum and depositing them atom by atom onto a surface. PVD is widely used in industries due to its ability to produce durable, high-performance coatings with precise control over composition and thickness. The two most common types of PVD are sputtering and evaporation, with evaporation further divided into thermal evaporation and electron-beam (e-beam) evaporation. These methods are chosen based on the specific requirements of the application, such as material compatibility, coating quality, and process efficiency.
Key Points Explained:
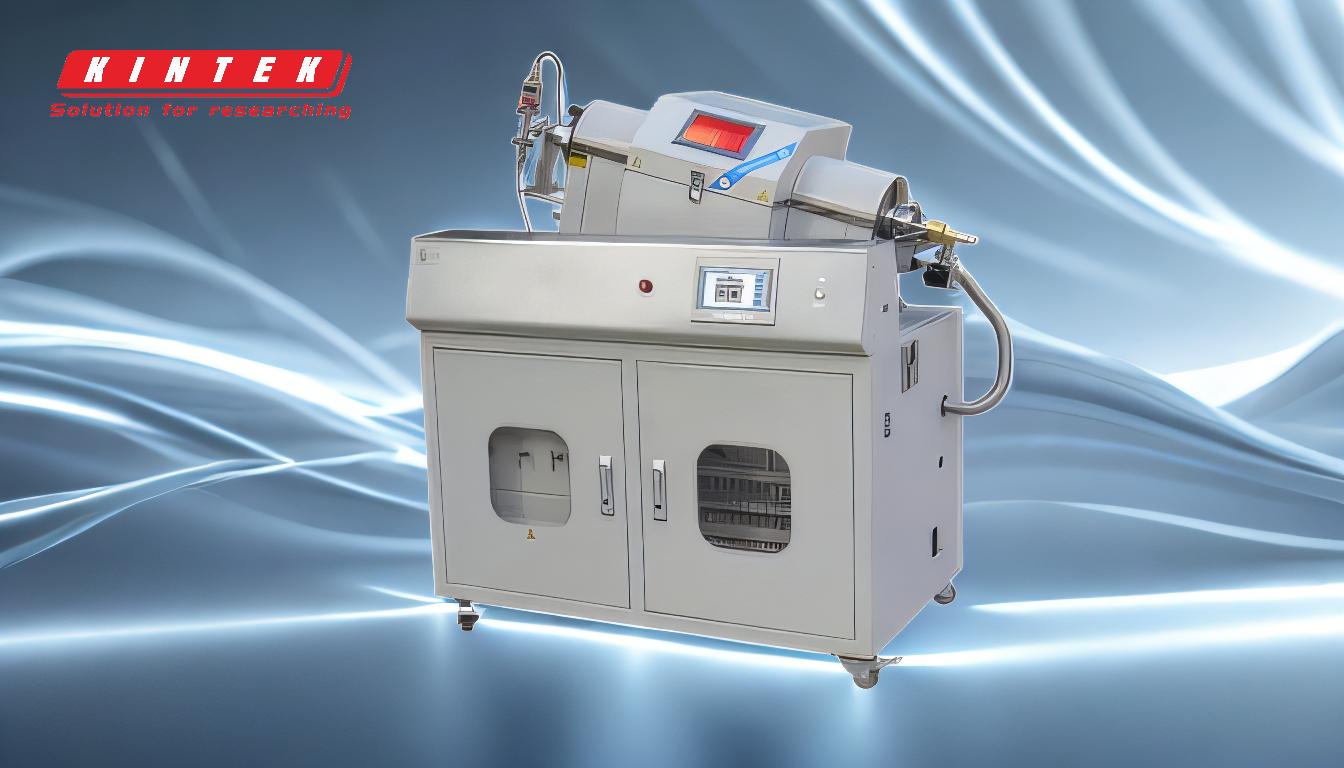
-
Sputtering in PVD:
- Sputtering is a widely used PVD technique where a target material is bombarded with high-energy ions, causing atoms to be ejected and deposited onto a substrate. This method is particularly effective for creating uniform and adherent coatings.
- Magnetron sputtering is a common variant that uses magnetic fields to enhance the efficiency of the sputtering process, making it suitable for depositing a wide range of materials, including metals, alloys, and ceramics.
- Sputtering is ideal for applications requiring high-quality, dense coatings with excellent adhesion and durability.
-
Evaporation in PVD:
- Evaporation involves heating a material in a vacuum until it vaporizes, and the vapor condenses onto a substrate to form a thin film. This method is divided into two main types:
- Thermal Evaporation: A simple and cost-effective method where the material is heated using a resistive heat source. It is commonly used for depositing metals and simple compounds.
- Electron-Beam (E-Beam) Evaporation: This method uses a focused electron beam to heat the material, allowing for the deposition of high-melting-point materials. It offers better control over film thickness and composition compared to thermal evaporation.
- Evaporation is preferred for applications requiring high-purity coatings and precise control over film properties.
- Evaporation involves heating a material in a vacuum until it vaporizes, and the vapor condenses onto a substrate to form a thin film. This method is divided into two main types:
-
Comparison of Sputtering and Evaporation:
- Material Compatibility: Sputtering is more versatile and can deposit a wider range of materials, including complex alloys and ceramics, while evaporation is better suited for simpler materials.
- Coating Quality: Sputtering produces denser and more adherent coatings, making it suitable for demanding applications. Evaporation, particularly e-beam evaporation, offers high-purity coatings with excellent uniformity.
- Process Efficiency: Sputtering is more efficient for large-scale production, while evaporation is often used for smaller, high-precision applications.
-
Advantages of PVD:
- PVD is environmentally friendly, as it does not require chemical reagents or post-treatment cleaning.
- It produces thin, pure coatings with excellent adhesion, resistance, and durability.
- The technique allows precise control over the composition and thickness of the coatings, making it suitable for a wide range of applications, from electronics to medical devices.
-
Applications of PVD:
- Electronics: PVD is used to deposit thin films for semiconductors, solar cells, and optical coatings.
- Medical Devices: The technique is used to create biocompatible coatings for implants and surgical instruments.
- Aerospace: PVD coatings enhance the performance and durability of components exposed to extreme conditions.
- Decorative Coatings: PVD is used to create durable and aesthetically pleasing finishes on consumer products.
-
Comparison with Chemical Vapor Deposition (CVD):
- While PVD relies on physical processes to deposit materials, microwave plasma chemical vapor deposition involves chemical reactions to form thin films. CVD is often used for depositing complex materials and achieving high deposition rates, but it requires higher temperatures and more complex equipment compared to PVD.
In summary, PVD techniques like sputtering and evaporation offer distinct advantages depending on the application. Sputtering is ideal for producing dense, high-quality coatings, while evaporation, particularly e-beam evaporation, excels in creating high-purity, precise films. Both methods are integral to modern manufacturing, offering environmentally friendly solutions for a wide range of industries.
Summary Table:
PVD Type | Subtypes | Key Features | Applications |
---|---|---|---|
Sputtering | Magnetron Sputtering | High-quality, dense coatings; excellent adhesion; versatile material deposition | Electronics, medical devices, aerospace, decorative coatings |
Evaporation | Thermal Evaporation | Cost-effective; simple process; suitable for metals and simple compounds | High-purity coatings, precise film control |
Electron-Beam Evaporation | High-melting-point materials; precise thickness and composition control | Semiconductors, optical coatings, advanced materials |
Discover which PVD technique is best for your application—contact our experts today!