Quenchants are essential in heat treatment processes to control the cooling rate of metals, ensuring desired mechanical properties and minimizing distortions. The primary types of quenchants include oil, water, polymer solutions, and specialized gases, each offering unique cooling characteristics. Oil quenchants, for instance, undergo three distinct cooling phases: vapor, boiling, and convection, which influence the hardness and structural integrity of the treated material. Water and polymer solutions provide faster cooling rates, suitable for specific applications, while vacuum quenching leverages controlled cooling to enhance mechanical properties. Selecting the appropriate quenchant depends on factors like material composition, part geometry, and desired outcomes.
Key Points Explained:
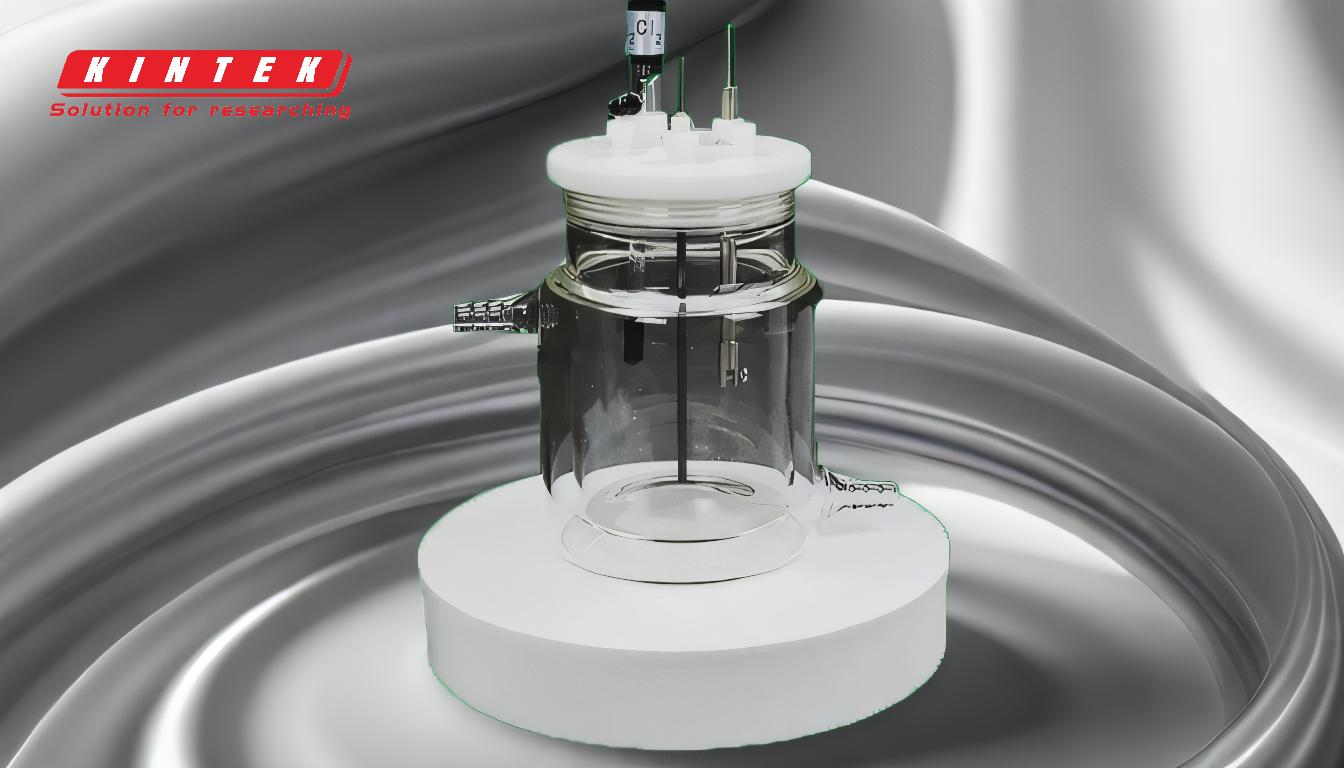
-
Oil Quenchants:
- Oil is one of the most commonly used quenchants due to its balanced cooling rate.
- It undergoes three cooling phases:
- Vapor Phase: Oil in contact with the heated part conducts heat, producing moderate cooling.
- Boiling Phase: The oil transforms into vapor, leading to the fastest cooling rate.
- Convection Phase: As the temperature lowers, the vapor phase dissipates, and convection completes the cooling process.
- The cooling rate of oil must be carefully controlled; insufficient cooling can result in low core hardness, while excessive cooling can cause part distortion or scrapping.
-
Water Quenchants:
- Water provides a faster cooling rate compared to oil, making it suitable for materials requiring rapid cooling.
- However, its aggressive cooling can lead to higher risks of distortion, cracking, or residual stresses in the treated parts.
- Water is often used for low-carbon steels and other materials that benefit from rapid quenching.
-
Polymer Quenchants:
- Polymer solutions, such as polyalkylene glycol (PAG), offer adjustable cooling rates by varying the concentration of the polymer in water.
- These quenchants are versatile and can be tailored to specific applications, reducing the risk of distortion and cracking.
- They are particularly useful for complex geometries or materials sensitive to thermal stresses.
-
Specialized Gas Quenchants:
- In processes like vacuum quenching, gases such as nitrogen or argon are used to cool the material at controlled rates.
- Gas quenching minimizes oxidation and distortion, making it ideal for high-precision components and advanced materials.
- The cooling rate is sufficient to trap diffused chemical elements, enhancing mechanical properties like hardness and strength.
-
Cooling Heterogeneities and Distortions:
- Variations in part thickness can lead to uneven cooling rates, causing martensitic transformations at different times.
- This can result in abrupt part expansion and distortions, which are inherent challenges in quenching operations.
- Proper selection of quenchants and cooling strategies is critical to mitigate these effects and achieve uniform hardness and dimensional stability.
-
Importance of Quenchant Selection:
- The choice of quenchant depends on factors such as material type, part geometry, and desired mechanical properties.
- For example, oil is preferred for medium-carbon steels, while water or polymer solutions may be better suited for low-carbon steels or complex shapes.
- Understanding the cooling phases and potential risks associated with each quenchant is essential for optimizing heat treatment processes.
By carefully selecting and controlling the quenching medium, manufacturers can achieve the desired balance between hardness, strength, and dimensional accuracy, ensuring high-quality heat-treated components.
Summary Table:
Quenchant Type | Cooling Rate | Key Characteristics | Applications |
---|---|---|---|
Oil | Moderate to Fast | Three cooling phases: vapor, boiling, convection; balanced cooling for medium-carbon steels. | Medium-carbon steels, general-purpose heat treatment. |
Water | Very Fast | Aggressive cooling; high risk of distortion or cracking. | Low-carbon steels, materials requiring rapid cooling. |
Polymer Solutions | Adjustable | Versatile cooling rates; reduces distortion and cracking. | Complex geometries, materials sensitive to thermal stresses. |
Specialized Gases | Controlled | Minimizes oxidation and distortion; ideal for high-precision components. | Vacuum quenching, advanced materials, high-precision components. |
Need help selecting the right quenchant for your heat treatment process? Contact our experts today for tailored solutions!