Atmospheric Pressure Chemical Vapor Deposition (APCVD) is a widely used technique for depositing thin films and coatings. While it offers several advantages, such as high deposition rates and the ability to coat complex shapes, it also has notable disadvantages. These include high operating temperatures, the need for toxic precursors, challenges in synthesizing multi-component materials, and limitations in coating large or complex surfaces. Additionally, the process often requires specialized equipment and cannot be performed on-site, making it less flexible for certain applications. Below, we explore these disadvantages in detail.
Key Points Explained:
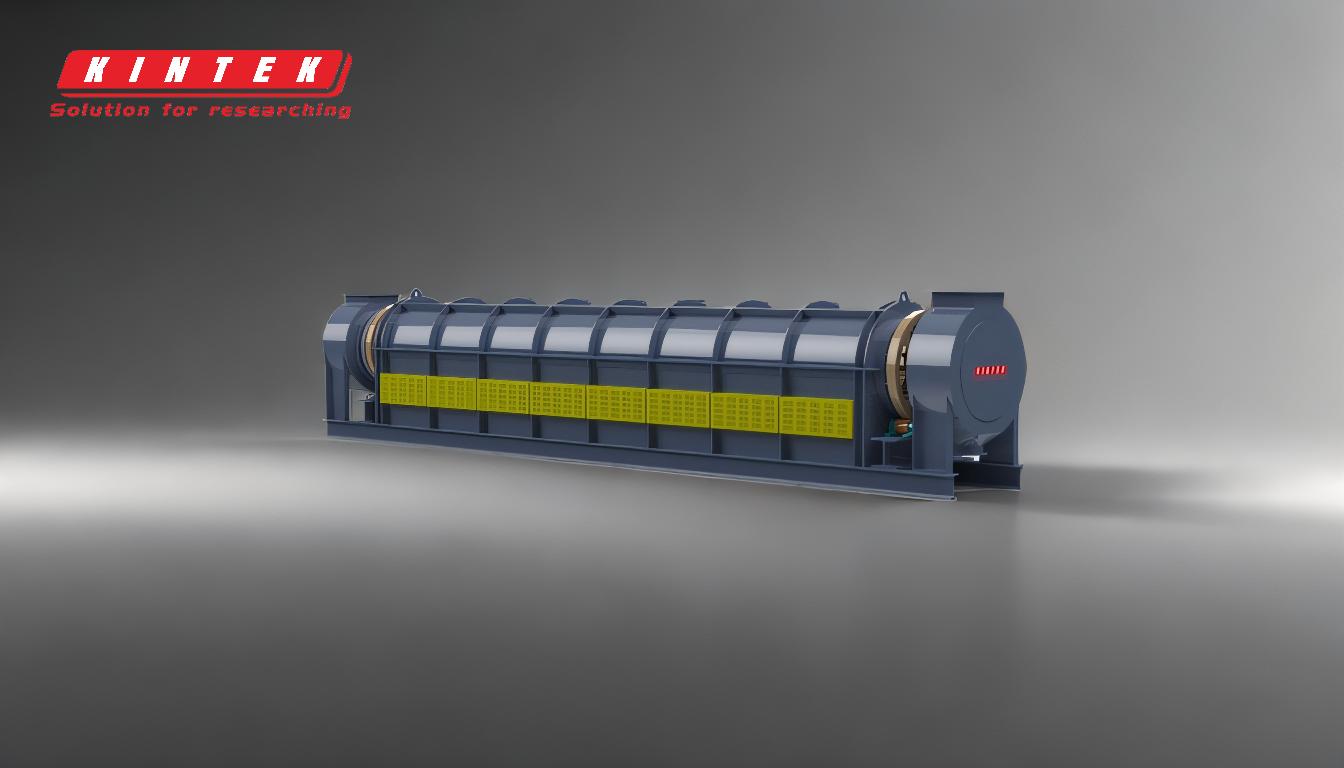
-
High Operating Temperatures:
- APCVD typically operates at high temperatures, which can lead to thermal instability in many substrates. This limits the types of materials that can be coated, as some substrates may degrade or warp under high heat.
- High temperatures also increase energy consumption, making the process less environmentally friendly and more costly.
-
Use of Toxic and Dangerous Precursors:
- APCVD requires chemical precursors with high vapor pressure, which are often toxic, corrosive, or pyrophoric. Handling these chemicals poses safety risks and requires stringent safety protocols.
- The by-products of the CVD process are often toxic and corrosive, requiring additional steps for neutralization and disposal, which increases operational costs.
-
Difficulty in Synthesizing Multi-Component Materials:
- Variations in vapor pressure, nucleation, and growth rates during the gas-to-particle conversion can lead to heterogeneous compositions in multi-component materials. This makes it challenging to achieve uniform and high-quality coatings.
- The lack of extremely volatile, non-toxic, and non-pyrophoric precursors further complicates the synthesis of complex materials.
-
Limitations in Coating Large or Complex Surfaces:
- The size of the vacuum chamber in APCVD systems is limited, making it difficult to coat large surfaces or components. This restricts the scalability of the process for industrial applications.
- While APCVD can coat complex shapes, achieving complete and uniform coverage can be challenging, as the process is often "all or nothing."
-
Inability to Perform On-Site Coating:
- APCVD cannot be performed on-site and requires components to be transported to specialized coating centers. This adds logistical complexity and costs, especially for large or heavy components.
- The need to disassemble parts into individual components for coating further increases preparation time and labor costs.
-
Environmental and Economic Concerns:
- The high energy consumption and use of hazardous chemicals make APCVD less sustainable compared to other deposition methods.
- The cost of equipment, maintenance, and waste management can be prohibitive for smaller-scale operations.
In summary, while APCVD is a powerful technique for thin film deposition, its disadvantages—such as high operating temperatures, toxic precursors, and scalability challenges—make it less suitable for certain applications. Understanding these limitations is crucial for equipment and consumable purchasers to make informed decisions about whether APCVD is the right choice for their specific needs.
Summary Table:
Disadvantage | Key Details |
---|---|
High Operating Temperatures | - Thermal instability in substrates - Increased energy costs |
Toxic and Dangerous Precursors | - Safety risks - Higher operational costs for neutralization and disposal |
Difficulty in Multi-Component Materials | - Heterogeneous compositions - Lack of suitable precursors |
Limited Coating for Large/Complex Surfaces | - Scalability challenges - Incomplete or non-uniform coverage |
Inability to Perform On-Site Coating | - Logistical complexity - Increased preparation time and labor costs |
Environmental and Economic Concerns | - High energy consumption - Prohibitive costs for smaller-scale operations |
Need help deciding if APCVD is right for your application? Contact our experts today for personalized guidance!