CVD (Chemical Vapor Deposition) graphene, while promising for its high quality, scalability, and cost-effectiveness, has several notable disadvantages. These include challenges in separating graphene from the substrate without damaging its structure, limitations due to high processing temperatures, and issues with tensile stress and cracking in thick coatings. Additionally, the process requires substrates that can withstand high temperatures, and the separation techniques can sometimes degrade the graphene's quality. Despite its potential in applications like transparent conductive films and replacing silicon technology, these drawbacks hinder its widespread adoption in certain industrial applications.
Key Points Explained:
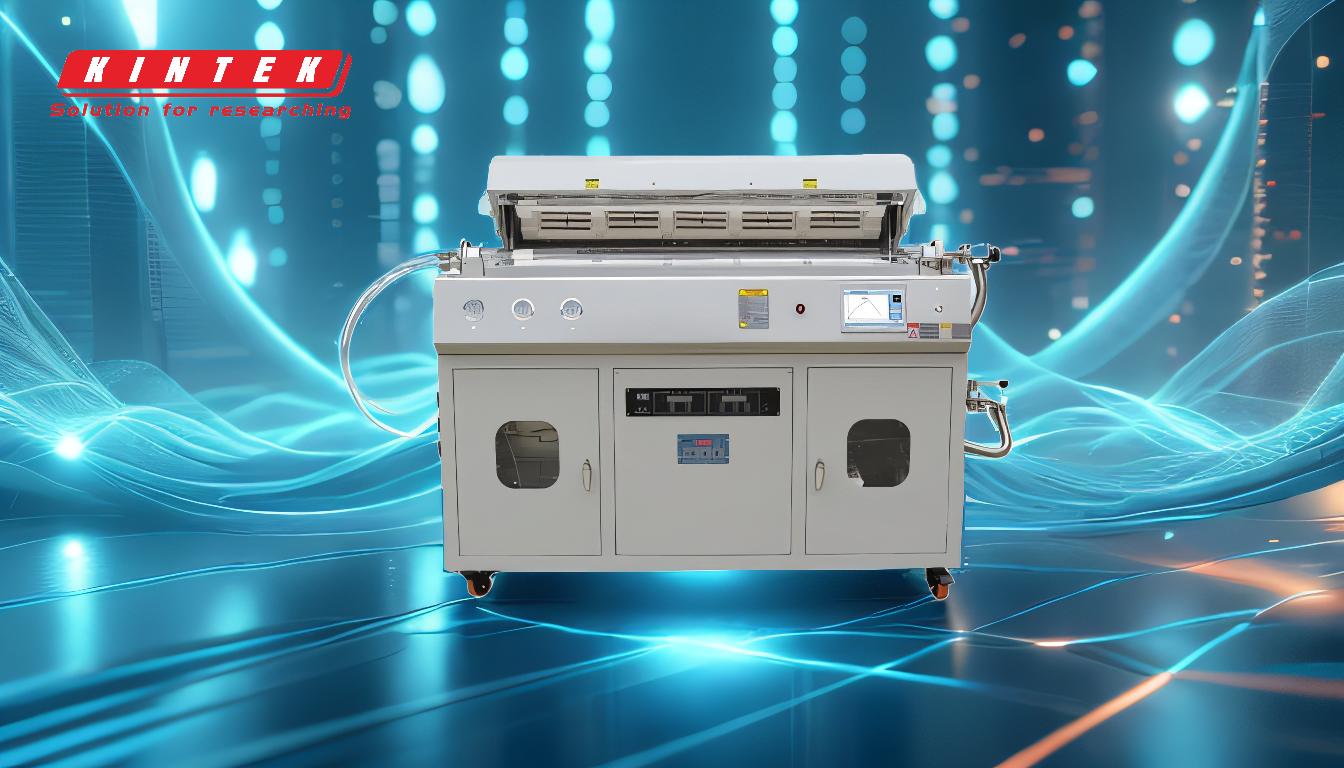
-
High Processing Temperature:
- CVD graphene production typically requires temperatures between 800°C to 1000°C. This high-temperature requirement limits the choice of substrates to those that can withstand such conditions, such as cemented carbide. This constraint can increase production costs and complexity.
-
Tensile Stress and Cracking:
- The thick coatings (10~20μm) produced by CVD can generate tensile stress during the cooling process. This stress can lead to the formation of fine cracks, which may spread under external impact, causing the coating to peel off. This makes CVD less suitable for applications involving interrupted cutting processes like milling, where the cutting force is not uniform and continuous.
-
Separation Challenges:
- One of the main challenges in CVD graphene production is the successful separation or exfoliation of graphene from the substrate without damaging its structure or affecting its properties. The relationship between graphene and the substrate is not fully understood, making separation techniques substrate-dependent. Some methods, such as dissolving the substrate in harmful acids, can adversely affect the quality of the graphene.
-
Quality Degradation During Separation:
- Techniques used to separate graphene from the substrate can sometimes degrade the quality of the graphene. For example, using harmful acids to dissolve the substrate can introduce impurities or damage the graphene's structure, reducing its effectiveness in applications requiring high purity and structural integrity.
-
Scalability vs. Quality Trade-off:
- While CVD is considered one of the best methods for producing high-quality graphene on a large scale, there is often a trade-off between scalability and quality. Ensuring high homogeneity, imperviousness, and fine grains across large areas can be challenging, and any compromise in these areas can limit the graphene's performance in critical applications.
-
Material Limitations:
- The need for high-temperature-resistant substrates and the potential for quality degradation during separation limit the types of materials that can be used in CVD graphene production. This can restrict the versatility of CVD graphene in various industrial applications, where different substrate materials might be required.
-
Environmental and Safety Concerns:
- The use of harmful chemicals in the separation process raises environmental and safety concerns. Proper handling and disposal of these chemicals are necessary to mitigate their impact, adding to the overall cost and complexity of the production process.
In summary, while CVD graphene offers significant advantages in terms of quality, scalability, and cost-effectiveness, its disadvantages—such as high processing temperatures, separation challenges, and material limitations—present notable hurdles that need to be addressed for broader industrial adoption.
Summary Table:
Disadvantage | Description |
---|---|
High Processing Temperature | Requires 800°C to 1000°C, limiting substrate choices and increasing costs. |
Tensile Stress and Cracking | Thick coatings can crack under stress, making CVD unsuitable for interrupted processes. |
Separation Challenges | Difficulty in separating graphene from substrates without damage. |
Quality Degradation During Separation | Use of harmful acids can degrade graphene quality. |
Scalability vs. Quality Trade-off | Challenges in maintaining quality at large scales. |
Material Limitations | High-temperature-resistant substrates are required, limiting versatility. |
Environmental and Safety Concerns | Harmful chemicals in separation processes raise safety and environmental issues. |
Interested in learning more about CVD graphene and its applications? Contact us today for expert insights!