Heat treatment, while essential for enhancing the mechanical properties of metals, comes with several disadvantages, particularly when considering controlled and ordinary atmosphere methods. Controlled atmosphere heat treatment can lead to surface roughness, loss of surface metal elements, and challenges in gas management, while ordinary atmosphere heat treatment often results in surface oxidation and a harsh working environment. Both methods have limitations in terms of applicability and operational challenges, which can impact the quality and efficiency of the treatment process.
Key Points Explained:
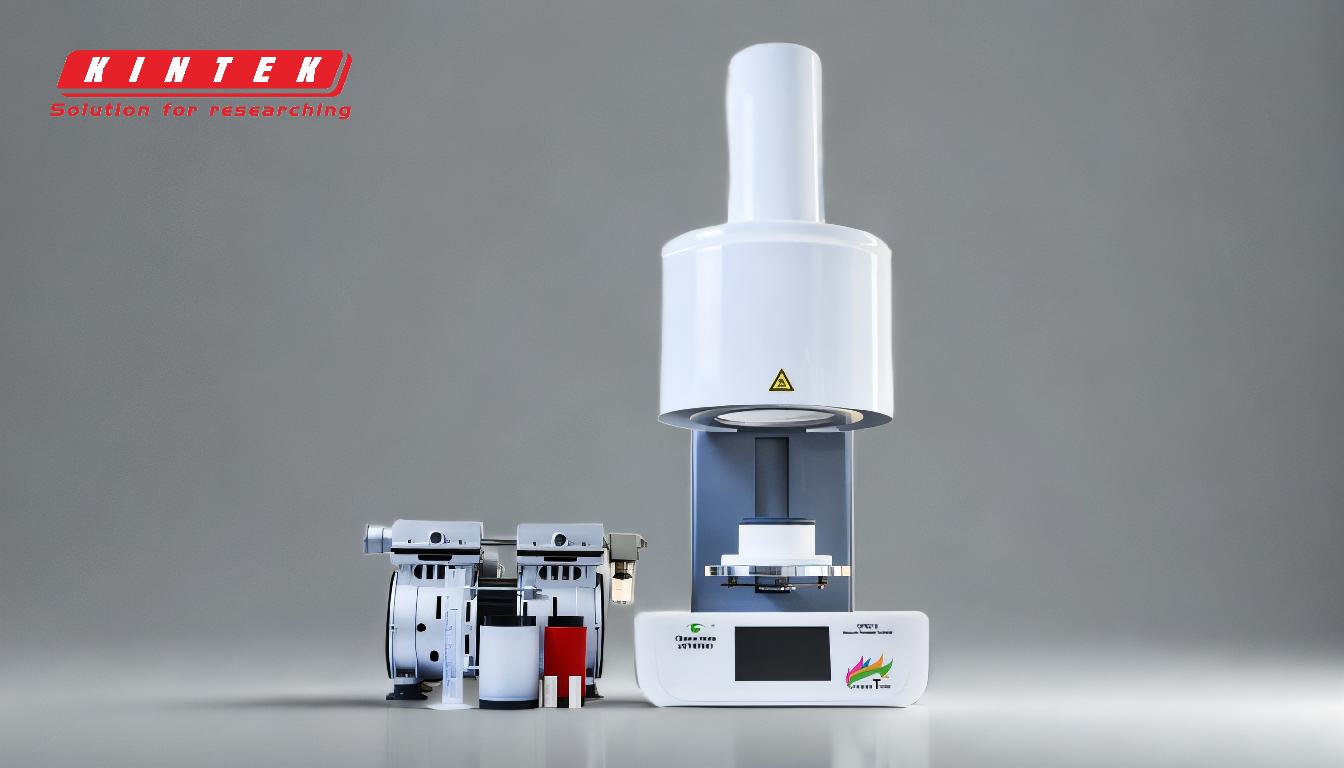
-
Surface Quality Issues in Controlled Atmosphere Heat Treatment:
- Rough and Non-Bright Surface: Controlled atmosphere heat treatment often results in a rough and non-bright surface on the workpiece. This can be problematic for applications requiring a smooth and aesthetically pleasing finish.
- Loss of Surface Metal Elements: The process can lead to the depletion of certain metal elements from the surface, which might affect the material's overall properties and performance.
-
Operational Challenges in Controlled Atmosphere Heat Treatment:
- Erosion of Electric Heating Elements: The environment within a controlled atmosphere furnace can cause erosion of the electric heating elements, leading to increased maintenance costs and potential downtime.
- Gas Usage and Recovery: Managing the gases used in the process and recovering reducing gases can be complex and costly, adding to the operational challenges.
-
Surface Oxidation in Ordinary Atmosphere Heat Treatment:
- Oxide Film Formation: Ordinary atmosphere heat treatment typically results in the formation of an oxide film on the workpiece surface. This oxide layer can affect the material's properties and may require additional processing to remove.
-
Harsh Treatment Environment:
- Environmental Conditions: Both controlled and ordinary atmosphere heat treatments often involve harsh environmental conditions, which can be challenging for operators and may require specialized equipment and safety measures.
-
Limited Applicability:
- Material and Application Constraints: The applicability of both heat treatment methods can be limited by the type of material being treated and the specific requirements of the application. This can restrict the use of these methods in certain industries or for particular components.
In summary, while heat treatment is a critical process for improving material properties, it comes with several disadvantages that need to be carefully managed. These include surface quality issues, operational challenges, environmental concerns, and limitations in applicability. Understanding these drawbacks is essential for selecting the appropriate heat treatment method and ensuring the desired outcomes in material processing.
Summary Table:
Disadvantage | Controlled Atmosphere | Ordinary Atmosphere |
---|---|---|
Surface Quality | Rough and non-bright surface; loss of surface metal elements | Oxide film formation |
Operational Challenges | Erosion of electric heating elements; complex gas management | Harsh working environment |
Environmental Impact | Harsh conditions for operators; specialized equipment required | Harsh conditions for operators; specialized equipment required |
Applicability | Limited by material type and application requirements | Limited by material type and application requirements |
Need help selecting the right heat treatment method for your materials? Contact our experts today for tailored solutions!