Inductive heating, while advantageous in many applications, has several notable disadvantages. These include high initial costs, the need for specialized equipment and skilled personnel, limitations in refining capacity, challenges in managing heat distribution, and the requirement for dedicated inductors. Additionally, inductive heating systems often require robust control algorithms to handle varying loads and operating points, and they may face issues with uneven heat distribution and high heating rates. These factors can make inductive heating less flexible and more expensive compared to other heating methods.
Key Points Explained:
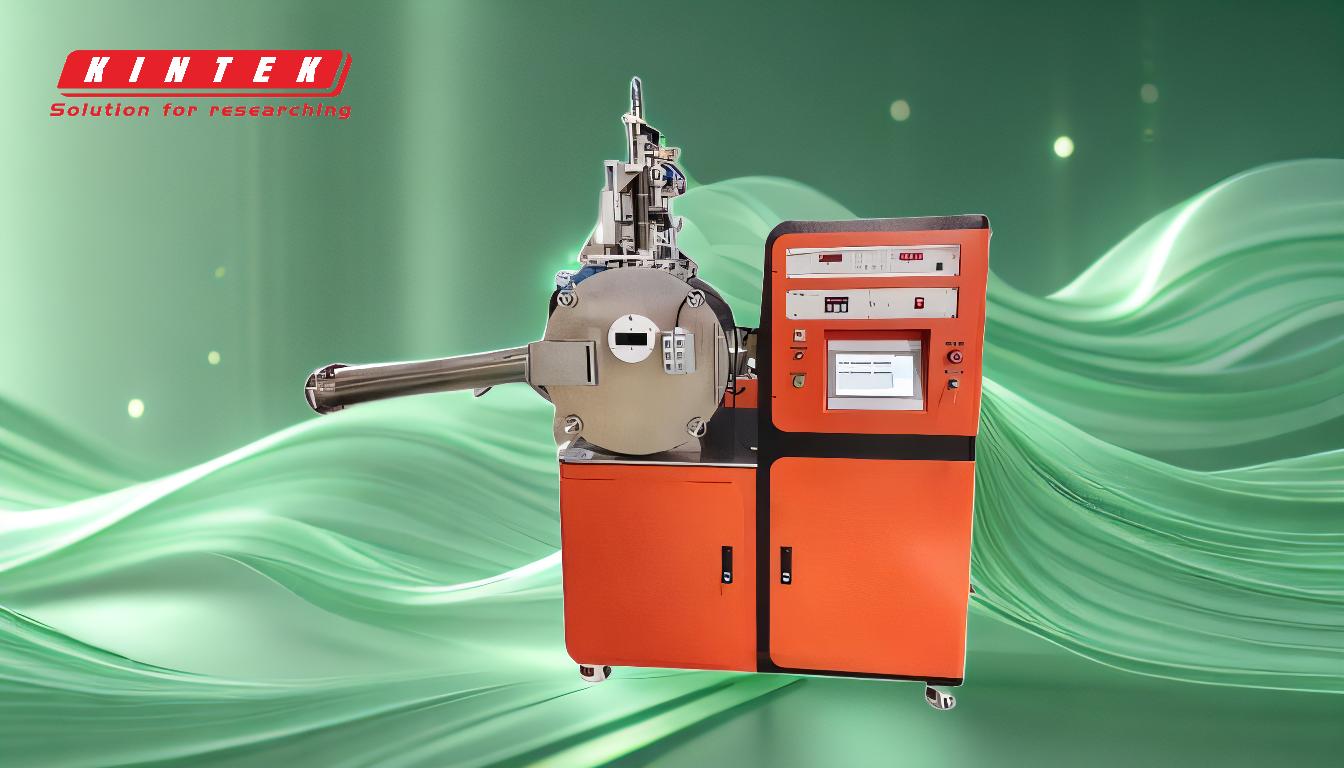
-
High Initial Investment
- Induction heating systems require significant upfront costs, including specialized equipment such as high-frequency generators and power supplies.
- The need for skilled personnel with expertise in induction heating principles and safety procedures further adds to the operational expenses.
- This makes inductive heating less accessible for small-scale operations or applications with limited budgets.
-
Lack of Refining Capacity
- Induction furnaces cannot refine materials, meaning the charge materials must be free of oxides and of a known composition.
- Some alloying elements may be lost due to oxidation during the heating process, requiring them to be re-added to the melt.
- This limitation makes inductive heating unsuitable for applications requiring material purification or refining.
-
Need for Dedicated Inductors
- The flexibility of inductive heating is constrained by the need to produce custom inductors for specific applications.
- These inductors can be expensive to design and manufacture, particularly for complex or unique geometries.
- Managing high-current densities in small copper inductors often requires specialized engineering and precise "copper-fitting," further increasing costs.
-
Challenges in Heat Distribution
- Inductive heating can result in uneven heat distribution, which may lead to inconsistent material properties in the final product.
- High heating rates can exacerbate this issue, causing thermal stress or damage to the material.
- Proper alignment and good inductive coupling are critical to achieving uniform heating, adding complexity to the process.
-
Dependence on Thermal Conductivity
- The effectiveness of inductive heating depends on the thermal conductivity of the material being heated.
- Materials with poor thermal conductivity may not heat evenly, limiting the applicability of inductive heating in certain scenarios.
- This reliance on material properties restricts the versatility of inductive heating compared to other methods like convection or radiation-based heating.
-
Complex Control Requirements
- Robust control algorithms are necessary to manage power converters for different induction heating loads and operating points.
- Multi-coil systems present additional challenges, requiring real-time identification and adaptive algorithms for optimal performance.
- These control complexities can increase the cost and difficulty of implementing inductive heating systems.
-
Surface Heating Limitations
- Induction heating is most effective for surface heating, which may not be suitable for applications requiring uniform heating throughout the material.
- This limitation restricts its use in certain heat treatment processes where deep or volumetric heating is necessary.
-
Energy Efficiency Concerns
- While inductive heating can be energy-efficient for specific applications, the high-frequency generators and power supplies required consume significant energy.
- Inefficiencies in the system, such as poor inductive coupling or heat loss, can further reduce overall energy efficiency.
-
Maintenance and Operational Challenges
- The specialized nature of inductive heating equipment often necessitates regular maintenance and troubleshooting by skilled technicians.
- Operational challenges, such as managing high-current densities and ensuring proper alignment, can lead to downtime and increased operational costs.
-
Limited Flexibility for Diverse Applications
- The need for custom inductors and the dependence on material properties limit the adaptability of inductive heating for diverse applications.
- Other heating methods, such as gas furnaces or electric furnaces, may offer greater flexibility for a wider range of materials and processes.
In summary, while inductive heating offers precision and efficiency in specific applications, its disadvantages—such as high costs, limited refining capacity, and challenges in heat distribution and control—make it less suitable for certain scenarios. Understanding these limitations is crucial for making informed decisions when selecting heating methods for industrial or manufacturing processes.
Summary Table:
Disadvantage | Description |
---|---|
High Initial Investment | Significant upfront costs for equipment and skilled personnel. |
Lack of Refining Capacity | Cannot refine materials; requires pre-purified charge materials. |
Need for Dedicated Inductors | Custom inductors are expensive and limit flexibility. |
Challenges in Heat Distribution | Uneven heating can lead to inconsistent material properties. |
Dependence on Thermal Conductivity | Limited effectiveness for materials with poor thermal conductivity. |
Complex Control Requirements | Requires robust algorithms for varying loads and operating points. |
Surface Heating Limitations | Not suitable for deep or uniform heating applications. |
Energy Efficiency Concerns | High energy consumption and potential inefficiencies. |
Maintenance Challenges | Requires skilled technicians and regular maintenance. |
Limited Flexibility | Less adaptable for diverse applications compared to other heating methods. |
Need help choosing the right heating method for your application? Contact our experts today for personalized advice!