Physical Vapor Deposition (PVD) is a widely used coating technique with several advantages, such as improved material properties, environmental friendliness, and versatility in material usage. However, it also has notable disadvantages that can impact its suitability for certain applications. These include high capital costs, slow deposition rates, line-of-sight limitations, and the need for skilled operators and specialized equipment like cooling systems. Additionally, PVD processes often require high vacuums and temperatures, which can complicate operations and increase costs. Understanding these drawbacks is essential for equipment and consumable purchasers to make informed decisions.
Key Points Explained:
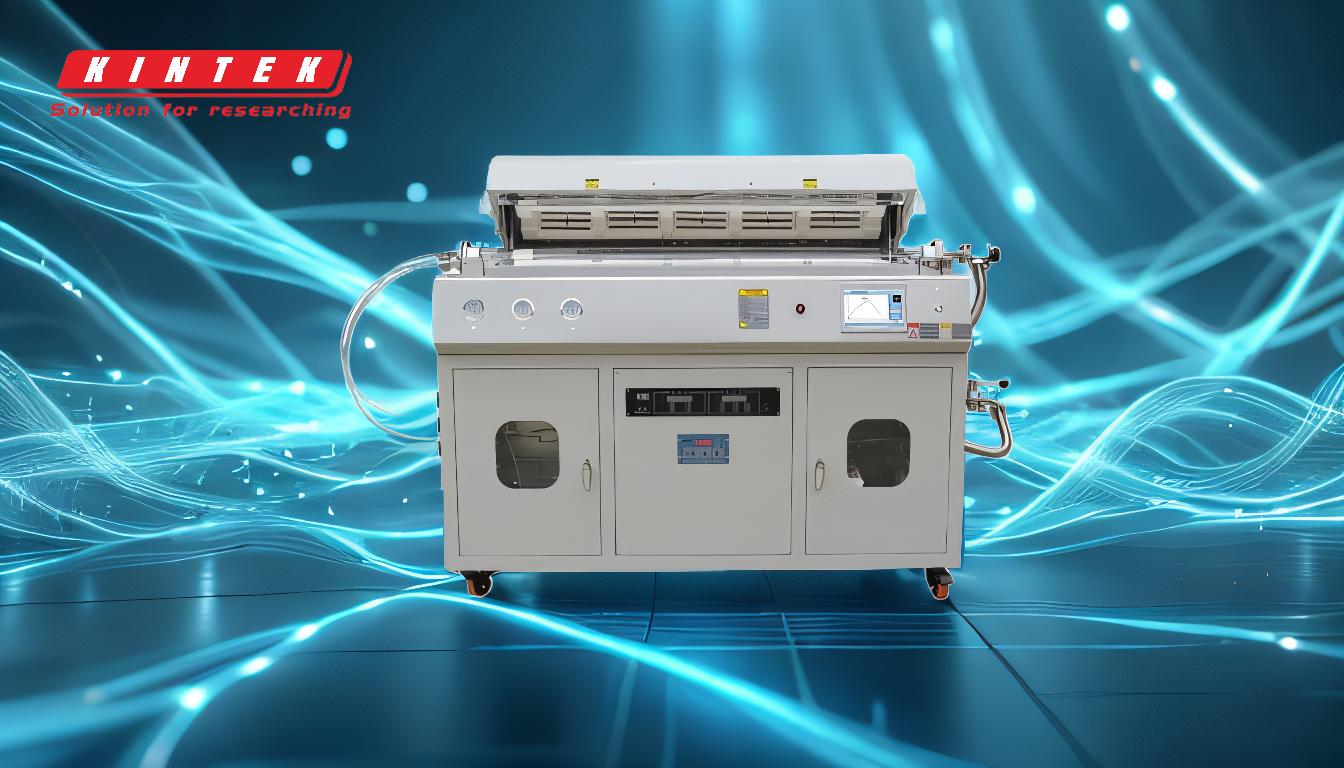
-
Line-of-Sight Limitation:
- PVD is a line-of-sight technique, meaning it can only coat surfaces directly exposed to the vapor source. This makes it difficult to coat complex geometries, such as undercuts, holes, or intricate surface features. For example, if a workpiece has hidden or recessed areas, these sections may remain uncoated, limiting the uniformity and effectiveness of the coating.
-
High Capital Cost:
- The equipment required for PVD is expensive, involving vacuum chambers, high-temperature systems, and cooling mechanisms. This makes the initial investment significantly higher compared to other coating methods, which can be a barrier for smaller operations or budget-conscious purchasers.
-
Slow Deposition Rate:
- PVD has a relatively slow deposition rate, typically ranging from 1 to 2 Ångströms per second (Å/s). This slow rate can lead to longer processing times, reducing throughput and efficiency, especially in high-volume production environments.
-
High Vacuum and Temperature Requirements:
- Many PVD processes require high vacuums and elevated temperatures (320 to 900 degrees Fahrenheit). These conditions necessitate skilled operators and specialized equipment, increasing operational complexity and costs. Additionally, maintaining high vacuums can be energy-intensive and time-consuming.
-
Need for Cooling Systems:
- PVD processes generate significant heat, particularly in techniques like sputtering or arc evaporation. To manage this, robust cooling systems are required, adding to the overall cost and complexity of the setup.
-
High Stress in Coatings:
- PVD coatings often exhibit high residual stress, which can lead to issues like cracking or delamination, especially in applications requiring thick coatings or those subjected to mechanical stress.
-
Limited Scalability:
- PVD is less scalable compared to other deposition methods, making it less suitable for large-scale production. This limitation can affect industries that require high throughput, such as automotive or consumer electronics.
-
Time-Consuming Process:
- The combination of slow deposition rates, high vacuum requirements, and cooling needs makes PVD a time-consuming process. This can be a disadvantage in industries where rapid turnaround times are critical.
-
Unsuitable for Certain Geometries:
- Due to its line-of-sight nature, PVD is not ideal for coating complex or hidden surfaces. This limitation can restrict its use in applications requiring uniform coverage on intricate parts.
-
Environmental and Operational Challenges:
- While PVD is more environmentally friendly than alternatives like electroplating, it still requires significant energy and resources to maintain high vacuums and temperatures. Additionally, the need for skilled personnel and specialized equipment can pose operational challenges.
By understanding these disadvantages, purchasers can better evaluate whether PVD is the right choice for their specific needs, considering factors like cost, application requirements, and production scale.
Summary Table:
Disadvantage | Explanation |
---|---|
Line-of-Sight Limitation | Cannot coat complex geometries or hidden surfaces effectively. |
High Capital Cost | Expensive equipment like vacuum chambers and cooling systems. |
Slow Deposition Rate | Rates range from 1 to 2 Å/s, leading to longer processing times. |
High Vacuum and Temperature Needs | Requires skilled operators and specialized equipment, increasing costs. |
Need for Cooling Systems | Generates significant heat, necessitating robust cooling mechanisms. |
High Stress in Coatings | May cause cracking or delamination in thick or mechanically stressed coatings. |
Limited Scalability | Less suitable for large-scale production due to throughput limitations. |
Time-Consuming Process | Slow rates, high vacuum, and cooling needs extend processing times. |
Unsuitable for Certain Geometries | Struggles with intricate or hidden surfaces, limiting uniform coverage. |
Environmental and Operational Challenges | High energy use and resource requirements for vacuums and temperatures. |
Need help deciding if PVD is right for your application? Contact our experts today for personalized guidance!