Sputtering is a widely used thin film deposition technique known for its high purity, precise control, and uniformity. However, it comes with several disadvantages that can impact its efficiency, cost, and application suitability. Key drawbacks include slower deposition rates, high equipment and operational costs, sensitivity to heat, film contamination risks, and challenges in achieving uniform film thickness. Additionally, sputtering faces limitations in material selection, process control, and integration with other fabrication techniques. These factors make it less ideal for certain applications, particularly those requiring high throughput, low contamination, or complex material combinations.
Key Points Explained:
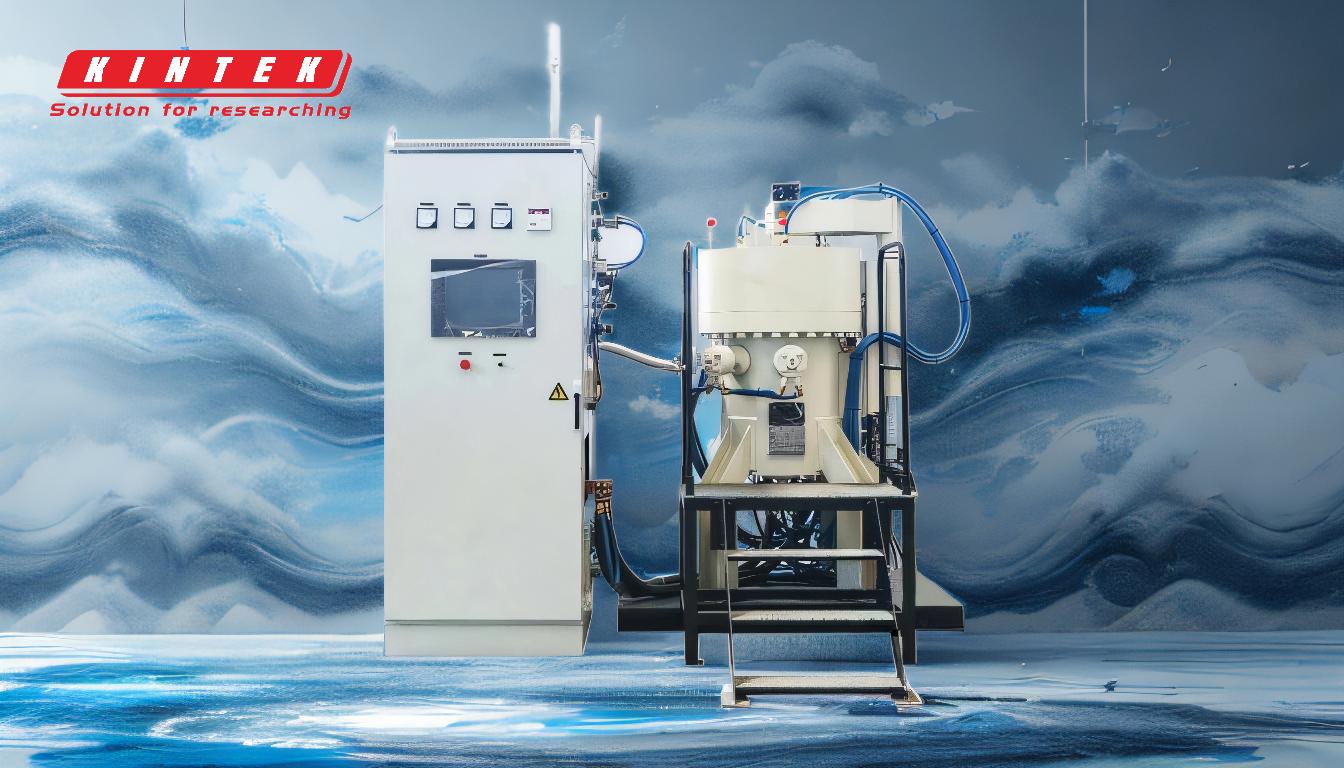
-
Slower Deposition Rates
- Sputtering typically has lower deposition rates compared to methods like thermal evaporation. This is due to the physical nature of the process, where atoms are ejected from a target material and deposited onto a substrate. The slower rate can limit throughput, making it less suitable for high-volume production.
-
High Equipment and Operational Costs
- Sputtering systems are expensive to purchase and maintain. The need for high-quality vacuum systems, RF or DC power sources, and cooling systems adds to the overall cost. Additionally, sputtering targets are often costly, and material use can be inefficient, further increasing expenses.
-
Heat Sensitivity and Cooling Requirements
- A significant portion of the energy used in sputtering is converted into heat, which must be effectively removed to prevent damage to the substrate or target. Cooling systems are required, but they can reduce production rates and increase energy consumption, adding to operational costs.
-
Film Contamination Risks
- Sputtering can introduce contamination into the deposited film. Impurities from the target material or gaseous contaminants in the plasma can become activated and incorporated into the film. This is particularly problematic in reactive sputtering, where careful control of gas composition is necessary to avoid target poisoning.
-
Challenges in Achieving Uniform Film Thickness
- The deposition flux distribution in sputtering is often non-uniform, especially for large substrates or targets. Moving fixtures or complex setups may be required to achieve uniform thickness, which adds complexity and cost to the process.
-
Limitations in Material Selection
- Sputtering is constrained by the melting temperatures and properties of target materials. Some materials may not be suitable for sputtering due to their low melting points or other physical characteristics, limiting the range of coatings that can be produced.
-
Difficulty in Combining with Lift-Off Processes
- Sputtering is challenging to integrate with lift-off processes used in film structuring. The diffuse transport of sputtered atoms makes full shadowing impossible, leading to contamination and difficulties in achieving precise patterns.
-
Active Control Challenges
- Compared to other deposition methods like pulsed laser deposition, sputtering offers less active control over layer-by-layer growth. This can limit its use in applications requiring precise atomic-level control.
-
High Operating Pressures and Sealing Issues
- Traditional sputtering processes operate at relatively high pressures, which can lead to permeation through elastomer seals and other vacuum system challenges. These issues can affect the quality and efficiency of the deposition process.
-
Plasma Density Unevenness
- For large rectangular cathodes (e.g., >1m), achieving uniform plasma density can be difficult, leading to uneven layer thickness distribution. This requires additional engineering solutions to address.
-
Energy Inefficiency
- Most of the energy incident on the target is converted into heat rather than being used for deposition, making the process less energy-efficient compared to other techniques.
-
Reactive Sputtering Complications
- In reactive sputtering, precise control of gas composition is critical to avoid target poisoning, where the target surface becomes chemically altered, reducing deposition efficiency and film quality.
By understanding these disadvantages, equipment and consumable purchasers can make informed decisions about whether sputtering is the right technique for their specific applications, considering factors like cost, throughput, and material requirements.
Summary Table:
Disadvantage | Key Details |
---|---|
Slower Deposition Rates | Lower throughput compared to methods like thermal evaporation. |
High Equipment and Operational Costs | Expensive systems, vacuum requirements, and costly sputtering targets. |
Heat Sensitivity | Requires cooling systems, reducing production rates and increasing energy use. |
Film Contamination Risks | Impurities from targets or plasma can affect film quality. |
Uniform Film Thickness Challenges | Non-uniform deposition flux, especially for large substrates. |
Material Selection Limitations | Constrained by target material properties and melting points. |
Integration with Lift-Off Processes | Difficult to combine with precise film structuring techniques. |
Active Control Challenges | Less precise layer-by-layer growth compared to other methods. |
High Operating Pressures | Can lead to vacuum system challenges and sealing issues. |
Plasma Density Unevenness | Difficult to achieve uniform plasma density for large cathodes. |
Energy Inefficiency | Most energy is converted into heat, not deposition. |
Reactive Sputtering Complications | Requires precise gas control to avoid target poisoning. |
Need help deciding if sputtering is right for your application? Contact our experts today for tailored advice!