Thermal Vapour Deposition (TVD), particularly thermal evaporation, is a widely used technique in thin-film deposition due to its simplicity and cost-effectiveness. However, it comes with several disadvantages that limit its application in certain scenarios. These drawbacks include poor film uniformity, high impurity levels, low-density film quality, moderate film stress, and limited scalability. Additionally, thermal evaporation is restricted to materials with relatively low melting points and is prone to contamination from the crucible. These limitations make it less suitable for advanced applications requiring high-purity, high-density, or multi-component materials.
Key Points Explained:
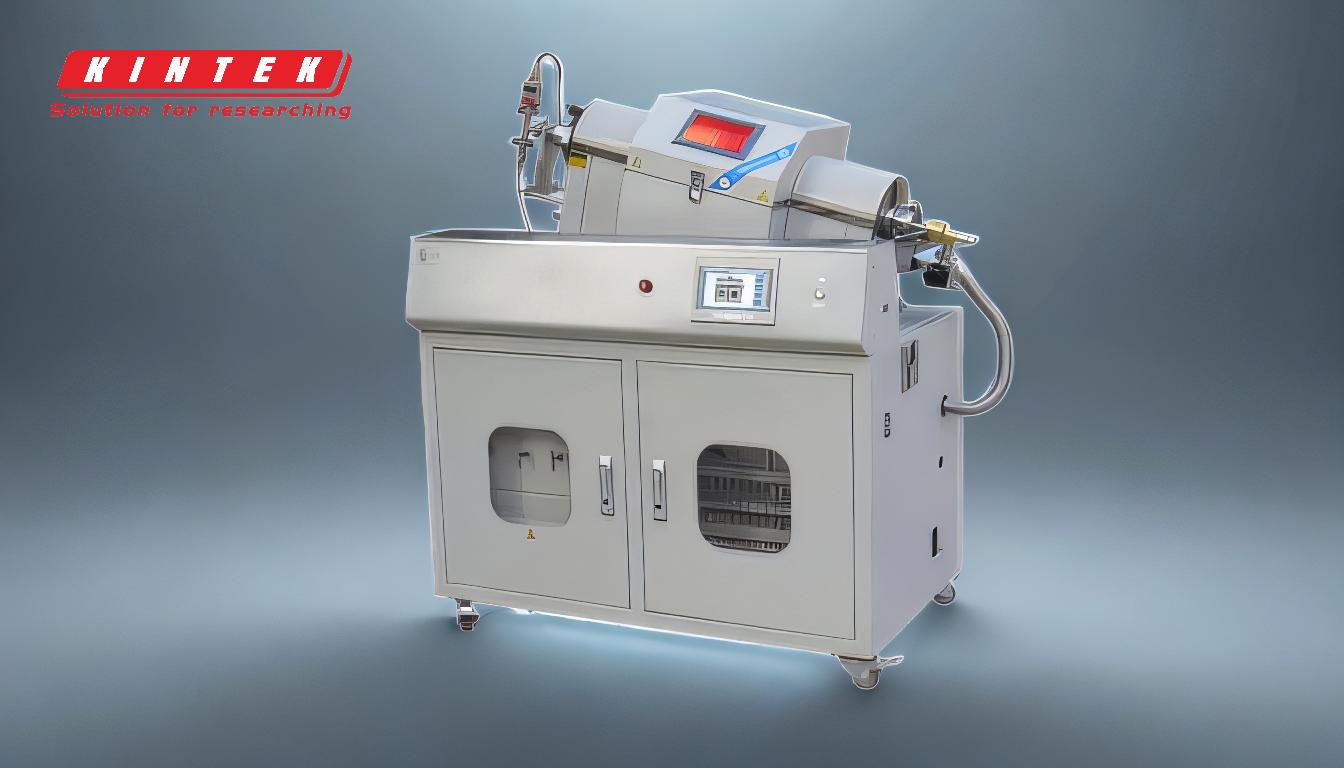
-
Poor Film Uniformity:
- Without the use of planetary systems and masks, thermal evaporation often results in uneven film thickness across the substrate. This is a significant drawback for applications requiring precise and uniform coatings.
- The lack of uniformity can lead to inconsistent material properties, which is particularly problematic in industries like electronics and optics.
-
High Impurity Levels:
- Thermal evaporation typically has the highest impurity levels among Physical Vapor Deposition (PVD) methods. This is due to contamination from the crucible and the evaporation source material.
- High impurity levels can degrade the performance of the deposited film, making it unsuitable for high-purity applications such as semiconductor manufacturing.
-
Low-Density Film Quality:
- Films produced by thermal evaporation often have low density, which can affect their mechanical and electrical properties. Although this can be improved with ion-assist techniques, it adds complexity and cost to the process.
- Low-density films are more prone to defects and may not provide the necessary durability for certain applications.
-
Moderate Film Stress:
- The films deposited by thermal evaporation often exhibit moderate stress, which can lead to issues like cracking or delamination over time.
- This is particularly problematic in applications where the film needs to withstand mechanical stress or thermal cycling.
-
Limited Scalability:
- Thermal evaporation is not easily scalable for large-area or high-throughput applications. The process is generally slower and less efficient compared to other deposition methods like sputtering or chemical vapor deposition (CVD).
- This limitation makes it less attractive for industrial-scale production.
-
Material Limitations:
- Thermal evaporation is primarily suitable for materials with relatively low melting points. It is not effective for depositing refractory metals or materials that require very high temperatures.
- This restricts the range of materials that can be deposited using this method, limiting its versatility.
-
Crucible Contamination:
- The use of a crucible in thermal evaporation can introduce contaminants into the deposited film, further reducing its purity and quality.
- This is a significant drawback for applications requiring high-purity materials, such as in the semiconductor or optical industries.
-
Challenges in Multi-Component Materials:
- Thermal evaporation is less effective for depositing multi-component materials due to variations in vapor pressure, nucleation, and growth rates among different components.
- This makes it difficult to achieve a homogeneous composition, which is crucial for many advanced applications.
In summary, while thermal evaporation is a simple and cost-effective method for thin-film deposition, its disadvantages—such as poor uniformity, high impurity levels, low-density films, moderate stress, limited scalability, material limitations, crucible contamination, and challenges with multi-component materials—make it less suitable for advanced or high-precision applications. For more information on thermal evaporation, you can visit thermal evaporation.
Summary Table:
Disadvantage | Description |
---|---|
Poor Film Uniformity | Uneven thickness, inconsistent material properties, problematic for electronics. |
High Impurity Levels | Contamination from crucible and source material, unsuitable for high-purity uses. |
Low-Density Film Quality | Prone to defects, affects mechanical and electrical properties. |
Moderate Film Stress | Leads to cracking or delamination, issues under mechanical or thermal stress. |
Limited Scalability | Not suitable for large-area or high-throughput industrial applications. |
Material Limitations | Restricted to low melting point materials, limits versatility. |
Crucible Contamination | Introduces impurities, reduces film purity and quality. |
Challenges in Multi-Component Materials | Difficult to achieve homogeneous composition for advanced applications. |
Need a better solution for thin-film deposition? Contact our experts today to explore advanced alternatives!