Three-plate molds, while offering advantages in certain applications, come with several notable disadvantages that can impact manufacturing efficiency and cost. These molds are more complex to design and manufacture compared to two-plate molds, leading to higher costs, increased weight, and longer lead times. The additional complexity also results in higher machining costs, making them less economical for some projects. Understanding these drawbacks is crucial for equipment or consumable purchasers to make informed decisions based on their specific needs and budget constraints.
Key Points Explained:
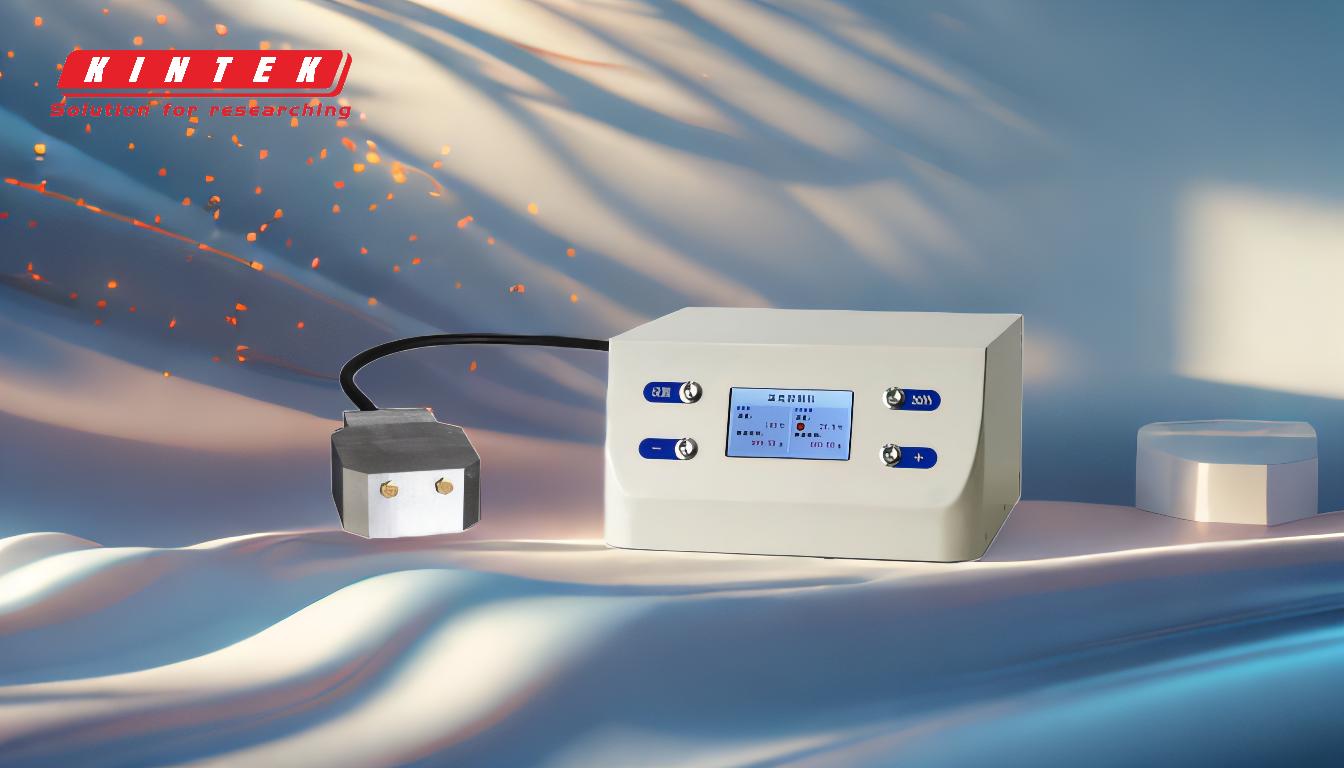
-
Higher Manufacturing Costs
- Three-plate molds are inherently more complex than two-plate molds due to their additional plate and intricate runner systems.
- This complexity requires more advanced design and engineering, which increases the overall manufacturing cost.
- For purchasers, this means a higher upfront investment, which may not be justified for simpler projects or low-volume production.
-
Increased Machining Costs
- The additional plate and runner system in three-plate molds require precise machining to ensure proper alignment and functionality.
- Machining these components is more labor-intensive and time-consuming, further driving up costs.
- This can be a significant drawback for projects with tight budgets or those requiring quick turnaround times.
-
Heavier Mold Weight
- The inclusion of an extra plate adds to the overall weight of the mold.
- Heavier molds can complicate handling, transportation, and installation, potentially requiring specialized equipment or additional labor.
- This added weight may also limit the compatibility of the mold with certain injection molding machines, restricting its use in some facilities.
-
Longer Lead Times
- The increased complexity of three-plate molds extends the time required for design, machining, and assembly.
- Longer lead times can delay production schedules, which may be a critical factor for time-sensitive projects.
- Purchasers must account for these delays when planning their production timelines to avoid bottlenecks.
-
Limited Cost-Effectiveness for Simple Projects
- While three-plate molds are advantageous for complex parts or multi-cavity designs, they may not be cost-effective for simpler projects.
- The additional costs and lead times associated with these molds may outweigh their benefits in cases where two-plate molds could suffice.
- Purchasers should carefully evaluate the specific requirements of their project to determine if the added complexity is justified.
-
Potential for Increased Maintenance
- The additional components in three-plate molds, such as the extra plate and runner system, create more opportunities for wear and tear.
- This can lead to higher maintenance requirements and increased downtime for repairs.
- For purchasers, this means factoring in ongoing maintenance costs and potential production interruptions when considering three-plate molds.
In summary, while three-plate molds offer unique advantages for certain applications, their higher manufacturing and machining costs, increased weight, longer lead times, and potential maintenance challenges make them less suitable for simpler or budget-constrained projects. Purchasers should carefully weigh these disadvantages against the specific needs of their production processes to determine if a three-plate mold is the right choice.
Summary Table:
Disadvantage | Impact |
---|---|
Higher Manufacturing Costs | Increased upfront investment due to complex design and engineering. |
Increased Machining Costs | Labor-intensive and time-consuming machining raises overall costs. |
Heavier Mold Weight | Complicates handling, transportation, and installation; limits compatibility. |
Longer Lead Times | Delays production schedules, affecting time-sensitive projects. |
Limited Cost-Effectiveness | Not economical for simpler projects; two-plate molds may suffice. |
Potential for Increased Maintenance | Additional components lead to higher wear and tear, increasing downtime. |
Need help deciding if a three-plate mold is right for your project? Contact our experts today for tailored advice!