Wiped film molecular stills, while offering significant advantages such as improved heat transfer, material transport, and separation efficiency, also come with notable disadvantages. These include high costs due to the complexity of the technology and the need for high vacuum systems and precise material sealing. Additionally, the process can result in the loss of the natural triglyceride form, and achieving high-quality distillate often requires multiple passes through the system, which increases processing time. The equipment is also challenging to process, requiring careful design of evaporation and condensation surfaces.
Key Points Explained:
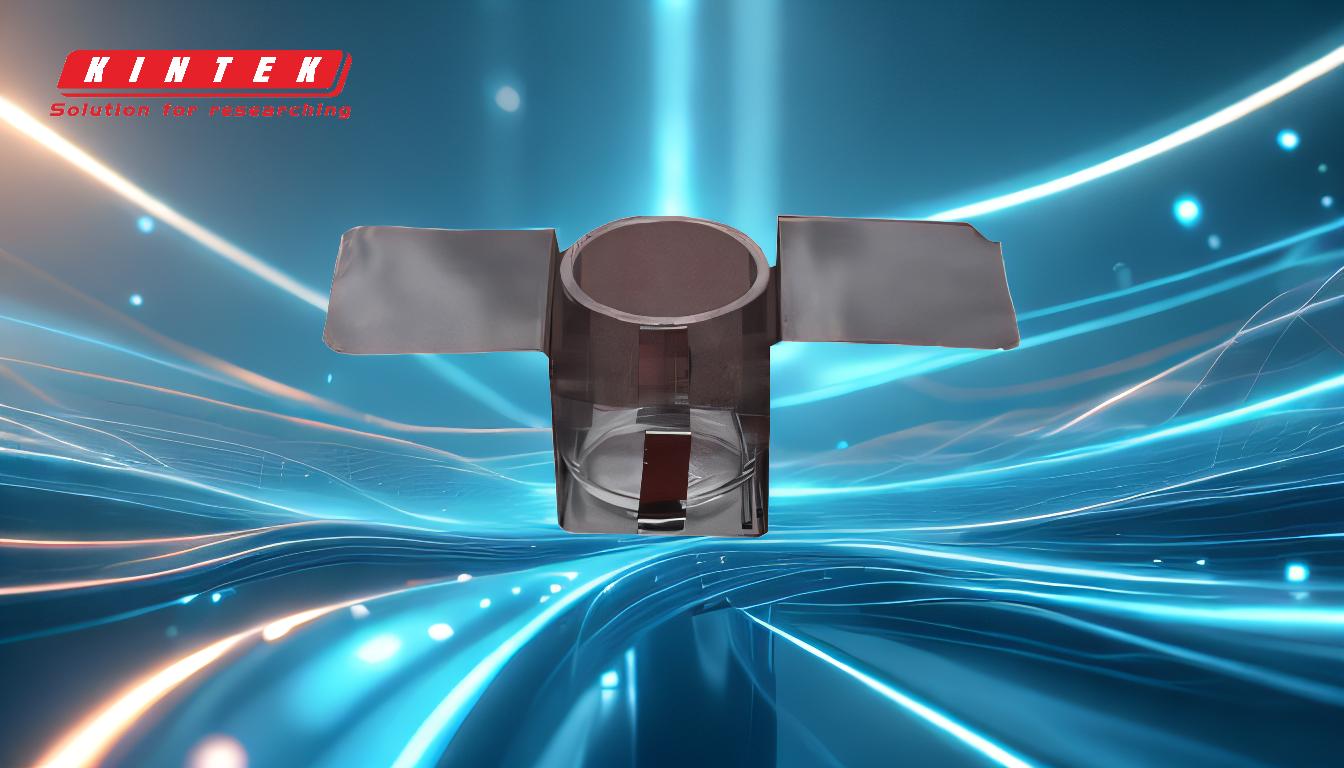
-
High Cost:
- Complex Technology: The wiped film molecular still involves sophisticated technology, which drives up the initial investment and maintenance costs.
- High Vacuum Systems: The need for high vacuum systems adds to the expense. These systems are essential for maintaining the low pressure required for effective distillation but are costly to install and maintain.
- Precise Material Sealing: Ensuring a proper seal to maintain the vacuum adds another layer of complexity and cost.
-
Loss of Natural Form:
- Natural Triglyceride Form: During the distillation process, the natural triglyceride form of the starting material is often lost. This can be a significant drawback for industries where maintaining the natural form of the product is crucial.
-
Multiple Passes Required:
- Two-Pass System: Achieving a high-quality distillate often requires two passes through the system. The first pass removes the bulk of the impurities, while the second pass is necessary to eliminate leftover terpenes and volatiles.
- Increased Processing Time: The need for multiple passes increases the overall processing time, which can be a disadvantage in time-sensitive production environments.
-
Equipment Processing Challenges:
- Design Complexity: The evaporation and condensation surfaces must be meticulously designed to ensure effective distillation. This adds to the complexity and cost of the equipment.
- Maintenance of High Vacuum Degree: Maintaining a high vacuum degree is crucial for the process but adds to the operational complexity and cost.
-
Operational Complexity:
- Controlled Scraper Rotation: The system relies on controlled scraper rotation to drive the material downward around the distillation wall, creating a high degree of film mixing. This requires precise control and adds to the operational complexity.
- Material Residence Time and Film Thickness: Managing short and controlled material residence times and film thickness is essential for effective distillation but requires sophisticated control systems.
In summary, while wiped film molecular stills offer significant advantages in terms of efficiency and product quality, they come with high costs, operational complexities, and the potential loss of the natural form of the starting material. These factors must be carefully considered when deciding whether this technology is appropriate for a given application.
Summary Table:
Disadvantage | Details |
---|---|
High Cost | Complex technology, high vacuum systems, and precise material sealing. |
Loss of Natural Form | Natural triglyceride form is often lost during distillation. |
Multiple Passes Required | Two-pass system increases processing time. |
Equipment Challenges | Complex design of evaporation/condensation surfaces and high vacuum maintenance. |
Operational Complexity | Controlled scraper rotation, material residence time, and film thickness management. |
Considering wiped film molecular stills for your application? Contact us today to discuss your needs and explore the best solutions!