Sintering temperature plays a critical role in determining the final properties of a material, including its microstructure, density, porosity, strength, and hardness. Higher sintering temperatures generally lead to reduced porosity and increased density, but excessive temperatures can cause defects and degrade material properties. Conversely, low sintering temperatures may result in insufficient bonding and poor mechanical properties. The sintering atmosphere and time also influence the final product, with factors like grain growth, recrystallization, and phase formation being directly affected by these parameters. Optimal sintering conditions are essential to achieve the desired balance of material properties.
Key Points Explained:
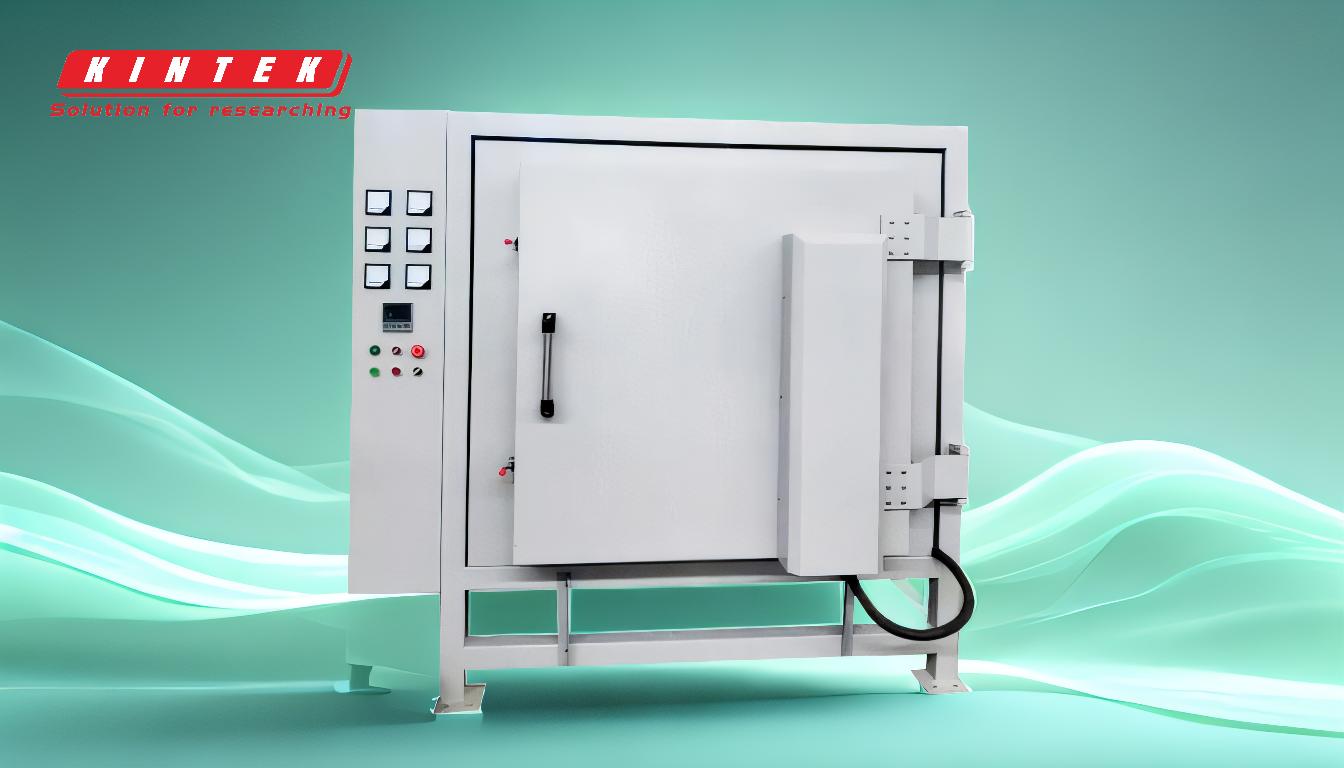
-
Microstructural Changes:
- Grain Size: Higher sintering temperatures promote grain growth, which can lead to larger grain sizes. This can improve strength but may reduce toughness.
- Pore Size and Distribution: Sintering at higher temperatures reduces porosity by closing pores, leading to a denser material. However, excessive temperatures can cause pore coarsening or defects.
- Grain Boundary Shape: Sintering affects the shape and distribution of grain boundaries, influencing material properties like ductility and fracture resistance.
-
Material Properties:
- Density: Higher sintering temperatures increase density by reducing porosity, but over-sintering can lead to undesirable grain growth or defects.
- Strength and Hardness: Optimal sintering temperatures enhance strength and hardness by improving particle bonding and reducing porosity. However, excessive temperatures can weaken the material due to grain coarsening.
- Porosity: Lower sintering temperatures result in higher porosity, which can degrade mechanical properties like strength and durability.
-
Defects and Degradation:
- High Temperatures: Prolonged sintering at high temperatures can cause defects such as cracking, warping, or the formation of ancillary phases, which degrade material properties.
- Low Temperatures: Insufficient sintering temperatures may result in incomplete bonding, poor mechanical properties, and higher porosity.
-
Sintering Atmosphere:
- Reducing Atmosphere: Sintering in a reducing atmosphere prevents oxidation and allows for the reduction of surface oxides, improving material properties.
- Oxidizing Atmosphere: Sintering in an oxidizing atmosphere can lead to the formation of oxides, which may degrade the material's properties.
-
Phase Formation:
- Ancillary Phases: The combination of sintering temperature, time, and atmosphere can influence the formation of secondary or ancillary phases, which may negatively impact material performance.
- Recrystallization and Grain Growth: Sintering temperature affects recrystallization and grain growth, which are critical for achieving the desired microstructure and properties.
-
Physical and Chemical Changes:
- Removal of Volatiles: During sintering, water, organic matter, and adsorbed gases are removed, which can affect the final density and porosity.
- Stress Relief: Sintering helps relieve internal stresses, improving material stability and performance.
- Material Migration: Sintering facilitates material migration, leading to better particle bonding and densification.
-
Optimal Sintering Conditions:
- Finding the right balance of sintering temperature, time, and atmosphere is crucial for achieving the desired material properties. This requires careful control and optimization of processing parameters.
In summary, sintering temperature significantly impacts the microstructure and properties of materials. Optimal sintering conditions must be carefully selected to balance density, porosity, strength, and other material properties, while avoiding defects and degradation.
Summary Table:
Aspect | Impact of High Temperature | Impact of Low Temperature |
---|---|---|
Density | Increases density, reduces porosity | Higher porosity, lower density |
Strength & Hardness | Improves bonding, increases strength | Poor bonding, reduced strength |
Porosity | Reduces porosity, may cause defects if excessive | Higher porosity, weaker material |
Grain Size | Promotes grain growth, may reduce toughness | Smaller grains, incomplete bonding |
Defects | Risk of cracking, warping, or phase formation | Incomplete bonding, poor mechanical properties |
Atmosphere | Reducing atmosphere improves properties | Oxidizing atmosphere may degrade properties |
Need help optimizing your sintering process? Contact our experts today for tailored solutions!