Magnetron sputtering is a versatile and widely used thin-film deposition technique with significant effects on material properties and applications across various industries. It enhances material durability, performance, and functional characteristics such as corrosion resistance, wear resistance, and optical or electrical properties. The process is highly efficient due to the concentration of plasma near the target surface, which increases ion bombardment and sputtering rates without raising operating pressure. This makes it suitable for depositing uniform and high-quality thin films for applications ranging from microelectronics and optics to solar cells and wear-resistant coatings. Additionally, magnetron sputtering enables the fabrication of advanced materials like high-mobility thin-film transistors (TFTs) and functional films with specialized optical or electrical properties.
Key Points Explained:
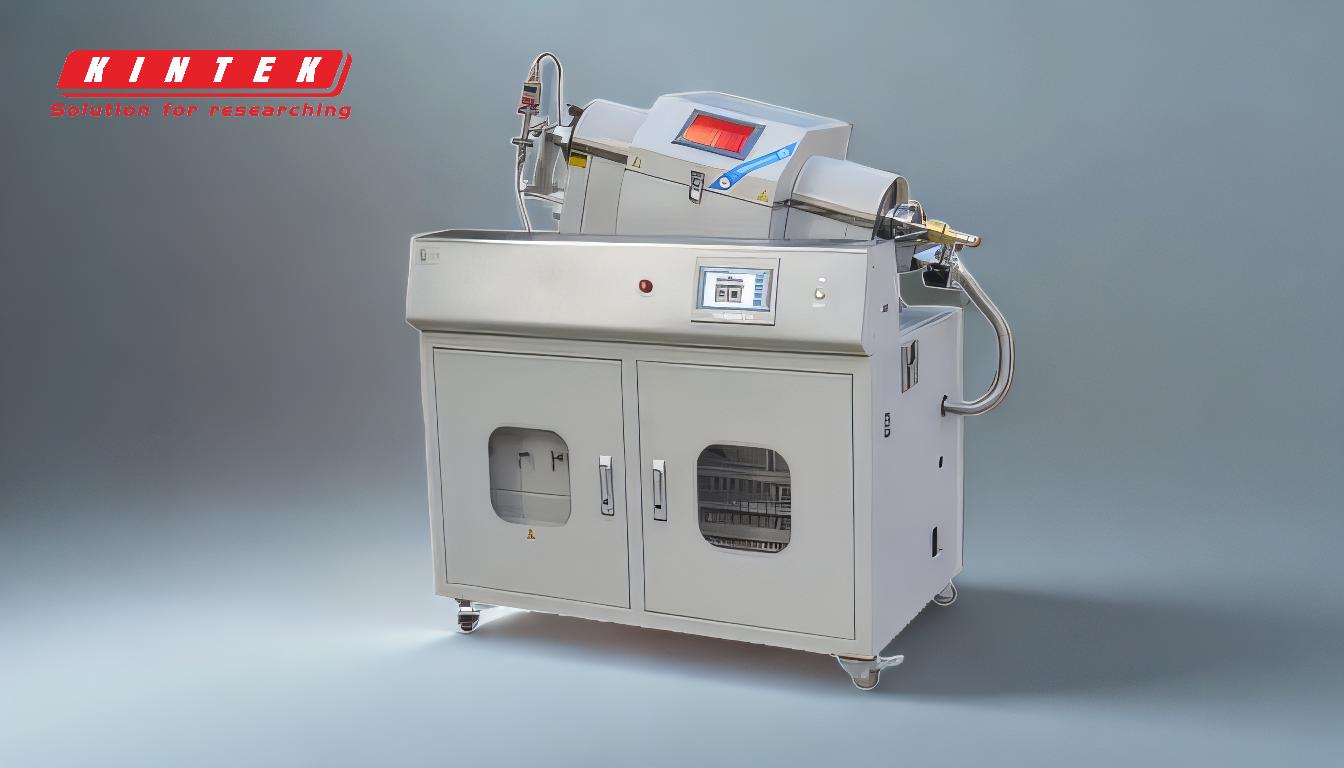
-
Enhanced Material Properties
- Magnetron sputtering improves material properties by depositing high-energy atoms in uniform and tight patterns.
- This results in enhanced durability, performance, and functional characteristics such as:
- Corrosion resistance
- Wear resistance
- Specific optical or electrical properties
-
High Efficiency and Precision
- The use of magnetic fields in magnetron sputtering concentrates plasma near the target surface, increasing ion bombardment and sputtering rates.
- This allows for efficient deposition without the need to raise operating pressure, making the process more effective for both DC and RF discharges.
-
Applications in Microelectronics
- Magnetron sputtering is widely used in the semiconductor industry for depositing thin films in integrated circuit processing.
- It has been instrumental in the production of computer hard disks and the fabrication of thin-film transistors (TFTs) using materials like amorphous indium gallium zinc oxide (a-IGZO) and zinc oxide.
- These TFTs exhibit high optical transparency, field-effect mobility, and can be fabricated at low temperatures on flexible substrates.
-
Functional Films for Optics and Energy
- Magnetron sputtering is used to create functional films with special optical properties, such as absorption, transmission, reflection, refraction, and polarization.
- Applications include:
- Translucent films and low-radiation glass in optical fields
- Thin-film solar cells and anti-reflective layers on displays
- Barrier layers for OLEDs and solar cells
- Solar control coatings on glass
-
Surface Functionalization in Machining
- In the machining industry, magnetron sputtering is used to deposit surface functional films, super hard films, and self-lubricating films.
- These coatings enhance wear resistance and reduce friction, improving the performance and lifespan of machine parts.
-
Research and Advanced Materials
- Magnetron sputtering plays a significant role in research areas such as:
- High-temperature superconducting thin films
- Ferroelectric thin films
- Giant magnetoresistive thin films
- Thin-film light-emitting materials
- Memory alloy thin films
- These materials are critical for developing advanced technologies in electronics, energy, and materials science.
- Magnetron sputtering plays a significant role in research areas such as:
-
Industrial Adoption and Cost-Effectiveness
- DC magnetron sputtering is simpler and generally less expensive than RF magnetron sputtering, making it more attractive for industrial applications.
- Advances in electrical components and fast control of power supplies have further enhanced its adoption in various industries.
In summary, magnetron sputtering is a highly effective and versatile technique that significantly impacts material properties and enables a wide range of applications in microelectronics, optics, energy, and machining. Its ability to deposit uniform, high-quality thin films with specialized properties makes it indispensable in both industrial and research settings.
Summary Table:
Key Effects of Magnetron Sputtering | Applications |
---|---|
Enhanced durability, corrosion resistance, and wear resistance | Microelectronics, machining, and wear-resistant coatings |
High-efficiency deposition with precise control | Thin-film transistors (TFTs), solar cells, and optical films |
Specialized optical and electrical properties | Translucent films, anti-reflective layers, and barrier layers |
Advanced materials for research and industry | High-temperature superconductors, ferroelectric films, and memory alloys |
Cost-effective industrial adoption | DC magnetron sputtering for large-scale applications |
Learn how magnetron sputtering can transform your materials and applications—contact our experts today!