Pyrolysis is a thermal decomposition process that converts organic materials into valuable products like biochar, bio-oil, and syngas, while also generating emissions that can impact the environment. The emissions from pyrolysis include gases such as carbon monoxide (CO), carbon dioxide (CO₂), methane (CH₄), hydrogen (H₂), and volatile organic compounds (VOCs), as well as particulate matter and ash. These emissions vary depending on the feedstock, pyrolysis conditions, and technology used. While pyrolysis offers significant environmental benefits, such as reducing greenhouse gas emissions and producing renewable energy, it also poses challenges, including potential air pollution and the need for sustainable feedstock sourcing. Proper management and optimization of the process are essential to maximize its environmental benefits and minimize negative impacts.
Key Points Explained:
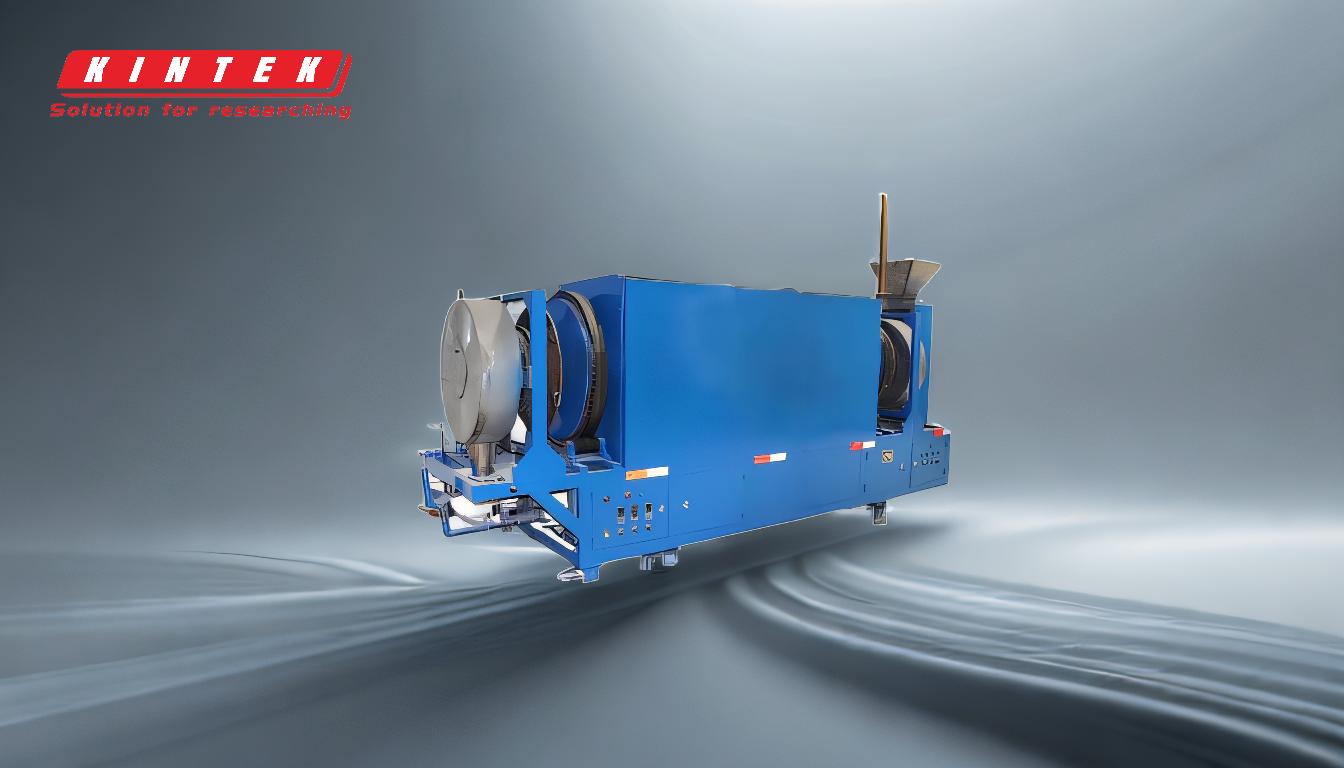
-
Types of Emissions from Pyrolysis:
- Gaseous Emissions: Pyrolysis releases gases such as carbon monoxide (CO), carbon dioxide (CO₂), methane (CH₄), hydrogen (H₂), and volatile organic compounds (VOCs). These gases can contribute to air pollution and climate change if not properly managed.
- Particulate Matter and Ash: The process also produces particulate matter and ash, which can contain harmful substances and require proper disposal to avoid environmental contamination.
-
Environmental Benefits of Pyrolysis:
- Greenhouse Gas Reduction: Pyrolysis helps reduce greenhouse gas emissions by converting organic waste into biofuels, which generally have a lower carbon footprint compared to traditional fossil fuels. It can offset up to 4 tonnes of CO₂ equivalent per tonne of waste.
- Renewable Energy Production: The process generates renewable energy in the form of bio-oil, syngas, and biochar, which can replace fossil fuels and contribute to a bio-based economy.
- Carbon Sequestration: Biochar produced during pyrolysis can be used to improve soil fertility and sequester carbon, further reducing atmospheric CO₂ levels.
-
Challenges and Negative Impacts:
- Air Pollution: The release of gases like CO, CO₂, and VOCs can contribute to air pollution if not controlled. Proper filtration and emission control systems are necessary to mitigate these effects.
- Feedstock Sourcing: Unsustainable sourcing of biomass can lead to deforestation and other environmental issues. It is crucial to use sustainable feedstocks to avoid negative impacts on ecosystems.
- Process Optimization: The environmental impact of pyrolysis can vary significantly depending on the process conditions, such as temperature, heating rate, and feedstock type. Optimizing these parameters is essential to minimize emissions and maximize product yield.
-
Applications and Complementary Technologies:
- Value-Added Products: Pyrolysis produces biochar, bio-oil, and syngas, which have various applications, including soil amendment, renewable fuel, and industrial feedstock.
- Integration with Other Processes: Pyrolysis can be integrated with other technologies, such as anaerobic digestion, to enhance overall efficiency and environmental benefits. For example, syngas can be used to heat anaerobic digestion plants, reducing the need for external energy sources.
-
Historical and Regional Context:
- Historical Deforestation: Historically, wood pyrolysis contributed to deforestation in regions like north-western Europe and Britain. Similar effects are observed today in parts of Africa and Asia, highlighting the importance of sustainable feedstock sourcing.
- Modern Practices: Modern pyrolysis technologies aim to mitigate historical issues by using waste materials and residues, thereby reducing the need for fresh biomass and minimizing environmental impact.
-
Regulatory and Management Considerations:
- Emission Control: Regulations and standards are essential to control emissions from pyrolysis plants. Technologies such as scrubbers, filters, and catalytic converters can help reduce the release of harmful gases and particulate matter.
- Waste Management: Proper disposal and utilization of ash and other by-products are crucial to prevent soil and water contamination. Ash can be used in construction materials or as a soil amendment, provided it is free from harmful contaminants.
In conclusion, pyrolysis is a promising technology with significant environmental benefits, particularly in reducing greenhouse gas emissions and producing renewable energy. However, it also poses challenges related to emissions, feedstock sourcing, and process optimization. By addressing these challenges through sustainable practices, advanced technologies, and regulatory oversight, the negative impacts of pyrolysis can be minimized, and its benefits can be fully realized.
Summary Table:
Aspect | Details |
---|---|
Types of Emissions | Gases (CO, CO₂, CH₄, H₂, VOCs), particulate matter, and ash. |
Environmental Benefits | Reduces greenhouse gases, produces renewable energy, and sequesters carbon. |
Challenges | Air pollution, sustainable feedstock sourcing, and process optimization. |
Applications | Biochar for soil, bio-oil for fuel, and syngas for industrial use. |
Regulatory Needs | Emission control systems and sustainable waste management practices. |
Discover how pyrolysis can benefit your operations—contact our experts today!