Wood pyrolysis is a thermal decomposition process that occurs in the absence of oxygen, converting wood into charcoal, gases, and tars. The emissions from wood pyrolysis primarily include gases like Carbon Monoxide (CO) and Carbon Dioxide (CO₂), along with other byproducts such as bio-oil and biochar. While the process has environmental benefits, such as reducing greenhouse gas emissions and producing renewable energy, it also poses challenges, including the release of harmful gases and the potential for deforestation if biomass is sourced unsustainably. The efficiency and environmental performance of wood pyrolysis depend on factors like temperature, feedstock quality, and process control.
Key Points Explained:
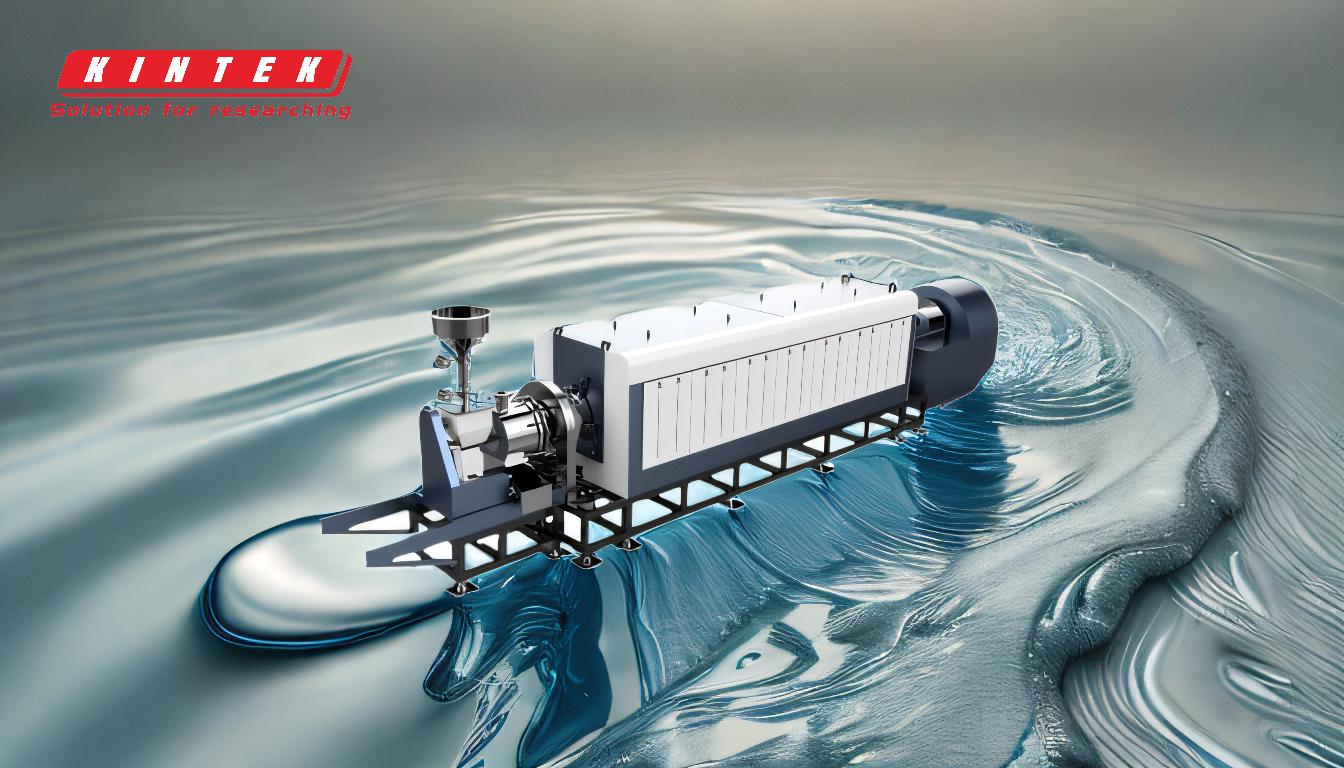
-
Primary Emissions from Wood Pyrolysis:
- Carbon Monoxide (CO) and Carbon Dioxide (CO₂): These are the main gases released during wood pyrolysis. CO is a toxic gas, while CO₂ is a greenhouse gas contributing to climate change.
- Tars and Bio-oil: These liquid byproducts can be used as fuels or in industrial applications, but they may also release volatile organic compounds (VOCs) if not properly managed.
- Charcoal (Biochar): A solid residue that can sequester carbon and improve soil fertility, but its production must be carefully controlled to avoid environmental harm.
-
Environmental Benefits:
- Greenhouse Gas Reduction: Pyrolysis offsets up to 4 tonnes of CO₂ equivalent per tonne of waste by preventing the release of CO₂ and methane (CH₄) from decomposition.
- Renewable Energy Production: The process converts agricultural residues, wood waste, and municipal solid waste into clean energy, reducing reliance on fossil fuels.
- Biochar Sequestration: Biochar can store carbon in the soil for centuries, contributing to carbon sequestration and improving soil health.
-
Environmental Challenges:
- Harmful Emissions: The release of CO, CO₂, and VOCs can harm air quality if not properly managed.
- Deforestation Risks: Unsustainable sourcing of biomass, such as wood from deforestation, can exacerbate environmental degradation.
- Process Emissions: The need for back-up fuel and the potential release of pollutants during pyrolysis can offset some of its environmental benefits.
-
Process Efficiency and Control:
- Temperature and Oxygen Control: Pyrolysis occurs at temperatures above 270 °C (518 °F) in the absence of oxygen. If oxygen is present, combustion occurs, producing wood ash instead of charcoal.
- Feedstock Quality: The type and quality of biomass used (e.g., agricultural residues, wood waste) significantly impact the efficiency and environmental performance of pyrolysis.
- Technological Integration: Pyrolysis can complement other processes, such as anaerobic digestion and plastic transformation, enhancing its overall sustainability.
-
Global Carbon Market and Sustainability:
- Carbon Credits: Biochar production can generate carbon credits, making pyrolysis economically viable and environmentally beneficial.
- Sustainable Practices: Ensuring sustainable biomass sourcing and proper management of emissions is critical to maximizing the environmental benefits of pyrolysis.
In summary, wood pyrolysis is a complex process with both environmental benefits and challenges. While it offers significant potential for reducing greenhouse gas emissions and producing renewable energy, careful management is required to mitigate harmful emissions and ensure sustainable biomass sourcing. The process's efficiency and environmental performance depend on factors such as temperature control, feedstock quality, and integration with other technologies.
Summary Table:
Aspect | Details |
---|---|
Primary Emissions | CO, CO₂, tars, bio-oil, and biochar |
Environmental Benefits | Greenhouse gas reduction, renewable energy, biochar sequestration |
Challenges | Harmful emissions, deforestation risks, process emissions |
Efficiency Factors | Temperature control, feedstock quality, technological integration |
Sustainability | Carbon credits, sustainable biomass sourcing, emission management |
Learn more about optimizing wood pyrolysis for sustainability—contact our experts today!