Pellet quality is a critical factor in many industries, particularly in biomass and feed production. The quality of raw materials plays a significant role in determining the final pellet quality, and several factors must be considered to optimize the pelletizing process. These factors include the shape, size, and moisture content of the raw materials, which directly influence the pellet mill's performance and the overall pelletizing plan. Understanding these factors helps in producing high-quality pellets that meet specific standards and requirements.
Key Points Explained:
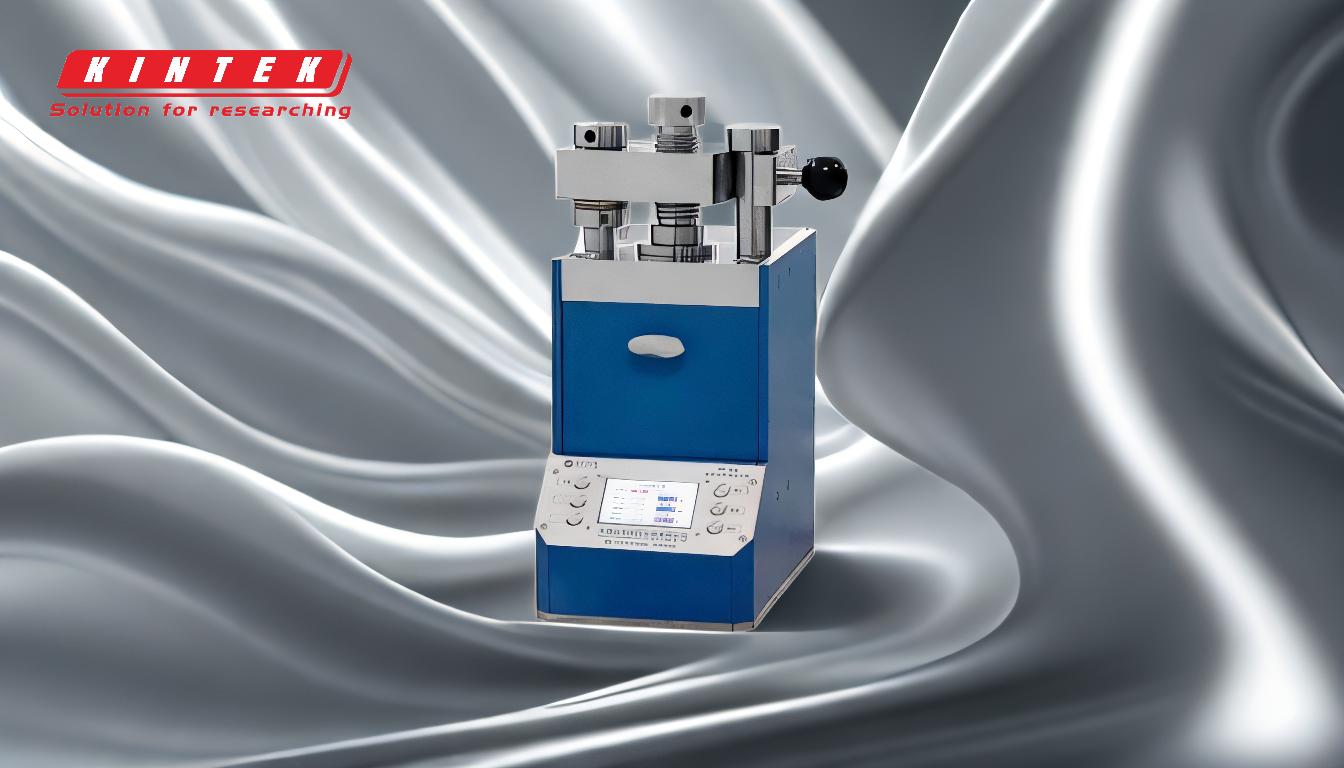
-
Quality of Raw Materials:
- The quality of raw materials is the foundation of pellet production. High-quality raw materials lead to better pellet quality, while poor-quality materials can result in substandard pellets.
- Raw materials should be free from contaminants and have consistent properties to ensure uniform pellet production.
-
Shape of Raw Materials:
- The shape of the raw materials affects how they compress and bind together during the pelletizing process.
- Irregular shapes can lead to uneven compression, resulting in weak or brittle pellets. Uniform shapes, on the other hand, promote better binding and stronger pellets.
-
Size of Raw Materials:
- The size of the raw materials is crucial for the pellet mill's performance. Materials that are too large may not compress properly, while materials that are too small may not bind effectively.
- Optimal size distribution ensures that the materials compress uniformly, leading to consistent pellet quality.
-
Moisture Content:
- Moisture content is a critical factor in pellet production. Too much moisture can cause the pellets to be too soft or even disintegrate, while too little moisture can make the materials difficult to compress.
- The ideal moisture level depends on the type of raw material and the specific pellet mill being used. Proper moisture control is essential for producing durable and high-quality pellets.
-
Pelletizing Plan:
- The pelletizing plan must take into account the properties of the raw materials to optimize the pellet mill's performance.
- Adjustments may need to be made to the pellet mill settings, such as die size, compression ratio, and feed rate, to accommodate different raw material properties and achieve the desired pellet quality.
-
Impact on Pellet Mill Performance:
- The quality of raw materials directly impacts the pellet mill's efficiency and output. Poor-quality materials can lead to increased wear and tear on the mill, higher energy consumption, and reduced production rates.
- High-quality materials, on the other hand, can improve the mill's performance, leading to higher production rates and longer equipment lifespan.
-
Final Pellet Quality:
- The ultimate goal is to produce pellets that meet specific quality standards, such as density, durability, and moisture resistance.
- By carefully controlling the factors that affect pellet quality, producers can ensure that their pellets are suitable for their intended use, whether it be for fuel, feed, or other applications.
In conclusion, the quality of raw materials, including their shape, size, and moisture content, plays a crucial role in determining the quality of pellets produced. By understanding and controlling these factors, producers can optimize their pelletizing plan and improve the performance of their pellet mill, ultimately leading to higher-quality pellets.
Summary Table:
Factor | Impact on Pellet Quality |
---|---|
Quality of Raw Materials | High-quality materials ensure better pellet quality; contaminants lead to substandard pellets. |
Shape of Raw Materials | Uniform shapes promote better binding, while irregular shapes cause weak or brittle pellets. |
Size of Raw Materials | Optimal size distribution ensures uniform compression and consistent pellet quality. |
Moisture Content | Proper moisture levels are essential for durable pellets; too much or too little harms quality. |
Pelletizing Plan | Adjust mill settings (die size, compression ratio, feed rate) to optimize pellet quality. |
Pellet Mill Performance | High-quality materials improve efficiency, reduce wear, and increase production rates. |
Final Pellet Quality | Meet standards for density, durability, and moisture resistance for intended applications. |
Ready to optimize your pellet quality? Contact our experts today for tailored solutions!