Hydraulic systems are widely used in various industries due to their efficiency and power transmission capabilities. However, they are prone to failures that can disrupt operations and lead to costly downtime. Common failures in hydraulic systems include issues like fluid contamination, overheating, leaks, component wear, and pressure problems. These failures often stem from poor maintenance, improper operation, or design flaws. Understanding the root causes of these failures and implementing preventive measures can significantly enhance the reliability and longevity of hydraulic systems.
Key Points Explained:
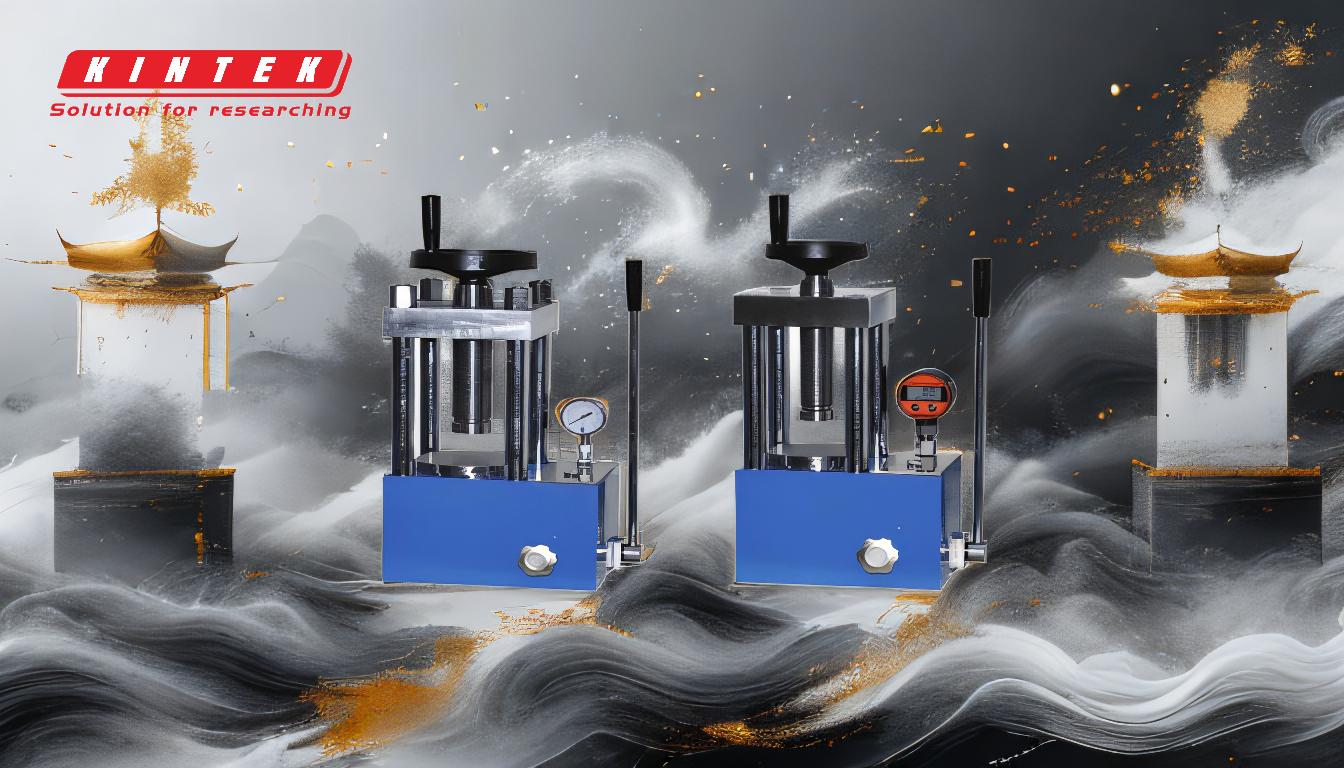
-
Fluid Contamination:
- Causes: Contaminants such as dirt, water, and metal particles can enter the hydraulic fluid through inadequate filtration, poor sealing, or improper handling.
- Effects: Contaminated fluid can cause abrasion, corrosion, and clogging of system components, leading to reduced efficiency and potential failure.
- Prevention: Regular fluid analysis, proper filtration, and maintaining clean working environments can help prevent contamination.
-
Overheating:
- Causes: Overheating can result from excessive load, insufficient cooling, or high ambient temperatures.
- Effects: Elevated temperatures can degrade hydraulic fluid, reduce viscosity, and damage seals and other components, leading to system inefficiency and failure.
- Prevention: Ensuring adequate cooling, monitoring system temperature, and avoiding overloading can mitigate overheating issues.
-
Leaks:
- Causes: Leaks can occur due to worn seals, loose fittings, or damaged hoses and pipes.
- Effects: Fluid leaks lead to loss of hydraulic pressure, reduced system performance, and potential environmental hazards.
- Prevention: Regular inspection of seals and fittings, proper installation, and timely replacement of worn components can prevent leaks.
-
Component Wear:
- Causes: Wear and tear of components like pumps, valves, and actuators can result from prolonged use, inadequate lubrication, or contamination.
- Effects: Worn components can lead to reduced efficiency, increased noise, and eventual system failure.
- Prevention: Regular maintenance, proper lubrication, and using high-quality components can extend the life of hydraulic system parts.
-
Pressure Problems:
- Causes: Incorrect pressure settings, faulty pressure relief valves, or blockages in the system can cause pressure issues.
- Effects: Abnormal pressure levels can lead to component damage, system inefficiency, and safety hazards.
- Prevention: Regular calibration of pressure settings, inspection of pressure relief valves, and ensuring clear fluid pathways can maintain optimal pressure levels.
By addressing these common failures through proactive maintenance and proper operation, the reliability and performance of hydraulic systems can be significantly improved, reducing downtime and operational costs.
Summary Table:
Failure Type | Causes | Effects | Prevention |
---|---|---|---|
Fluid Contamination | Dirt, water, metal particles entering fluid | Abrasion, corrosion, clogging, reduced efficiency | Regular fluid analysis, proper filtration, clean environments |
Overheating | Excessive load, insufficient cooling, high ambient temperatures | Fluid degradation, reduced viscosity, seal damage | Adequate cooling, temperature monitoring, avoid overloading |
Leaks | Worn seals, loose fittings, damaged hoses/pipes | Loss of pressure, reduced performance, environmental hazards | Regular inspection, proper installation, timely replacement |
Component Wear | Prolonged use, inadequate lubrication, contamination | Reduced efficiency, increased noise, system failure | Regular maintenance, proper lubrication, high-quality components |
Pressure Problems | Incorrect settings, faulty valves, blockages | Component damage, inefficiency, safety hazards | Regular calibration, valve inspection, clear fluid pathways |
Ensure your hydraulic systems run smoothly—contact our experts today for tailored solutions!