Induction heating is a versatile and efficient method used across various industries for applications such as heat treatment, metal joining, melting, and surface hardening. It offers precise temperature control, contactless heating, and automation, making it ideal for processes requiring high consistency and repeatability. Key applications include hardening steel parts, soldering/brazing, annealing, and melting refractory metals. It also plays a significant role in semiconductor manufacturing, crystal growth, and medical applications. With ongoing technological advancements, induction heating is expected to expand further into emerging fields like alternative energy and engineered materials.
Key Points Explained:
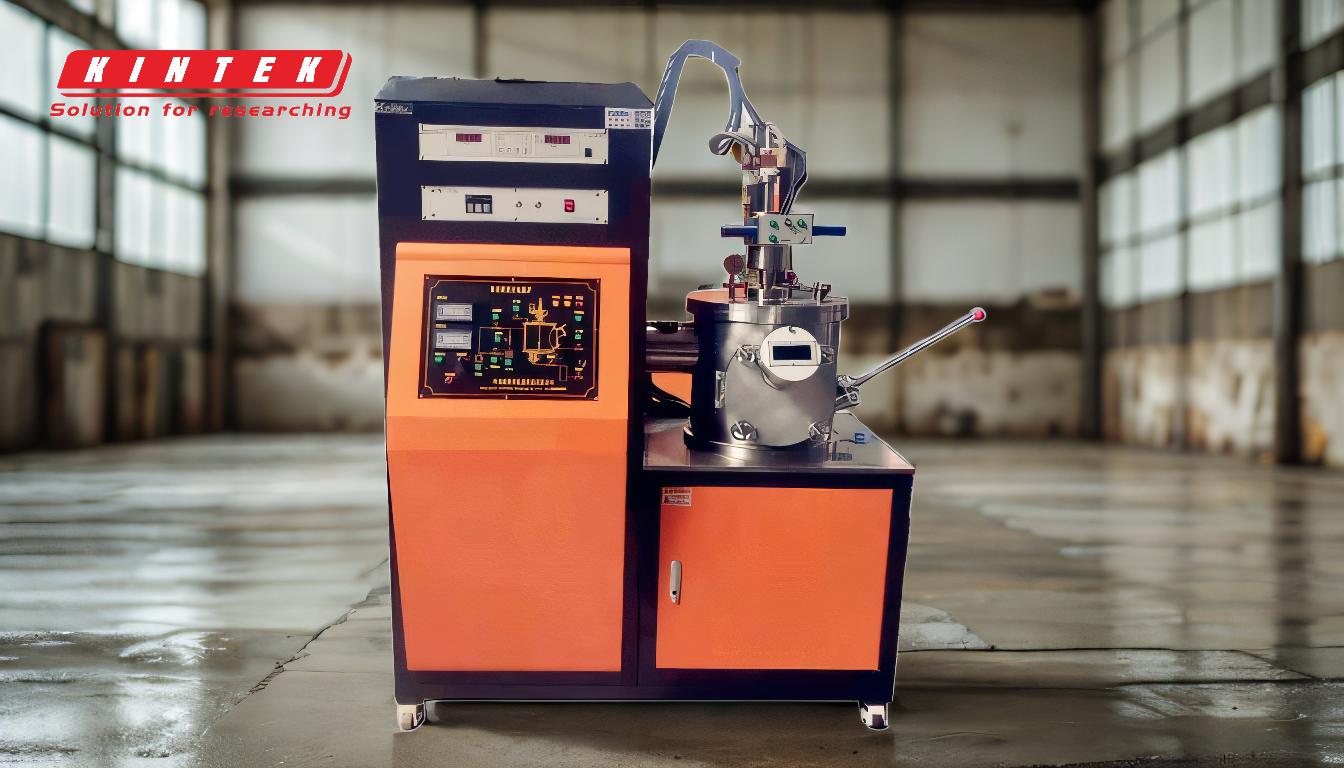
-
Heat Treatment in Metallurgy
- Induction heating is widely used for heat treatment processes such as hardening, annealing, and tempering of metal parts.
- Induction Hardening: This process involves heating the surface of steel parts using an alternating magnetic field and then quenching them to achieve high surface hardness while keeping the core unaffected. Case hardnesses of 37/58 Rc are achievable, making it ideal for components like gears and shafts.
- Induction Annealing: Used to selectively soften specific areas of a metal part, improving ductility and reducing internal stresses.
- Induction Tempering: Helps in achieving desired mechanical properties by controlling the heating and cooling cycles.
-
Metal Joining Processes
- Induction Soldering/Brazing: This method is used to join metal components by heating them to a specific temperature where a filler material melts and forms a strong bond. It is commonly used in the automotive and electronics industries for its precision and efficiency.
- Welding: Induction heating is used for welding metals and even plastics doped with ferromagnetic ceramics, providing a clean and controlled joining process.
-
Melting and Refining Metals
- Induction Furnaces: Used to melt metals, including refractory metals like tungsten and molybdenum, which require extremely high temperatures. Induction furnaces are also used in vacuum environments to produce specialized steel and alloys.
- Zone Refining: A critical process in the semiconductor industry for purifying materials like silicon by melting and recrystallizing them in a controlled manner.
-
Semiconductor and Crystal Growth Applications
- Czochralski Crystal Growth: Induction heating is used to grow single crystals of silicon and other materials for semiconductor manufacturing.
- Zone Refining: Used to purify semiconductors by melting and recrystallizing them, ensuring high material purity.
-
Surface Heating and Hardening
- Induction heating is ideal for surface hardening of steel components, where only the surface layer is heated and quenched to achieve high hardness while maintaining a tough core. This is particularly useful for parts subjected to wear and tear, such as gears and bearings.
-
Medical and Biological Applications
- Induction heating is being explored for medical applications, such as heating biological tissues for therapeutic purposes. Its precise and localized heating capabilities make it suitable for minimally invasive treatments.
-
Industrial and Consumer Applications
- Induction Cooktops: A common household application, induction cooktops use electromagnetic fields to heat cookware directly, offering energy efficiency and precise temperature control.
- Plastic Injection Molding: Induction heating improves energy efficiency in plastic injection molding machines by providing targeted and rapid heating.
- Tamper-Resistant Sealing: Used in the pharmaceutical and food industries to seal caps on bottles securely.
-
Advantages of Induction Heating
- Precision and Control: Enables precise temperature control, ensuring consistent results and high-quality end products.
- Contactless Heating: Reduces wear and tear on equipment and minimizes contamination risks.
- Energy Efficiency: Directly heats the target material, reducing energy losses and improving overall efficiency.
- Automation-Friendly: Easily integrated into automated production lines, enhancing productivity and repeatability.
-
Future Applications and Innovations
- Induction heating is expected to play a significant role in the development of advanced materials, alternative energy solutions, and empowering developing countries with efficient heating technologies.
- Ongoing research aims to optimize process parameters for emerging applications, such as heating low-resistivity materials and biological tissues.
-
Specialized Industrial Uses
- Inductive Furnaces: Used for melting metals in specialized environments, such as vacuum furnaces for producing high-purity alloys.
- Brazing Carbide to Shafts: A critical process in tool manufacturing, ensuring strong and durable bonds between carbide tips and steel shafts.
- Heating Liquid and Gaseous Conductors: Used in specific industrial processes requiring controlled heating of conductive fluids or gases.
In conclusion, induction heating is a cornerstone technology in modern industrial processes, offering unparalleled precision, efficiency, and versatility. Its applications span from traditional metallurgy and semiconductor manufacturing to emerging fields like medical treatments and alternative energy. As technology advances, its role in industrial innovation is set to grow even further.
Summary Table:
Application | Key Uses |
---|---|
Heat Treatment | Hardening, annealing, tempering of metal parts |
Metal Joining | Soldering, brazing, welding |
Melting and Refining Metals | Melting refractory metals, zone refining for semiconductors |
Semiconductor Manufacturing | Crystal growth, material purification |
Medical Applications | Therapeutic heating of biological tissues |
Consumer Applications | Induction cooktops, plastic injection molding, tamper-resistant sealing |
Advantages | Precision, contactless heating, energy efficiency, automation-friendly |
Future Innovations | Advanced materials, alternative energy, and medical advancements |
Interested in how induction heating can transform your processes? Contact us today to learn more!