An induction furnace is a highly efficient and versatile heating or melting system that relies on electromagnetic induction to generate heat within the material being processed. Its main components work together to ensure precise temperature control, uniform heating, and reliable operation. The key parts include the inductor (or induction coil), furnace body, power supply, capacitor, and control system. Additionally, modern induction furnaces often incorporate advanced features like automated frequency scanning, constant power control, and comprehensive protection systems to enhance performance and safety. These components are essential for applications ranging from metal melting to heat treatment.
Key Points Explained:
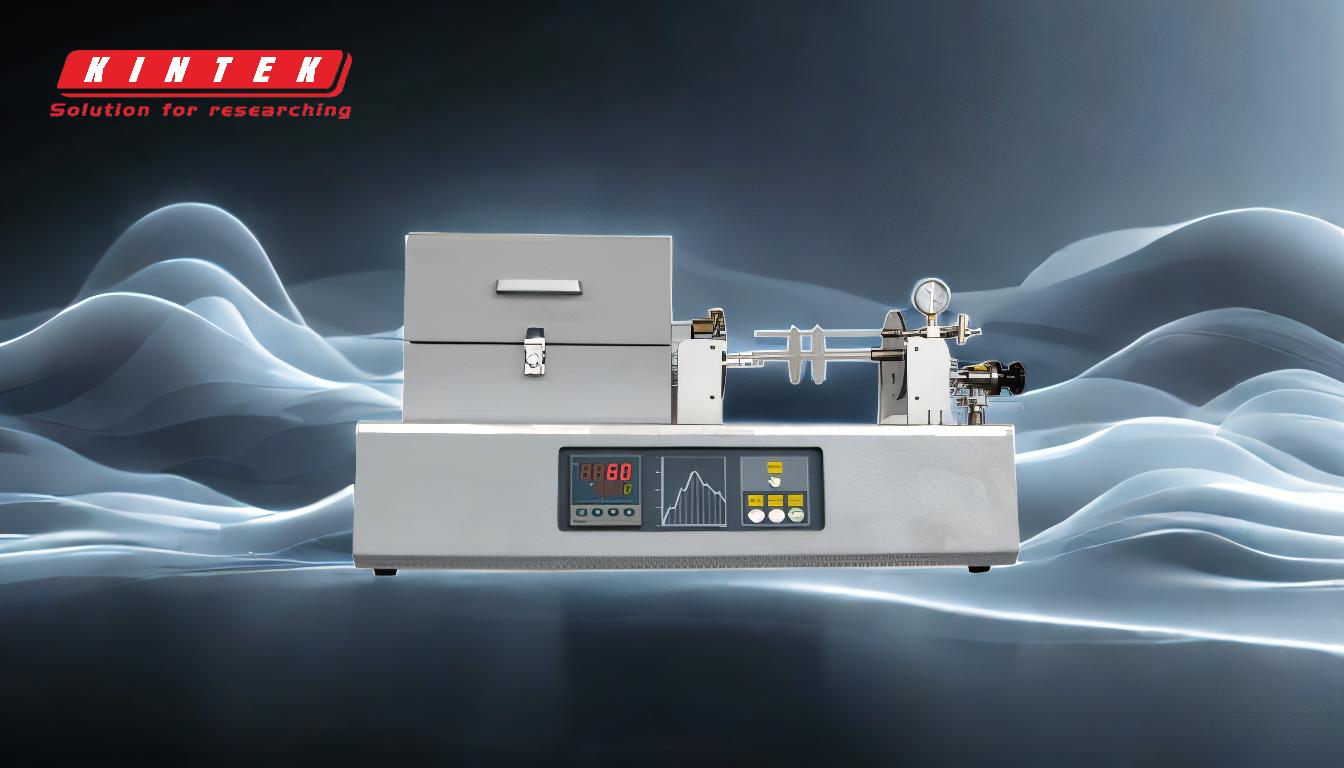
-
Inductor (Induction Coil):
- The inductor is the core component of an induction furnace, responsible for generating the alternating magnetic field that induces eddy currents in the material.
- It is typically made of copper tubing to withstand high temperatures and is often water-cooled to prevent overheating.
- The design of the coil determines the efficiency and uniformity of heating.
-
Furnace Body:
- The furnace body houses the inductor and the material being processed.
- It is constructed with refractory materials to withstand high temperatures and thermal shocks.
- In some designs, the furnace body includes a crucible, which holds the molten material and is also made of refractory materials.
-
Power Supply:
- The power supply provides the necessary electrical energy to the induction coil.
- Modern induction furnaces often use IGBT induction furnace technology, which offers high efficiency, precise control, and reduced energy consumption.
- The power supply unit may include components like transformers, inverters, and capacitor banks to convert and regulate the electrical energy.
-
Capacitor:
- Capacitors are used in the resonant circuit to store and release electrical energy, ensuring efficient power transfer to the induction coil.
- They help maintain the desired frequency and power levels, which are critical for optimal furnace performance.
-
Control System:
- The control system manages the operation of the furnace, including temperature regulation, power output, and safety features.
- Advanced systems may include automatic frequency scanning, constant power control, and protection mechanisms for over-voltage, over-current, and under-voltage conditions.
- The control system ensures smooth and stable operation, even under varying load conditions.
-
Cooling System:
- Induction furnaces generate significant heat, requiring an effective cooling system to protect components like the induction coil and power supply.
- Water cooling is commonly used due to its high heat transfer efficiency.
-
Charging and Fume Extraction Systems:
- A charging arrangement allows for the efficient loading of raw materials into the furnace.
- Fume extraction equipment is essential for removing gases and particulates generated during the melting process, ensuring a safe working environment.
-
Refractory Lining and Crucible:
- The refractory lining protects the furnace body from high temperatures and chemical reactions with molten materials.
- The crucible, often made of high-quality refractory materials, holds the molten metal and must withstand thermal and mechanical stresses.
-
Protection and Safety Features:
- Modern induction furnaces are equipped with comprehensive protection systems to prevent damage from electrical faults, overheating, or other operational issues.
- These features ensure reliable and safe operation, even in demanding industrial environments.
By integrating these components, an induction furnace achieves precise and efficient heating or melting, making it a vital tool in industries such as metallurgy, foundries, and heat treatment. The use of advanced technologies like IGBT induction furnace further enhances performance, making these systems both energy-efficient and highly adaptable to various applications.
Summary Table:
Component | Function |
---|---|
Inductor (Induction Coil) | Generates alternating magnetic field to induce heat in the material. |
Furnace Body | Houses the inductor and material, made of refractory materials for durability. |
Power Supply | Provides electrical energy, often using IGBT technology for efficiency. |
Capacitor | Stores and releases energy to maintain frequency and power levels. |
Control System | Manages temperature, power output, and safety features for stable operation. |
Cooling System | Uses water cooling to protect components from overheating. |
Charging System | Facilitates efficient loading of raw materials into the furnace. |
Fume Extraction | Removes gases and particulates for a safe working environment. |
Refractory Lining | Protects the furnace body from high temperatures and chemical reactions. |
Protection Features | Ensures safe operation with mechanisms for over-voltage and overheating. |
Upgrade your heating process with a high-performance induction furnace—contact us today to learn more!