Liquid phase sintering (LPS) is a widely used process in powder metallurgy and ceramics, where a liquid phase facilitates densification and bonding of solid particles. While it offers advantages like improved densification and the ability to produce complex shapes, it also comes with several drawbacks. These include high costs due to expensive equipment and energy consumption, challenges in achieving uniform properties, and potential defects such as warping or sagging. Additionally, the process may require specialized materials and precise control over parameters, making it complex and less suitable for large-scale production or applications requiring high mechanical strength.
Key Points Explained:
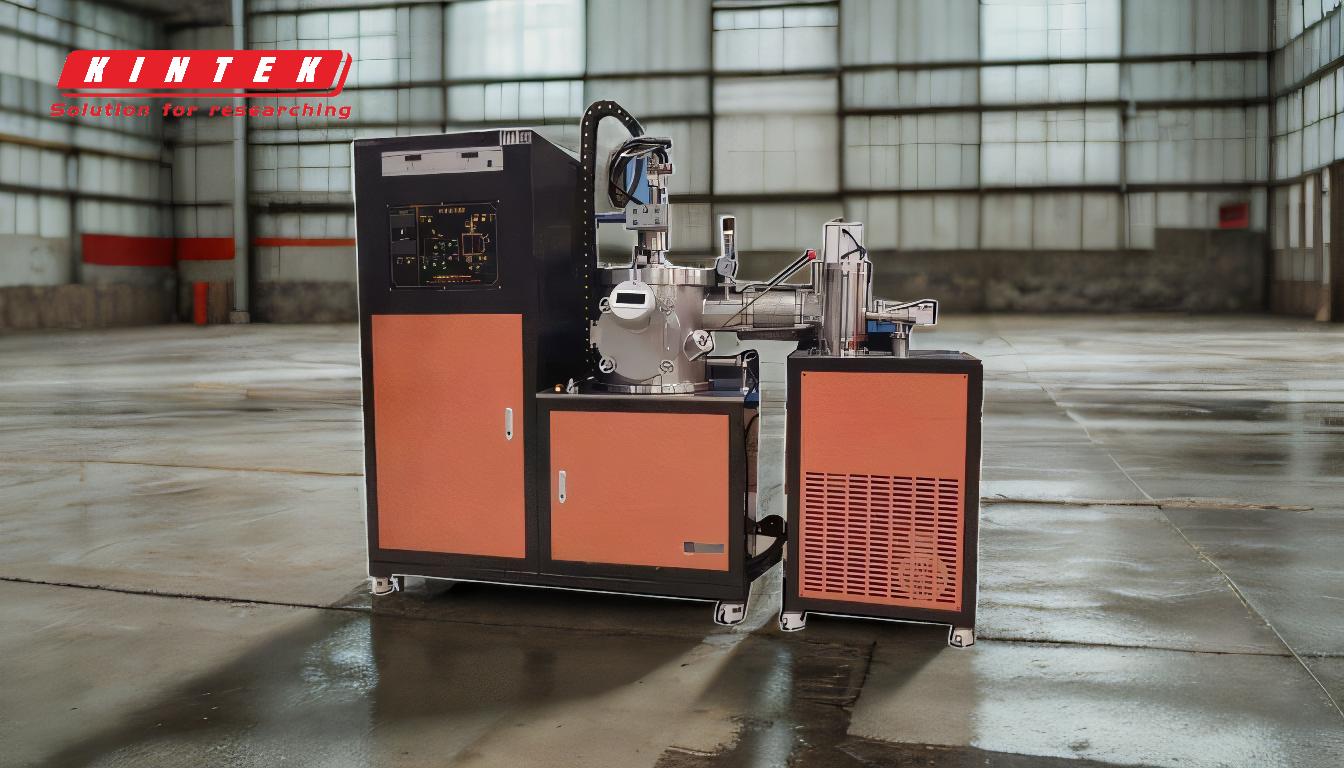
-
High Equipment and Operational Costs
- Liquid phase sintering often requires specialized furnaces capable of maintaining precise temperatures and atmospheres, which are expensive to purchase and maintain.
- The process demands significant energy consumption, particularly for high-temperature sintering, leading to higher operational costs.
- Professional expertise is needed to operate and maintain the equipment, adding to labor costs.
-
Material and Process Limitations
- The process may require specific materials or additives to form the liquid phase, which can increase material costs.
- Achieving uniform distribution of the liquid phase is challenging, potentially leading to inconsistent properties in the final product.
- The process may not be suitable for materials that are sensitive to high temperatures or prone to excessive shrinkage.
-
Potential for Defects
- Warping and sagging are common issues during liquid phase sintering due to gravity or friction, which can lead to dimensional inaccuracies or defects in the final part.
- Excessive shrinkage during sintering can complicate the design and production process, requiring careful compensation during the initial stages.
-
Size and Complexity Constraints
- Liquid phase sintering may face limitations in producing large or complex-shaped parts, similar to other powder metallurgy processes.
- The process may not achieve the same mechanical strength or ductility as traditional casting or forging methods, limiting its use in high-performance applications.
-
Low Productivity and Output
- The sintering process is often time-consuming, with long cycle times that reduce overall productivity.
- Output per furnace is typically small, making it less efficient for large-scale production compared to other manufacturing methods.
-
Technical Complexity
- The process requires precise control over parameters such as temperature, pressure, and atmosphere, making it technically demanding.
- Adjustments may be needed for different materials, adding complexity to the operation and increasing the risk of errors.
In summary, while liquid phase sintering offers unique advantages, its drawbacks—such as high costs, technical complexity, and potential defects—make it less suitable for certain applications. Careful consideration of these factors is essential when choosing this process for manufacturing.
Summary Table:
Drawback | Key Challenges |
---|---|
High Equipment Costs | Expensive specialized furnaces, high energy consumption, and labor costs. |
Material Limitations | Requires specific additives, uneven liquid phase distribution, and material issues. |
Potential Defects | Warping, sagging, and excessive shrinkage during sintering. |
Size & Complexity Limits | Limited ability to produce large or complex parts with high mechanical strength. |
Low Productivity | Time-consuming process with small output per furnace. |
Technical Complexity | Precise control of temperature, pressure, and atmosphere required. |
Need help overcoming the challenges of liquid phase sintering? Contact our experts today for tailored solutions!