Dental ceramics are essential materials in modern dentistry, used for creating durable, aesthetically pleasing dental restorations such as crowns, veneers, and bridges. These materials are primarily composed of inorganic, non-metallic components, often derived from silicate-based minerals. The key materials include clay, kaolin, feldspar, and soapstone, which are processed and fired at high temperatures to achieve the desired mechanical and aesthetic properties. Additionally, advanced ceramics may incorporate alumina and zirconium to enhance strength and durability. The choice of materials depends on factors like the restoration's location, the desired appearance, and the patient's budget.
Key Points Explained:
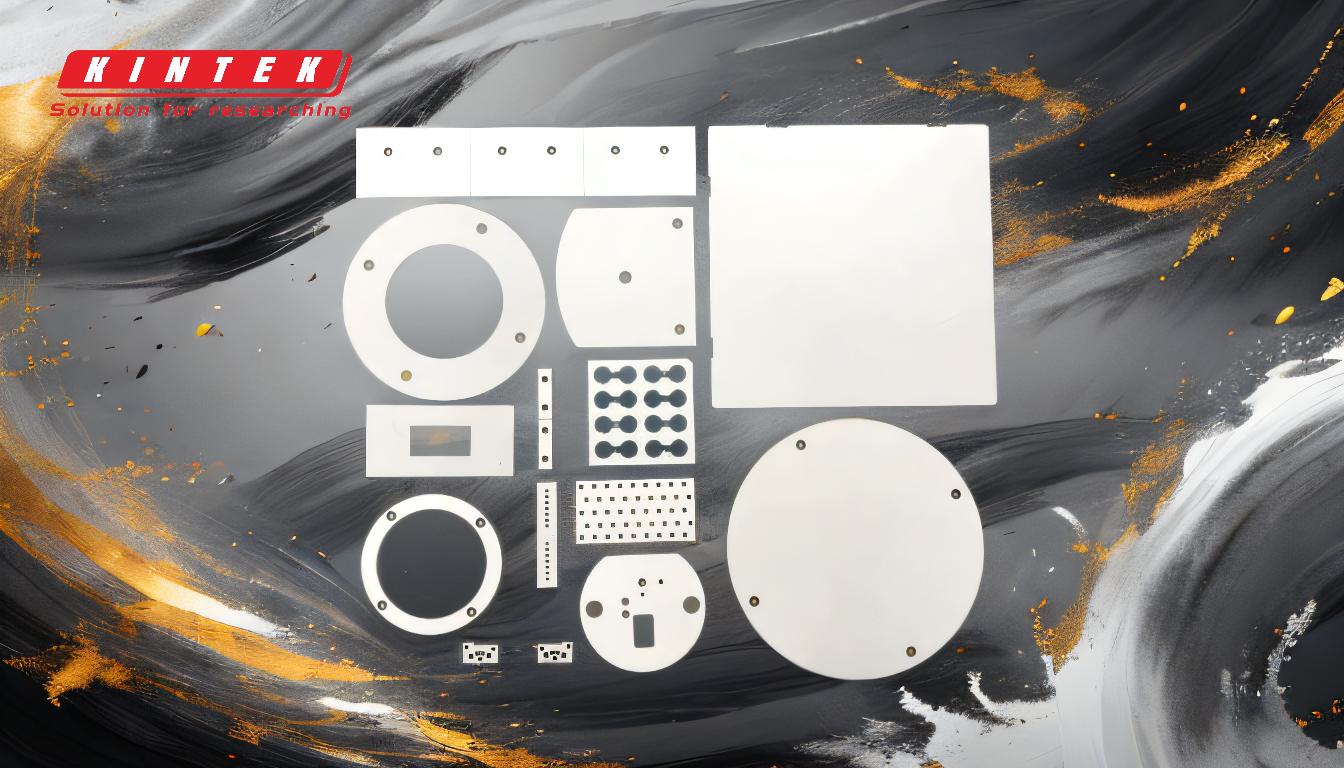
-
Primary Components of Dental Ceramics:
- Clay and Kaolin: These are fundamental materials in dental ceramics, providing the base structure. Clay is typically sourced from soil or salt mines, while kaolin is a refined form of clay that enhances the material's workability and firing properties.
- Feldspar: A silicate mineral that acts as a flux, lowering the melting temperature of the ceramic mixture and promoting vitrification during firing. This results in a glassy, durable finish.
- Soapstone: Another silicate source that contributes to the ceramic's thermal stability and resistance to chemical degradation.
-
Additives for Enhanced Properties:
- Alumina (Aluminum Oxide): Added to improve the mechanical strength and fracture resistance of dental ceramics. It is particularly useful in high-stress areas of the mouth.
- Zirconium (Zirconium Oxide): Known for its exceptional strength and biocompatibility, zirconium is often used in advanced dental ceramics, especially for crowns and bridges. It provides a natural tooth-like appearance and long-term durability.
-
Processing and Firing:
- Dental ceramics are created by mixing the raw materials (clay, minerals, and additives) into a homogenous paste. This mixture is then shaped into the desired form (e.g., crowns, veneers) and fired at high temperatures (typically between 800°C and 1,400°C). The firing process vitrifies the material, creating a hard, glass-like structure with excellent compressive strength.
-
Types of Dental Ceramics:
- Monolithic Ceramics: Single-material ceramics that are pressed or milled into the final restoration shape. These are often used for their simplicity and strength.
- Press-to-Metal Ceramics: Ceramics that are pressed onto a metal substructure, combining the strength of metal with the aesthetics of porcelain.
- Press-to-Zirconia Ceramics: Advanced ceramics pressed onto a zirconia framework, offering superior strength and a natural appearance.
-
Properties and Applications:
- Aesthetic Qualities: Dental ceramics are prized for their ability to mimic the natural translucency and color of teeth, making them ideal for visible restorations.
- Durability: While ceramics are brittle and have low tensile strength, their high compressive strength makes them suitable for withstanding the forces of chewing and biting.
- Biocompatibility: Dental ceramics are non-reactive and biocompatible, making them safe for long-term use in the oral environment.
-
Material Selection Considerations:
- Location of Restoration: Materials like zirconia are preferred for posterior teeth due to their strength, while feldspathic porcelain is often used for anterior teeth for its aesthetic qualities.
- Patient Preferences: Factors such as budget and desired appearance (e.g., metal-free options) influence the choice of ceramic material.
- Dentist’s Recommendation: The dentist’s expertise and the specific clinical requirements of the case play a crucial role in material selection.
By understanding the materials and processes involved in dental ceramics, patients and practitioners can make informed decisions to achieve functional, durable, and aesthetically pleasing dental restorations.
Summary Table:
Component | Role in Dental Ceramics |
---|---|
Clay and Kaolin | Base structure, enhances workability and firing properties. |
Feldspar | Acts as a flux, lowers melting temperature, and promotes vitrification for a durable finish. |
Soapstone | Improves thermal stability and chemical resistance. |
Alumina | Enhances mechanical strength and fracture resistance. |
Zirconium | Provides exceptional strength, biocompatibility, and a natural tooth-like appearance. |
Ready to learn more about dental ceramics? Contact our experts today for personalized advice!