Debinding is a critical step in manufacturing processes such as Metal Injection Molding (MIM) and technical ceramics, where organic binders are removed from the green body to prepare it for sintering. The primary methods of debinding include thermal debinding, solvent debinding, and supercritical fluid (SCF) debinding. Each method involves distinct mechanisms, such as evaporation, degradation, or dissolution, and requires precise control of temperature, pressure, and atmosphere to avoid defects like warping or cracking. The choice of method depends on the material, binder composition, and desired outcomes.
Key Points Explained:
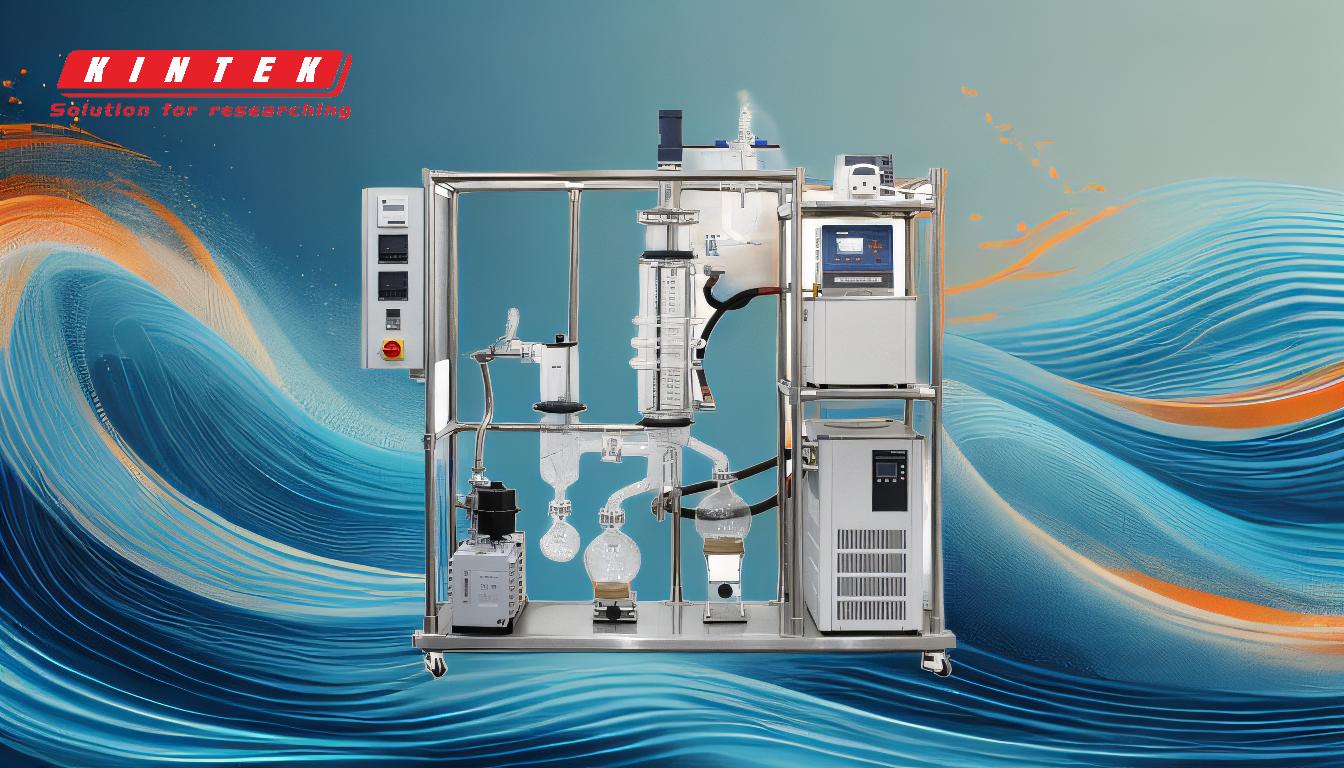
-
Thermal Debinding
- Mechanism: Thermal debinding relies on heating the material to a temperature where the binder evaporates or degrades. This process typically occurs between 150°C and 600°C (300°F to 1110°F).
- Process Details: The binder, often a mixture of organic compounds with varying melting points, is gradually removed through controlled heating. A nitrogen purge is often used to reduce oxygen content in the furnace, preventing oxidation and contamination.
- Advantages: This method is straightforward and widely used due to its simplicity and compatibility with many materials.
- Challenges: Careful control of temperature and atmosphere is required to avoid defects such as warping, cracking, or incomplete binder removal. Multiple heating cycles may be necessary to ensure complete removal of all binder traces.
-
Solvent Debinding
- Mechanism: Solvent debinding involves immersing the part in a solvent that dissolves the binder. The dissolved binder is then removed from the part, leaving behind a porous structure.
- Process Details: The part is submerged in a debinding fluid, which selectively dissolves the binder without affecting the material's integrity. The solvent is then evaporated or drained, and the part is dried.
- Advantages: Solvent debinding is faster than thermal debinding and can remove a significant portion of the binder before thermal treatment, reducing the risk of defects.
- Challenges: The choice of solvent is critical, as it must be compatible with the binder and the material. Additionally, solvent handling and disposal require careful management to ensure safety and environmental compliance.
-
Supercritical Fluid (SCF) Debinding
- Mechanism: SCF debinding uses supercritical fluids, typically carbon dioxide, to dissolve and remove the binder. In the supercritical state, the fluid has properties of both a liquid and a gas, enabling efficient penetration and dissolution of the binder.
- Process Details: The part is placed in a high-pressure chamber, and supercritical CO2 is introduced. The binder dissolves into the fluid, which is then depressurized, causing the CO2 to revert to a gaseous state and leaving behind a clean part.
- Advantages: SCF debinding is highly efficient and environmentally friendly, as CO2 is non-toxic and can be recycled. It also allows for precise control over the debinding process.
- Challenges: The equipment required for SCF debinding is more complex and expensive compared to thermal or solvent methods. Additionally, the process may not be suitable for all binder types.
-
Combination of Methods
- Hybrid Approach: In some cases, a combination of debinding methods is used to optimize the process. For example, solvent debinding may be followed by thermal debinding to ensure complete binder removal.
- Benefits: This approach leverages the strengths of each method, such as the speed of solvent debinding and the thoroughness of thermal debinding, while minimizing their respective limitations.
-
Process Control and Considerations
- Temperature Profile: The temperature must be carefully controlled to avoid thermal shock or uneven binder removal, which can lead to defects.
- Atmosphere Control: The use of inert gases like nitrogen helps prevent oxidation and contamination during thermal debinding.
- Multiple Passes: In some cases, multiple passes through the furnace or solvent bath are required to ensure complete binder removal, as even trace amounts can negatively impact the sintering phase.
By understanding these methods and their respective advantages and challenges, manufacturers can select the most appropriate debinding technique for their specific application, ensuring high-quality results and efficient production processes.
Summary Table:
Debinding Method | Mechanism | Advantages | Challenges |
---|---|---|---|
Thermal Debinding | Binder evaporates or degrades with heat | Simple, widely compatible with materials | Requires precise temperature and atmosphere control to avoid defects |
Solvent Debinding | Binder dissolves in a solvent | Faster than thermal debinding, reduces defect risk | Solvent compatibility and environmental handling are critical |
Supercritical Fluid (SCF) | Binder dissolves in supercritical CO2 | Efficient, environmentally friendly, precise control | Expensive equipment, may not suit all binder types |
Combination Methods | Hybrid approach (e.g., solvent + thermal) | Leverages strengths of multiple methods, minimizes limitations | Requires careful process integration and control |
Need help choosing the right debinding method for your application? Contact our experts today for tailored solutions!