Thin film deposition is a critical process in various industries, particularly in electronics, optics, and nanotechnology. The methods used for depositing thin films can be broadly categorized into two main types: Chemical Vapor Deposition (CVD) and Physical Vapor Deposition (PVD). CVD techniques involve chemical reactions to form thin films, while PVD techniques rely on physical processes like vaporization and condensation. Each method has its own set of techniques, such as sputtering, evaporation, and atomic layer deposition, which are chosen based on the desired film properties, substrate material, and application requirements. These methods are essential for producing high-quality, precise, and durable thin films used in advanced technologies.
Key Points Explained:
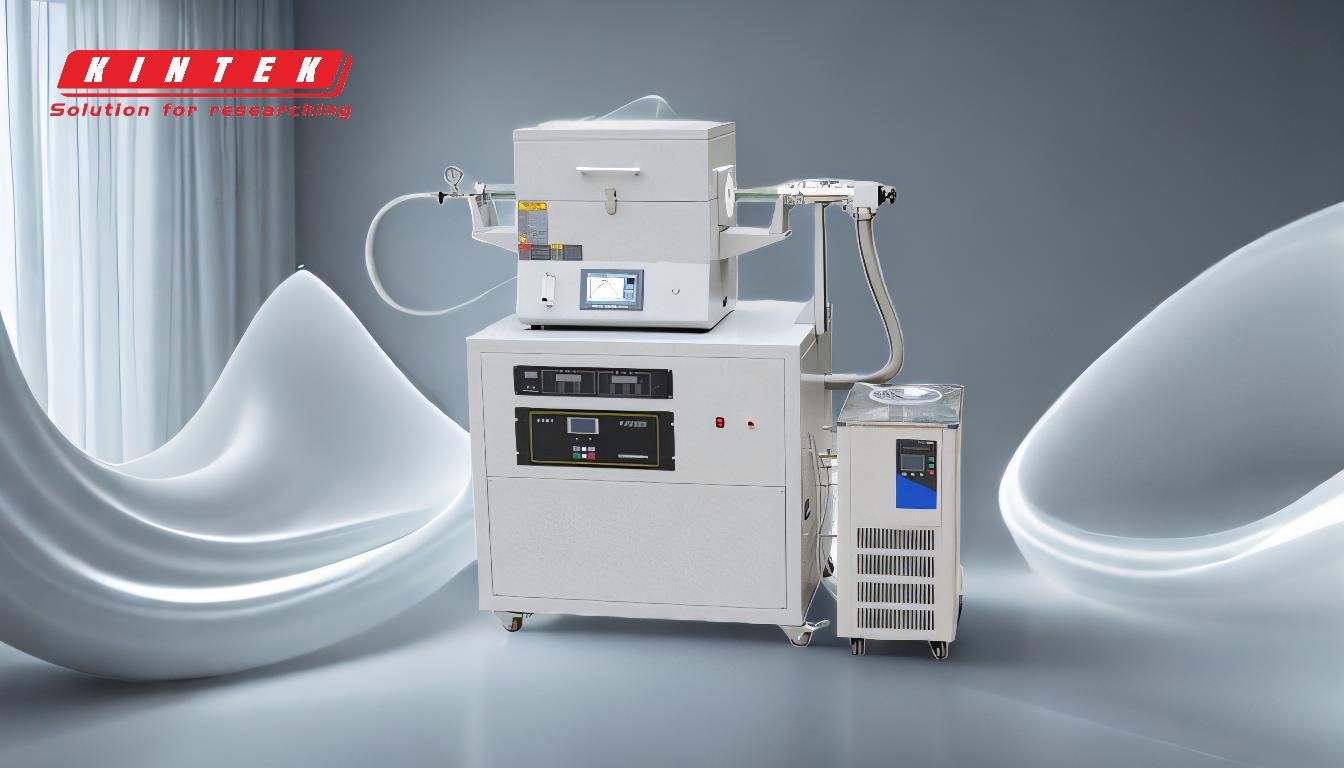
1. Chemical Vapor Deposition (CVD)
- Definition: CVD involves the use of chemical reactions to deposit thin films onto a substrate. The process typically occurs in a controlled environment where precursor gases react to form a solid film on the substrate.
-
Techniques:
- Chemical Bath Deposition: A simple and cost-effective method where the substrate is immersed in a chemical solution, leading to the deposition of a thin film.
- Electroplating: This method uses an electric current to reduce dissolved metal cations, forming a coherent metal coating on the substrate.
- Molecular Beam Epitaxy (MBE): A highly controlled process where beams of atoms or molecules are directed at the substrate to grow thin films layer by layer.
- Thermal Oxidation: A process where the substrate is exposed to an oxidizing environment at high temperatures, forming an oxide layer on the surface.
- Plasma-Enhanced CVD (PECVD): This technique uses plasma to enhance the chemical reaction rates, allowing for lower temperature deposition.
- Atomic Layer Deposition (ALD): A precise method where thin films are deposited one atomic layer at a time, offering excellent control over film thickness and uniformity.
2. Physical Vapor Deposition (PVD)
- Definition: PVD involves the physical transfer of material from a source to a substrate, typically in a vacuum environment. The material is vaporized from a solid or liquid source and then condenses on the substrate to form a thin film.
-
Techniques:
-
Evaporation:
- Thermal Evaporation: The target material is heated until it vaporizes, and the vapor then condenses on the substrate.
- Electron Beam Evaporation: An electron beam is used to heat the target material, causing it to evaporate and deposit onto the substrate.
-
Sputtering:
- Magnetron Sputtering: A widely used technique where a plasma is created to dislodge atoms from a target material, which then deposit onto the substrate. This method is known for producing high-purity films with low defect levels.
- Ion Beam Sputtering: A high-energy ion beam is directed at the target material, causing atoms to be ejected and deposited onto the substrate.
- Pulsed Laser Deposition (PLD): A high-energy laser pulse is used to ablate material from a target, which then deposits onto the substrate.
- Carbon Coating: A specialized form of PVD where carbon is vaporized and deposited onto the substrate, often used for creating conductive or protective coatings.
-
Evaporation:
3. Comparison of CVD and PVD
- CVD is generally preferred for applications requiring high-quality, uniform films with excellent step coverage (ability to coat uneven surfaces). It is widely used in semiconductor manufacturing and for creating complex multi-layer structures.
- PVD is often chosen for applications requiring high-purity films, such as in optics and nanotechnology. It is also favored for its ability to deposit a wide range of materials, including metals, alloys, and ceramics.
4. Selection Criteria for Deposition Methods
- Film Properties: The choice of deposition method depends on the desired film properties, such as thickness, uniformity, purity, and adhesion.
- Substrate Material: The substrate material and its thermal stability can influence the choice of deposition method. For example, PVD is often preferred for temperature-sensitive substrates.
- Application Requirements: The specific application, whether in electronics, optics, or protective coatings, will dictate the most suitable deposition technique.
5. Emerging Trends in Thin Film Deposition
- Atomic Layer Deposition (ALD): ALD is gaining popularity due to its ability to deposit ultra-thin, highly uniform films with atomic-level precision. It is particularly useful in nanotechnology and semiconductor applications.
- Hybrid Techniques: Combining CVD and PVD methods, or integrating other advanced techniques like plasma treatment, is becoming more common to achieve films with tailored properties.
In conclusion, the deposition of thin films is a complex and highly specialized field that relies on a variety of techniques, each with its own advantages and limitations. Understanding the differences between CVD and PVD, as well as the specific techniques within each category, is crucial for selecting the right method for a given application. As technology advances, new and hybrid methods are likely to emerge, further expanding the possibilities for thin film deposition.
Summary Table:
Method | Techniques | Applications |
---|---|---|
CVD | Chemical Bath Deposition, Electroplating, MBE, Thermal Oxidation, PECVD, ALD | Semiconductor manufacturing, complex multi-layer structures, uniform coatings |
PVD | Thermal Evaporation, Electron Beam Evaporation, Magnetron Sputtering, PLD | Optics, nanotechnology, high-purity films, conductive/protective coatings |
Discover the best thin film deposition method for your needs—contact our experts today!