Pyrolysis is a thermal decomposition process that occurs at elevated temperatures in the absence of oxygen or with limited oxygen supply. The pressure conditions during pyrolysis vary depending on the type of pyrolysis (e.g., fast pyrolysis, flash pyrolysis, or high-temperature pyrolysis) and the desired end products. Generally, pyrolysis pressures range from atmospheric pressure (1 bar) to moderately elevated pressures (up to 30 bar). Fast pyrolysis, which maximizes bio-oil production, typically operates at moderate pressures, while high-temperature pyrolysis for gaseous or liquid species may involve higher pressures. The choice of pressure is influenced by factors such as the feedstock, reactor design, and the specific pyrolysis process being employed.
Key Points Explained:
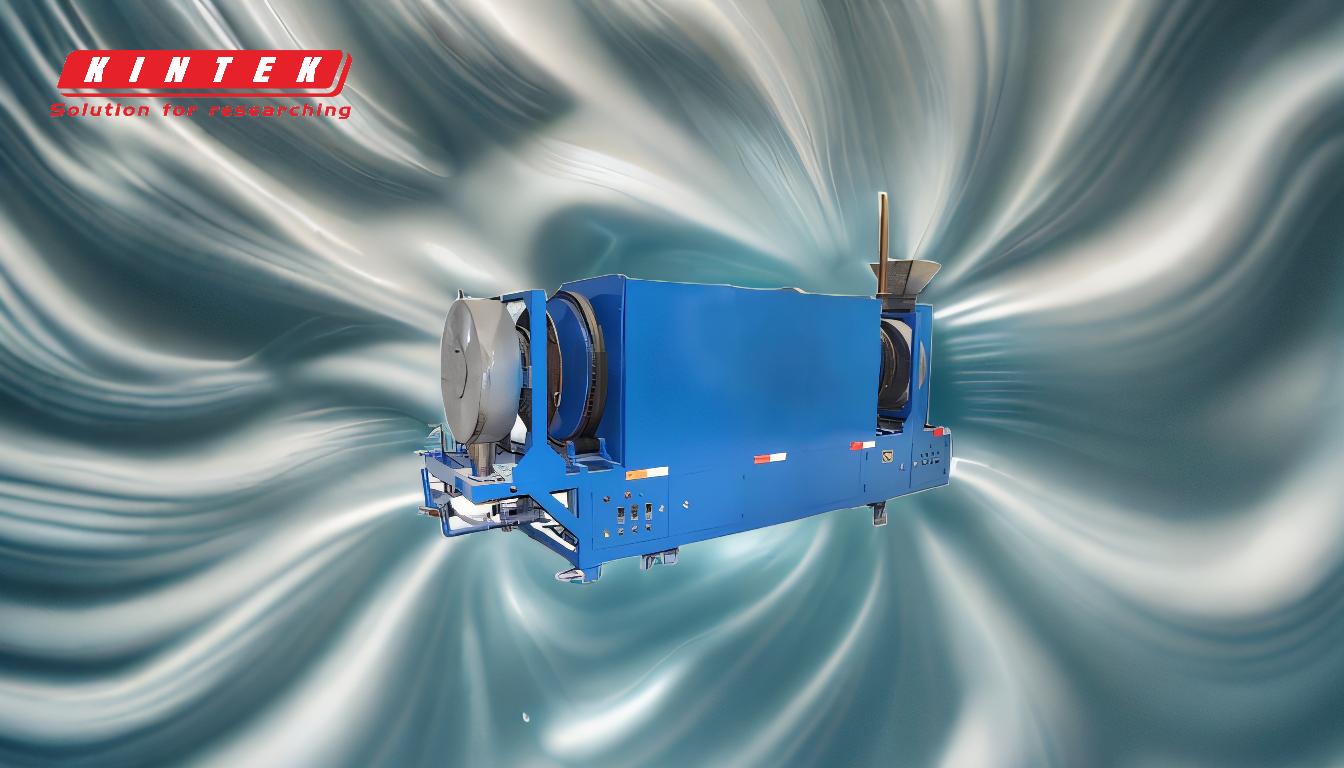
-
Pressure Ranges in Pyrolysis:
- Atmospheric Pressure (1 bar): Many pyrolysis processes, especially fast pyrolysis, are conducted at or near atmospheric pressure to simplify reactor design and reduce costs. This is particularly common in processes aimed at producing bio-oil, where rapid heating and cooling are prioritized.
- Moderate Pressures (1–30 bar): High-temperature pyrolysis processes, especially those involving liquid or gaseous species, often operate at elevated pressures. These pressures help control the reaction kinetics and improve the yield of desired products, such as syngas or bio-oil.
-
Influence of Pressure on Pyrolysis Outcomes:
- Bio-Oil Production: In fast pyrolysis, lower pressures (around 1 bar) are typically used to maximize bio-oil yields. The rapid heating and short residence times at these pressures help prevent secondary reactions that could degrade the bio-oil.
- Gas and Liquid Production: Higher pressures (up to 30 bar) are often employed in high-temperature pyrolysis to enhance the production of gaseous and liquid species. Elevated pressures can improve the efficiency of heat transfer and reaction rates, leading to higher yields of syngas or other valuable byproducts.
-
Reactor Design and Pressure Considerations:
- Fast Pyrolysis Reactors: These reactors are designed to operate at or near atmospheric pressure to facilitate rapid heating and quenching of biomass particles. The focus is on achieving high heating rates (up to 1000 °C/s) and short residence times (less than 2 seconds).
- High-Temperature Pyrolysis Reactors: These reactors, often made of refractory alloys, are designed to withstand higher pressures (up to 30 bar) and temperatures (700–1200 °C). The elevated pressures help maintain the stability of the reactor and improve the efficiency of the pyrolysis process.
-
Interaction Between Pressure and Other Factors:
- Temperature: Pressure and temperature are closely linked in pyrolysis. Higher pressures can allow for higher temperatures, which can improve the breakdown of complex molecules and increase the yield of gaseous or liquid products.
- Residence Time: The pressure in the reactor can influence the residence time of the pyrolysis vapors. Higher pressures may increase the residence time, which can affect the quality and composition of the final products.
- Atmosphere: The pressure conditions are often chosen in conjunction with the reactor atmosphere (e.g., inert, vacuum, or limited oxygen). For example, operating under vacuum can reduce the pressure and prevent unwanted side reactions like combustion.
-
Practical Implications for Equipment and Consumables:
- Material Selection: Reactors operating at higher pressures require materials that can withstand the increased stress and temperature. Refractory alloys are commonly used for high-pressure pyrolysis reactors.
- Safety Considerations: Higher pressures necessitate robust safety measures, including pressure relief systems and monitoring equipment, to prevent accidents.
- Cost Implications: Operating at higher pressures can increase the cost of the pyrolysis system due to the need for more durable materials and safety features. However, the improved yields and product quality may justify the additional expense.
In summary, the pressure conditions in pyrolysis are highly dependent on the specific process and desired outcomes. Fast pyrolysis typically operates at or near atmospheric pressure to maximize bio-oil production, while high-temperature pyrolysis may involve higher pressures to enhance the yield of gaseous or liquid species. The choice of pressure is influenced by factors such as reactor design, feedstock, and the interaction with other process parameters like temperature and residence time.
Summary Table:
Pressure Range | Application | Key Benefits |
---|---|---|
1 bar (Atmospheric) | Fast Pyrolysis | Maximizes bio-oil yield, rapid heating, cost-effective |
1–30 bar (Moderate) | High-Temperature Pyrolysis | Enhances gaseous/liquid species, improves reaction kinetics |
Factor | Impact on Pyrolysis |
---|---|
Temperature | Higher pressures allow higher temperatures for better breakdown |
Residence Time | Influences vapor quality and composition |
Atmosphere | Inert or vacuum conditions prevent unwanted reactions |
Need help optimizing your pyrolysis process? Contact our experts today!