Preventive maintenance of hydraulic systems is essential to ensure their longevity, efficiency, and reliability. It involves regular inspections, monitoring, and servicing to prevent unexpected failures and costly downtime. Key practices include checking fluid levels, inspecting hoses and seals, monitoring system pressure, and ensuring cleanliness to avoid contamination. By adhering to a structured maintenance schedule, operators can identify potential issues early, reduce wear and tear, and maintain optimal performance. This proactive approach not only extends the lifespan of hydraulic components but also enhances safety and operational efficiency.
Key Points Explained:
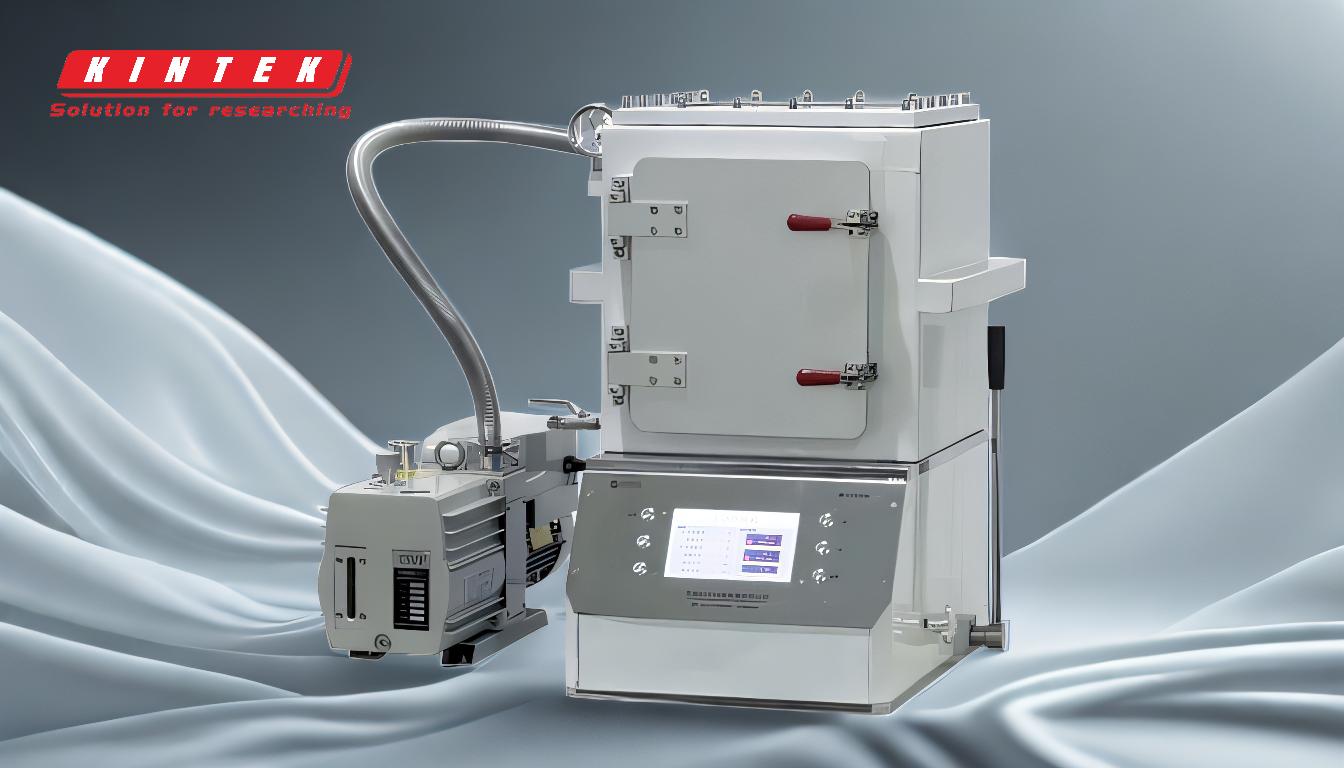
-
Regular Fluid Checks and Replacement
- Hydraulic fluid is the lifeblood of the system, and its condition directly impacts performance. Regularly check fluid levels and top up as necessary.
- Monitor fluid quality for signs of contamination, such as discoloration or debris. Contaminated fluid can cause damage to internal components.
- Replace hydraulic fluid at recommended intervals to maintain viscosity and lubrication properties. This prevents overheating and reduces wear on moving parts.
-
Inspection of Hoses, Seals, and Fittings
- Inspect hoses for cracks, abrasions, or leaks, as damaged hoses can lead to fluid loss and system failure.
- Check seals and fittings for wear or looseness, which can cause leaks and pressure drops.
- Replace worn-out components promptly to prevent catastrophic failures and ensure system integrity.
-
Monitoring System Pressure
- Regularly check hydraulic system pressure to ensure it operates within the recommended range. Abnormal pressure levels can indicate issues such as blockages or pump malfunctions.
- Use pressure gauges and sensors to monitor performance and detect anomalies early.
-
Preventing Contamination
- Keep the hydraulic system clean by using proper filtration systems and ensuring all components are free from dirt and debris.
- Use clean tools and equipment during maintenance to avoid introducing contaminants.
- Regularly inspect and replace filters to maintain fluid cleanliness.
-
Lubrication of Moving Parts
- Ensure all moving parts, such as cylinders and valves, are adequately lubricated to reduce friction and wear.
- Use the correct type of lubricant as specified by the manufacturer to avoid compatibility issues.
-
Scheduled Inspections and Maintenance
- Follow a preventive maintenance schedule that includes routine inspections, component replacements, and system testing.
- Document all maintenance activities to track system performance and identify recurring issues.
-
Training and Awareness
- Train operators and maintenance personnel on proper hydraulic system operation and maintenance procedures.
- Encourage a proactive approach to identifying and addressing potential issues before they escalate.
By implementing these preventive maintenance practices, hydraulic systems can operate efficiently, minimize downtime, and extend their service life. Regular attention to fluid quality, component integrity, and system cleanliness ensures reliable performance and reduces the risk of unexpected failures.
Summary Table:
Key Maintenance Practices | Details |
---|---|
Regular Fluid Checks | Monitor levels, quality, and replace fluid to prevent contamination. |
Inspect Hoses, Seals, Fittings | Check for wear, leaks, and replace damaged components promptly. |
Monitor System Pressure | Ensure pressure is within range to detect blockages or pump issues early. |
Prevent Contamination | Use proper filtration, clean tools, and replace filters regularly. |
Lubricate Moving Parts | Use correct lubricants to reduce friction and wear. |
Scheduled Inspections | Follow a structured maintenance schedule and document all activities. |
Training and Awareness | Train personnel to identify and address issues proactively. |
Ensure your hydraulic systems run smoothly—contact our experts today for tailored maintenance solutions!