Diamond-like carbon (DLC) coating is a versatile material known for its exceptional properties, making it highly suitable for wear-protective and friction-reducing applications. It combines high hardness, low coefficient of friction, chemical inertness, and excellent surface smoothness. The material's unique structure, consisting of both sp3 (diamond-like) and sp2 (graphite-like) carbon bonds, allows for tailored properties based on the bonding content. DLC coatings are widely used in industries requiring durability, corrosion resistance, and enhanced sliding properties. The ability to control deposition parameters further enables customization of characteristics such as grain size, surface roughness, and crystallinity.
Key Points Explained:
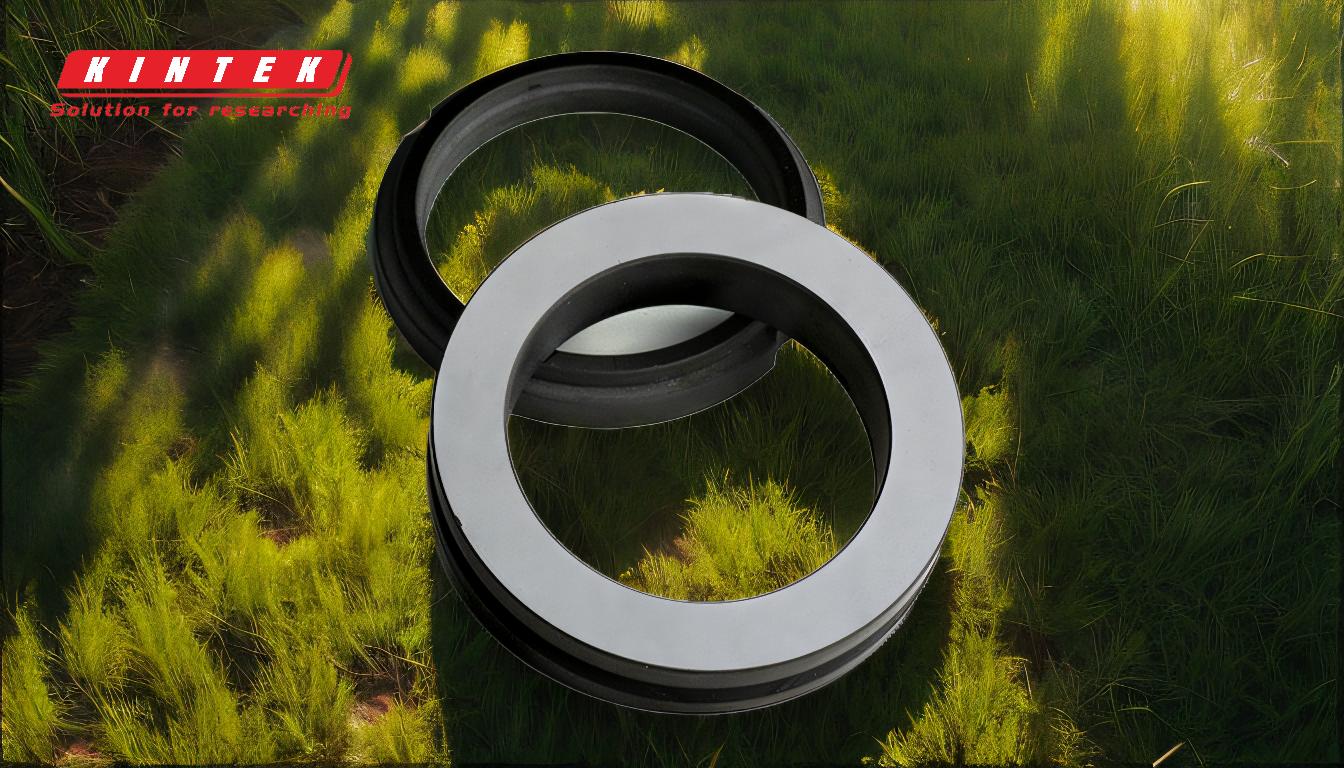
-
High Hardness
- DLC coatings exhibit exceptional hardness, comparable to that of diamond, due to the presence of sp3 carbon bonds.
- This hardness makes DLC coatings ideal for wear-resistant applications, such as in automotive components, cutting tools, and industrial machinery.
- The hardness can be tailored by adjusting the sp3-to-sp2 bonding ratio during the deposition process.
-
Low Coefficient of Friction
- DLC coatings have a low coefficient of friction, which reduces wear and energy loss in sliding or rotating components.
- This property is particularly beneficial in applications like engine parts, bearings, and medical devices, where minimizing friction is critical.
- The low friction is attributed to the presence of sp2 (graphite-like) bonds, which provide a lubricating effect.
-
Chemical Inertness
- DLC coatings are chemically inert, meaning they resist reactions with most chemicals and corrosive substances.
- This property makes them suitable for use in harsh environments, such as chemical processing equipment or marine applications.
- The inertness also contributes to the coating's longevity and stability over time.
-
High Surface Smoothness
- DLC coatings are known for their high surface smoothness, which reduces surface irregularities and enhances performance in sliding or rotating applications.
- This smoothness is achieved through precise deposition techniques and contributes to the coating's low friction and wear resistance.
- It also improves the aesthetic appearance of coated components.
-
Thermal Conductivity
- DLC coatings exhibit excellent thermal conductivity, which helps dissipate heat efficiently in high-temperature applications.
- This property is particularly useful in electronic components, cutting tools, and engine parts, where heat management is critical.
- The thermal conductivity can be optimized by controlling the deposition parameters and bonding structure.
-
Tailorable Properties
- The properties of DLC coatings, such as hardness, friction coefficient, and surface roughness, can be tailored by adjusting the sp3-to-sp2 bonding ratio and deposition parameters.
- This flexibility allows for customization based on specific application requirements, such as enhanced durability, reduced friction, or improved corrosion resistance.
- The ability to control grain size, crystallinity, and surface roughness further enhances the coating's performance.
-
Durability and Wear Resistance
- DLC coatings are highly durable and resistant to wear, making them suitable for long-term use in demanding applications.
- The combination of high hardness, low friction, and chemical inertness ensures that the coatings maintain their performance even under extreme conditions.
- This durability reduces maintenance costs and extends the lifespan of coated components.
-
Applications in Corrosive Environments
- Due to their chemical inertness and corrosion resistance, DLC coatings are widely used in corrosive environments, such as offshore drilling equipment, chemical processing plants, and medical devices.
- The coatings protect underlying materials from degradation, ensuring reliable performance and reducing the need for frequent replacements.
-
Enhanced Sliding Properties
- DLC coatings are specifically designed to enhance sliding properties, making them ideal for applications involving moving parts, such as gears, pistons, and bearings.
- The low friction and high hardness of the coatings reduce wear and improve efficiency in these applications.
-
Metastable Amorphous Structure
- DLC is a metastable form of amorphous carbon or hydrogenated amorphous carbon, containing a significant fraction of sp3 bonds.
- This unique structure gives DLC its combination of diamond-like and graphite-like properties, making it a versatile material for various industrial applications.
- The metastable nature allows for precise control over the coating's characteristics through deposition techniques.
In summary, DLC coatings are a highly effective solution for applications requiring wear resistance, low friction, chemical inertness, and durability. Their tailorable properties and excellent performance in harsh environments make them a preferred choice across multiple industries.
Summary Table:
Property | Description |
---|---|
High Hardness | Comparable to diamond, ideal for wear-resistant applications like cutting tools. |
Low Friction | Reduces wear and energy loss in sliding or rotating components. |
Chemical Inertness | Resists reactions with chemicals, suitable for harsh environments. |
Surface Smoothness | Enhances performance and aesthetics in sliding applications. |
Thermal Conductivity | Efficient heat dissipation for high-temperature applications. |
Tailorable Properties | Customizable hardness, friction, and surface roughness for specific needs. |
Durability | Long-lasting performance in extreme conditions, reducing maintenance costs. |
Corrosion Resistance | Protects materials in corrosive environments like offshore drilling. |
Enhanced Sliding | Improves efficiency in moving parts like gears and bearings. |
Metastable Structure | Combines diamond-like and graphite-like properties for versatility. |
Unlock the potential of DLC coatings for your applications—contact our experts today!