Physical Vapor Deposition (PVD) is a collection of vacuum-based techniques used to deposit thin films onto substrates. These methods involve transforming a solid or liquid material into a vapor phase, which then condenses onto a target surface to form a thin film. PVD techniques are widely used in industries requiring precise, high-quality coatings for mechanical, optical, chemical, or electronic applications. The most common PVD methods include sputtering, thermal evaporation, e-beam evaporation, pulsed laser deposition (PLD), and cathodic arc deposition. Each technique has unique mechanisms and applications, making PVD a versatile and essential process in modern manufacturing and material science.
Key Points Explained:
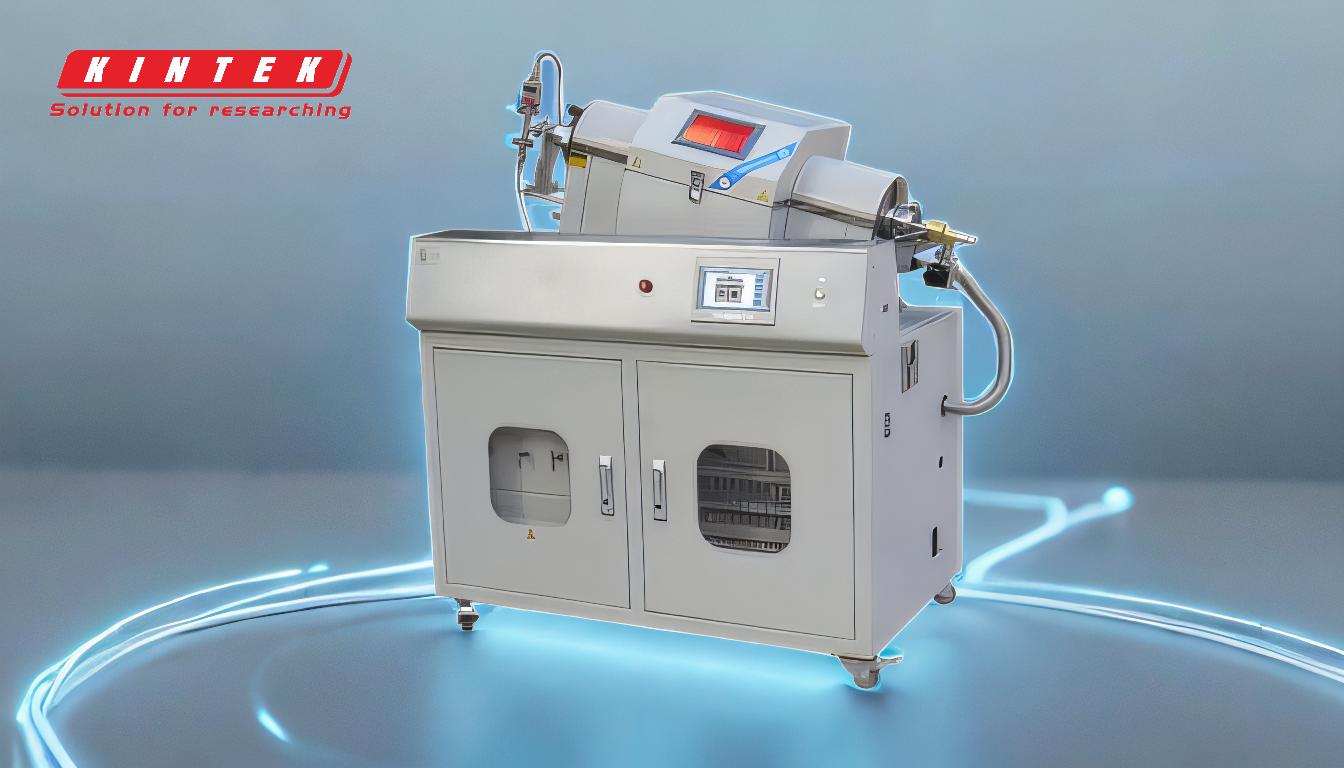
-
Overview of PVD Techniques:
- PVD is a group of vacuum deposition methods that transition a material from a condensed phase (solid or liquid) to a vapor phase and then back to a thin film on a substrate.
- These techniques are used to create thin films with specific mechanical, optical, chemical, or electronic properties.
- PVD processes are conducted in vacuum environments to minimize contamination and ensure precise control over film properties.
-
Common PVD Techniques:
-
Sputtering:
- Sputtering involves bombarding a target material with high-energy ions (usually from a plasma) to dislodge atoms from the target surface.
- The ejected atoms then deposit onto a substrate to form a thin film.
- This method is widely used due to its ability to deposit a wide range of materials, including metals, alloys, and ceramics, with excellent adhesion and uniformity.
-
Thermal Evaporation:
- In thermal evaporation, the target material is heated to its vaporization point using resistive heating or electron beams.
- The vaporized material then condenses onto the substrate to form a thin film.
- This technique is simple and cost-effective but is typically limited to materials with relatively low melting points.
-
Electron Beam (e-Beam) Evaporation:
- e-Beam evaporation uses a focused electron beam to heat and vaporize the target material.
- This method is suitable for materials with high melting points and allows for precise control over deposition rates and film thickness.
-
Pulsed Laser Deposition (PLD):
- PLD involves using a high-power laser pulse to ablate material from a target, creating a vapor plume that deposits onto the substrate.
- This technique is particularly useful for depositing complex materials, such as oxides and superconductors, with high stoichiometric accuracy.
-
Cathodic Arc Deposition:
- In this method, an electric arc is used to vaporize material from a cathode target.
- The vaporized material forms a plasma, which then deposits onto the substrate.
- Cathodic arc deposition is known for producing dense, high-quality coatings but can generate macro-particles that affect film quality.
-
Sputtering:
-
Key Components and Processes in PVD:
-
Vacuum Environment:
- PVD processes are conducted in vacuum chambers to reduce background gases that could interfere with the deposition process.
- Lowering the pressure minimizes chemical reactions between the vaporized material and residual gases, ensuring high-purity films.
-
Material Vaporization:
- The target material is vaporized using methods such as heating, sputtering, or laser ablation.
- The choice of vaporization method depends on the material properties and desired film characteristics.
-
Film Deposition:
- The vaporized material is transported through the vacuum or plasma environment and condenses onto the substrate.
- The deposition rate and film thickness are controlled using tools like quartz crystal rate monitors.
-
Substrate Preparation:
- Substrates are often cleaned and treated to improve adhesion and film quality.
- Surface treatments may include plasma cleaning or the application of adhesion-promoting layers.
-
Vacuum Environment:
-
Applications of PVD Techniques:
-
Mechanical Coatings:
- PVD is used to deposit wear-resistant, hard coatings (e.g., titanium nitride) on tools, molds, and machine components.
-
Optical Coatings:
- Thin films with specific optical properties, such as anti-reflective or reflective coatings, are applied to lenses, mirrors, and displays.
-
Electronic and Semiconductor Coatings:
- PVD is used to deposit conductive, insulating, or semiconducting layers in microelectronics and semiconductor devices.
-
Decorative Coatings:
- PVD coatings are applied to consumer products (e.g., watches, jewelry, and automotive trim) to enhance appearance and durability.
-
Mechanical Coatings:
-
Advantages of PVD:
- High-quality, dense, and adherent films.
- Precise control over film composition, thickness, and properties.
- Environmentally friendly compared to some chemical deposition methods.
- Compatibility with a wide range of materials and substrates.
-
Challenges and Considerations:
- High equipment and operational costs due to vacuum requirements.
- Limited deposition rates compared to some chemical vapor deposition (CVD) techniques.
- Potential for defects, such as macro-particles in cathodic arc deposition or uneven coatings in thermal evaporation.
By understanding these key points, equipment and consumable purchasers can make informed decisions about selecting the appropriate PVD technique for their specific application, ensuring optimal performance and cost-effectiveness.
Summary Table:
Aspect | Details |
---|---|
Common PVD Techniques | Sputtering, Thermal Evaporation, e-Beam Evaporation, PLD, Cathodic Arc |
Key Components | Vacuum Environment, Material Vaporization, Film Deposition, Substrate Prep |
Applications | Mechanical, Optical, Electronic, Decorative Coatings |
Advantages | High-quality films, precise control, eco-friendly, material compatibility |
Challenges | High costs, limited deposition rates, potential defects |
Discover the right PVD solution for your needs—contact our experts today!